There is still about 20% of cobalt unrecovered in the first cobalt precipitation process. This process uses slaked lime to neutralize and precipitate to recover the cobalt in the first cobalt precipitation liquid. The reaction is as follows:
Ca(OH)2+CoSO4=Co(OH)2↓+CaSO4
At the same time, in an alkaline environment, part of the magnesium sulfate will react with lime to form magnesium hydroxide.
Ca(OH)2+MgSO4=Mg(OH)2↓+CaSO4
The operating conditions are: at 60℃ and under continuous stirring, slaked lime slurry (adjusting slurry concentration ~20%) is continuously added to the second cobalt precipitation reaction tank. To ensure the complete precipitation and recovery of cobalt, the end point pH of the solution should be controlled at about 8.
The second cobalt slag produced by the second cobalt precipitation slurry after filter pressing is mixed with the raffinate and sent to the iron removal process to re-enter the process.
The typical compositions of the second cobalt precipitation liquid and the second cobalt slag are shown in Table 5 and Table 6 respectively.
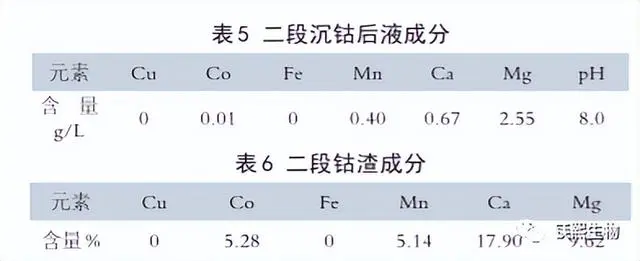
Magnesium precipitation
The liquid after the second stage of cobalt precipitation mainly contains metal ions such as magnesium and manganese. Direct discharge will cause water pollution, so magnesium precipitation treatment is required. This process uses slaked lime to adjust the pH of the solution so that magnesium and manganese ions are precipitated and removed.
The operating conditions are: at 60°C, under continuous stirring, add slaked lime slurry (slurry concentration ~20%) to the magnesium precipitation reaction tank. To ensure complete precipitation of magnesium and manganese ions, the end point pH of the solution should be controlled above 11.
Table 7 shows the main technical indicators obtained in the trial production according to this process in May 2014.
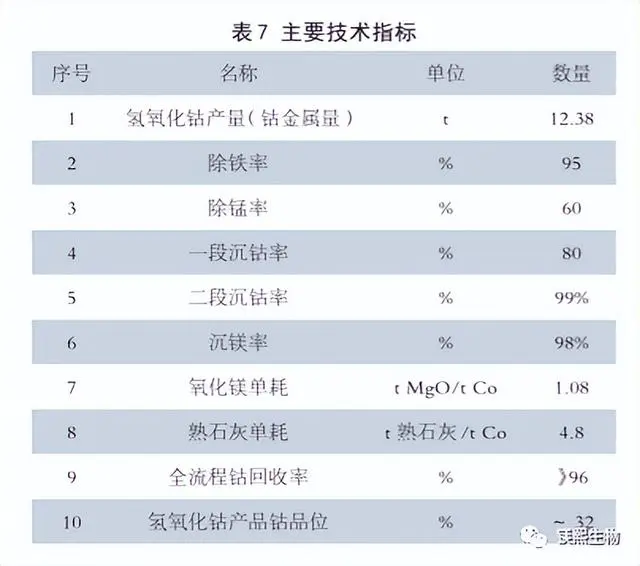