Active magnesium oxide, also known as light-burned magnesium oxide or caustic magnesium oxide, is mainly produced by calcining magnesium compounds at relatively low temperatures (usually below 900°C). This process decomposes the raw materials into magnesium oxide and may be accompanied by the release of water or carbon dioxide. The following are several common processes for preparing active magnesium oxide:
1 Dolomite carbonization method:
• Dolomite or magnesite is calcined and reacted with water to produce Mg(OH)2 and Ca(OH)2.
• Carbonization treatment is carried out using CO2 to obtain magnesium bicarbonate and by-product calcium carbonate.
• Calcium carbonate is separated and removed, and then the remaining mother liquor is pyrolyzed to obtain basic magnesium carbonate, and finally calcined at about 800°C for 1 to 2 hours to obtain active magnesium oxide.
2 Brine-ammonia method:
• Ammonia is introduced into the brine to convert magnesium salts into magnesium hydroxide precipitates.
• After filtering, washing, crushing and drying, the magnesium hydroxide is sent to a rotary calcining furnace.
• The calcination temperature is controlled at about 500℃ for 2 hours to prepare active magnesium oxide.
3 Brine-ammonium carbonate method:
• Add ammonium carbonate solution to brine and heat to precipitate basic magnesium carbonate.
• The precipitate is filtered, washed, dried, crushed and calcined to finally obtain active magnesium oxide.
Due to its special chemical and physical properties, active magnesium oxide is widely used in many fields:
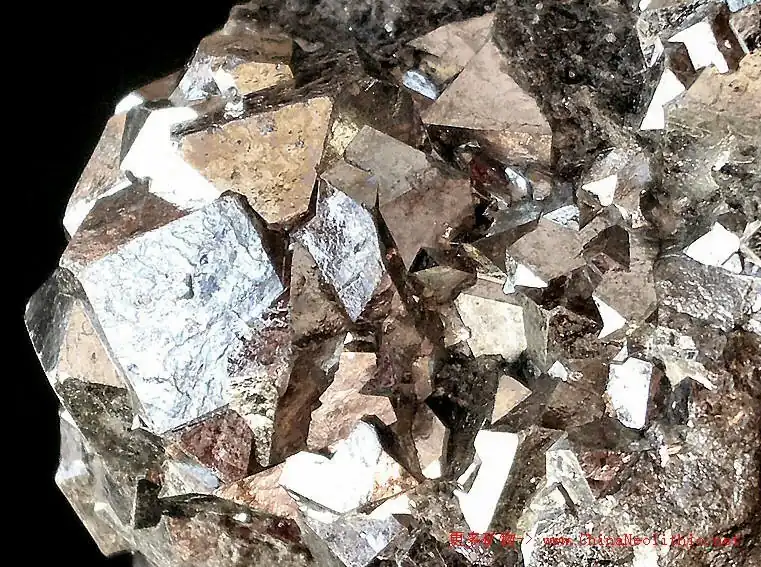
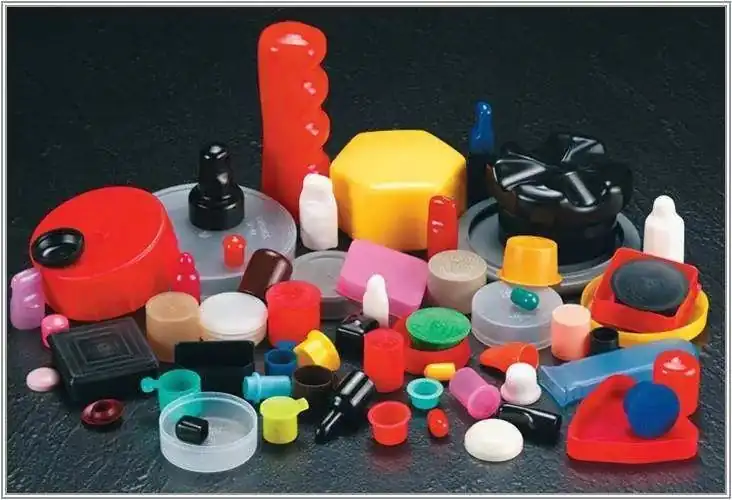
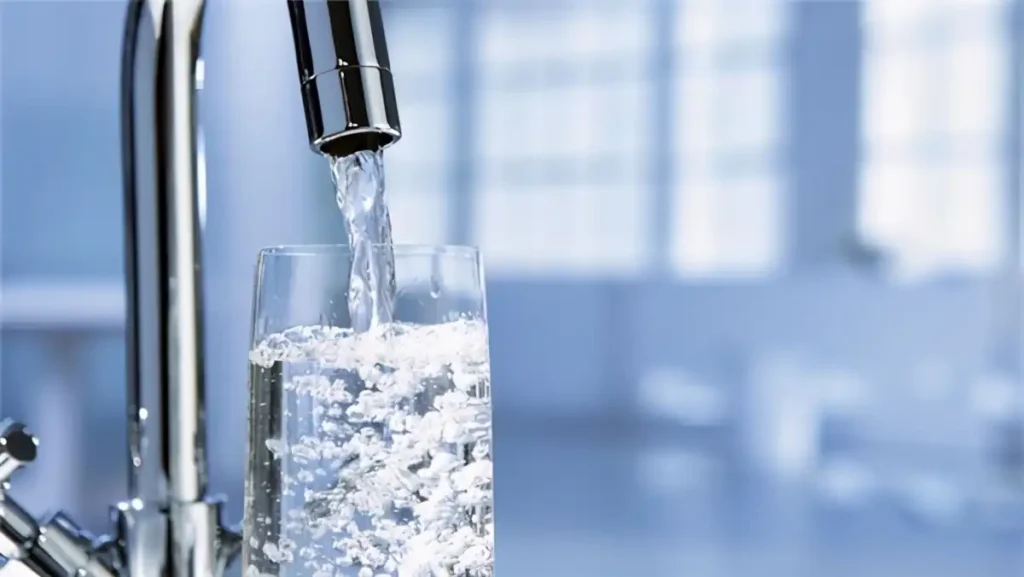
• Environmental protection field: used for waste gas and wastewater treatment, it can effectively adsorb and neutralize harmful gases such as sulfur dioxide, nitrogen oxides and heavy metal ions.
• Metallurgical industry: as a desulfurizer in the steelmaking process, it helps to convert sulfides into more easily handled sulfates.
• Chemical materials: as a key raw material for the preparation of high-functional fine inorganic materials, electronic components, inks, and harmful gas adsorbents.
• Rubber and plastic industry: as a rubber accelerator and activator, as well as a filler for plastics and rubber products, it improves the performance and heat resistance of products.
• Others: It can also be used as filler for paint, paper, cosmetics, and other advanced materials under special conditions (such as high temperature, high corrosion environment).
Its iodine absorption value (a measure of its activity) is usually between 120-180 mg/g, which makes it highly efficient in specific chemical reactions and adsorption processes.