Magnesium oxide is a very common alkaline oxide and is widely used in the production of magnesium hydroxide and magnesium metal. In the field of advanced ceramics, magnesium oxide is favored due to its extremely high melting point (up to 2800°C) and unique properties. It can be directly sintered into magnesium oxide ceramics or used as an additive. Therefore, magnesium oxide plays an important role in the application of ceramic materials.
Alumina transparent ceramics are widely used in high-pressure sodium lamps in the lighting field, ceramic discharge tubes of ceramic metal halide lamps, integrated circuit substrates in the electronics industry, high-frequency insulation materials, and infrared detection windows due to their high temperature resistance, corrosion resistance, high strength, high toughness and good light transmittance, and low preparation cost. Alumina transparent ceramics are a polycrystalline inorganic material composed of a variety of microstructures, including grains, grain boundaries, second phases, pores, etc. Due to the difference in their respective refractive indices (theoretical transmittance is 86%), the material has low light transmittance.
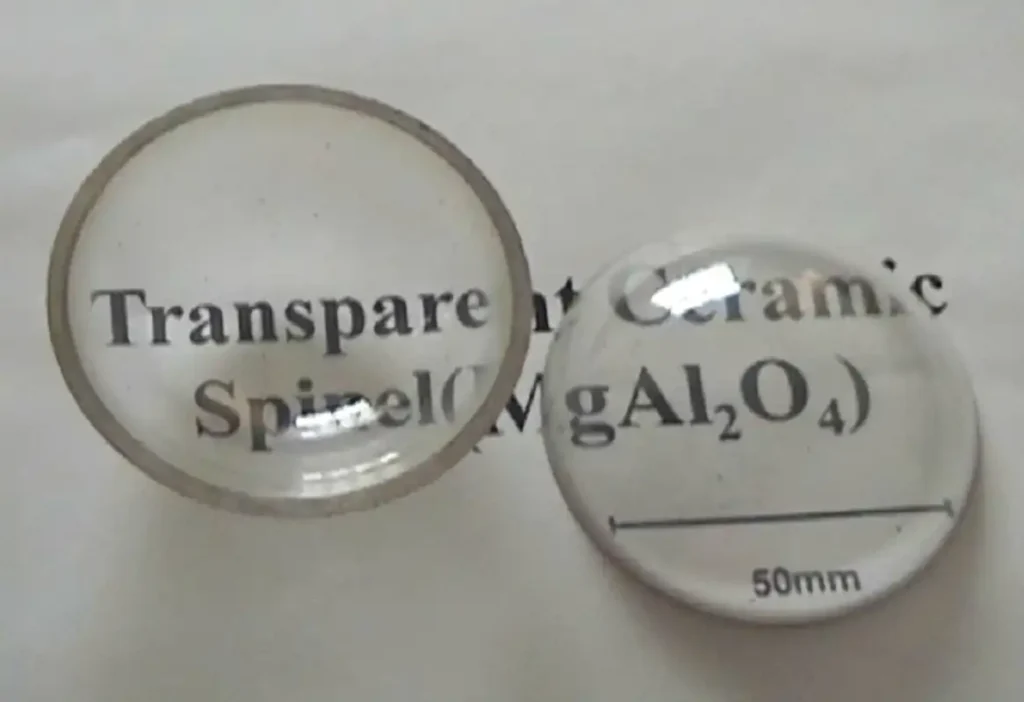
In the preparation process of alumina transparent ceramics, in addition to using high-purity raw material powder, a very small amount of sintering aids must be added to promote sintering densification and the elimination of pores during sintering shrinkage. In addition, trace sintering aids also have the effect of inhibiting abnormal grain growth, so the selection of sintering aids and their content are crucial to the final acquisition of high-quality transparent ceramics. Today we will learn about the effect of MgO as a sintering aid on alumina transparent ceramics.
1. Effect on the sintering temperature of alumina ceramics
Adding an appropriate amount of magnesium oxide can promote the sintering process of alumina ceramics, effectively reduce the sintering temperature of alumina ceramics, and improve its sintering density and wear resistance. Messi Biology Research found that when 10% magnesium oxide is added, the sintering temperature of alumina ceramics can be reduced by 120°C. At the same time, its wear resistance is also greatly improved.
This is because the addition of magnesium oxide can promote the diffusion and bonding between alumina particles. Specifically, the addition of magnesium oxide can lead to the diffusion of grain boundaries and chemical reactions on the surface of particles, thereby forming a layer of magnesium-rich liquid phase grain boundaries between alumina particles, accelerating the bonding and diffusion of particles and reducing the sintering temperature.
2. Influence on the density of alumina ceramics
The density of alumina ceramics is one of the important indicators of its performance, which is related to its mechanical properties, wear resistance and corrosion resistance. Adding an appropriate amount of magnesium oxide can reduce the sintering temperature, inhibit grain growth, reduce the porosity of alumina ceramics, and improve its density.
Studies have shown that the addition of magnesium oxide can change the crystal growth mode and structure of alumina ceramics, promote the uniform distribution and arrangement of its grains, and thus reduce the formation of defects and pores.
3. Summary
In summary, magnesium oxide has a significant effect on the sintering temperature and density of alumina ceramics. However, Messi Biology suggested that in the preparation process of alumina ceramics, reasonable control of the addition amount of magnesium oxide and sintering process is an effective solution to improve the performance of alumina ceramics.