Is Magnesium Oxide (MgO) a Refractory Material?
In the refractory industry, one of the materials widely used is magnesia. It is chemically known as magnesium oxide (MgO). Magnesium oxide is a choice material because of its impressively high thermal and low electric conductivities, which are highly coveted properties in refractory materials. So, yes, magnesium oxide is indeed a refractory material. In this post, we will discuss what magnesium oxide is, its properties, and its application as a refractory material.
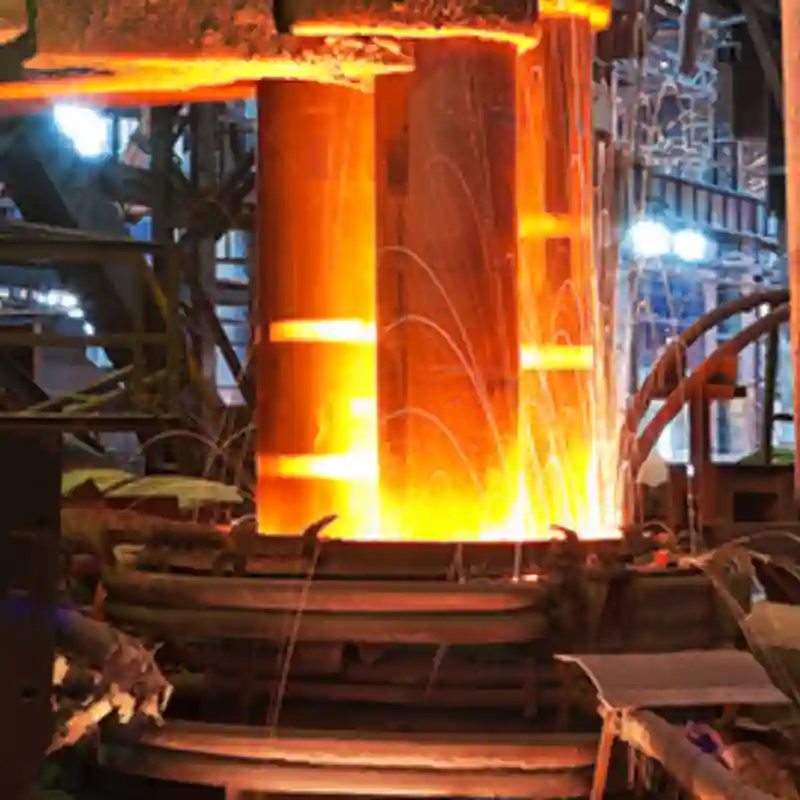
Refractory application of magnesium oxide
Refractory materials are materials that can withstand very high temperatures (above 1,000°F or 538°C), which is typical of many manufacturing processes. They help preserve the industrial processes where heat is encountered. Refractory materials are more heat-resistant than metals. These materials are used to line the hot surfaces inside industrial production plants. Magnesium oxide is one such material.
It is used as a basic refractory material for crucibles and many industrial processes. The properties discussed above all contribute to the use of magnesia (MgO) as a refractory material. It has a wide availability and is relatively affordable. This makes magnesium oxide (MgO) the choice refractory material for heat-intensive metal, glass, and fired-ceramic applications.
Magnesium oxide is also used as an insulator in heat-resistant electrical cables. In ceramics, magnesium oxide doping is effective for inhibiting grain growth in ceramics and improving their fracture toughness.
Aside from its application as a refractory, magnesium oxide is widely used in many other applications, such as agricultural, mining, catalysts, power generation, pulp bleaching, wastewater treatment, etc.
What are the requirements for refractory materials?
Below are some essential requirements for selecting refractory materials:
- It must be able to withstand high temperatures.
- It must not conduct much heat.
- It should have a stable volume, i.e., does not undergo thermal expansion when exposed to high temperatures. In other words, it should have a low coefficient of thermal expansion.
- Must be able to withstand temperature fluctuations.
- Ability to withstand the action of furnace gas, including CO, SO2, CO2, CH4, H2O, and volatile oxides and salts in metals.
- The material should withstand the actions of processing materials reasonably.
- Must withstand impact and abrasion of solid, liquid, and dust-laden gases moving with high speed.
Messi’s high purity, dead burned magnesium oxide MagChem P98 is used in refractory products such as refractory bricks, monolithic gunning mixes, castables, and other miscellaneous refractory applications, for steelmaking, iron making, and foundry applications where high temperature and corrosion resistance are required.
Several grades of dead burned magnesium oxide (periclase) are available in run of kiln and sized fractions.
Refractory Application of Magnesium Oxide
Refractory materials maintain physical and chemical stability at high temperatures. Dead-burned magnesium oxide, which is produced in shaft and rotary kilns at temperatures over 1500oC, has reduced chemical reactivity and therefore is suited to refractory applications.
Magnesium oxide (MgO) has a very high melting point of 2800 degrees C. High melting point, along with resistance to basic slags, wide availability, and moderate cost makes magnesium oxide (MgO) the choice for heat intensive metal, glass, and fired-ceramic applications.
By far the largest consumer of magnesium oxide (MgO) worldwide is the refractory industry. Monolithic gunnables, rammables, castables, spinel formulations, and magnesia carbon based refractory bricks, all formulated using magnesium oxide (MgO), are widely used for basic steel refractory linings. These products are also used in ferroalloy, non-ferrous, glass and ceramic kiln applications.
Magnesium oxide refractory forming mixture and method of producing the same
Refractory Grade Fused Magnesia
The addition of fused magnesia grains can greatly enhance the performance and durability of basic refractories such as magcarbon bricks. This is a function of a higher bulk specific gravity and large periclase crystal size, plus realignment of accessory silicates. Refractory grade fused magnesia has exacting specifications and is normally characterised by the following:
Due to its excellent corrosion resistance, refractory grade fused magnesia is used in high wear areas in steel making, eg, basic oxygen and electric arc furnaces, converters and ladles.
Ultra high purity (>99 per cent MgO) grades have been used in high-tech applications such as optical equipment, nuclear reactors and rocket nozzles.