Abstract
The present invention discloses a preparation method of silicon steel grade magnesium oxide coating dedicated to oriented silicon steel sheet, including the following process steps: selecting natural cryptocrystalline magnesite to produce light burnt magnesium oxide powder; digesting the light burnt magnesium oxide, acid and alkali neutralization and decalcification, and reacting it at the temperature of 15-30 ℃ and the time of 5-15 minutes, to generate magnesium hydroxide, and then washing, filtering, drying and calcining at the temperature of 1100± 50 ℃, time for 2.0 ± 0.5 hours for calcination, can be obtained high-purity light burnt magnesium oxide powder; the use of air flow milling processed into the required micron-sized particle size segments. Silicon steel grade magnesium oxide coating produced by this invention has the characteristics of high chemical purity, low impurity ions, good suspension, low hydration rate, coating, good adhesion; its physical properties are far better than similar products, is the production of oriented silicon steel sheet of good annealing isolation agent; and the production process is simple, greatly reducing production costs.
Description
Preparation Method of Silicon Steel Grade Magnesium Oxide Coating
Technical Field
The present invention relates to a method of preparing a magnesium compound, specifically a method of preparing a silicon steel-grade magnesium oxide coating for oriented silicon steel wafers.
BACKGROUND TECHNOLOGY
The silicon steel grade magnesium oxide coating is dedicated to be used as a high temperature annealing isolator in the preparation process of an oriented silicon steel wafer. The main role of silicon steel grade magnesium oxide coating in the high temperature annealing of oriented silicon steel sheet is to prevent the silicon steel sheet steel coil from sintering in the high temperature annealing, and to remove sulfur, phosphorus and other impurities in the silicon steel sheet. According to the survey of China’s high-purity magnesium oxide market demand of nearly 100,000 tons, while the domestic products are very few, the gap is quite large, which gives the production of high-purity magnesium oxide, the development of opportunities and favorable conditions. At present at home and abroad for the preparation of magnesium oxide method of salt brine soda ash method, dolomite, serpentine carbonization method, brine ammonium carbon method. In the patent CN200610012973.2, a method of producing magnesium oxide of silicon steel grade by salt brine soda ash method is disclosed, in which magnesium oxide is produced by reacting refined magnesium chloride solution with refined sodium carbonate solution at the temperature of 65-85°C for 5-15 minutes to generate alkaline magnesium carbonate, and then it is cooked, filtered and calcined at the temperature of 1,100±50°C and time of 2.0±0.5 hours, to obtain magnesium oxide. After calcination, magnesium oxide can be obtained. The above method has problems such as long process flow, low utilization of raw materials, high production cost, pollution of the environment, low magnesium content of the product and low chemical purity.
Content of the invention
In view of this, an object of the present invention is to provide a preparation method of silicon steel grade magnesium oxide coating, to solve the defects of the existing method of preparing silicon steel grade magnesium oxide, such as long process flow, low chemical purity of the final product and poor physical properties.
In order to achieve the above purpose, the present invention provides a preparation method of silicon steel grade magnesium oxide coating, comprising the following process steps:
Step A: Lightly fired magnesium oxide powder is produced by selecting natural cryptocrystalline magnesite;
Step B: digesting the light burnt magnesium oxide, acid and alkali neutralization and decalcification, and reacting at a temperature of 15-30°C for 5-15 minutes to produce magnesium hydroxide, and then calcinating at a temperature of 1100±50°C for 2.0±0.5 hours after washing, filtering, and drying, to obtain high purity light burnt magnesium oxide powder;
Step C: Processing into the desired micron-sized particle size section using air flow milling.
This invention selects natural cryptocrystalline magnesite production of more than 98% of magnesium oxide, calcium oxide 0.8-1.0%; according to the process method to achieve magnesium oxide ≥ 99%, calcium oxide ≤ 0.5% of the low-calcium, chlorine root is less than 0.03% of the high-purity magnesium oxide. Silicon steel grade magnesium oxide coating produced by this invention has the characteristics of high chemical purity, low impurity ions, good suspension, low hydration rate, coating, good adhesion; its physical properties are far better than similar products, is the production of good annealing isolation agent for oriented silicon steel sheet; and the production process is simple, greatly reducing production costs.
Specific implementation
Example 1: choose natural cryptocrystalline magnesite to produce light burnt magnesium oxide powder; light burnt magnesium oxide digestion, acid and alkali neutralization and decalcification, at a temperature of 15 ° C, time for 5 minutes for the reaction, the generation of magnesium hydroxide, and then after washing, filtering, drying at a temperature of 1050 ° C, time of 1.5 hours under the calcinations, you can get high purity light burnt magnesium oxide powder; the use of airflow mill processing into the required micron-level The particle size section is processed into the required micrometer level by using air flow milling.
Example 2: choose natural cryptocrystalline magnesite to produce light burnt magnesium oxide powder; light burnt magnesium oxide digestion, acid and alkali neutralization and decalcification, at a temperature of 20 ℃, time of 10 minutes for the reaction, the generation of magnesium hydroxide, and then after washing, filtration, drying at a temperature of 1,100 ℃, the time of 2.0 hours for the calcinations, can be obtained from the high purity of light burnt magnesium oxide powder; the use of airflow milling processed into the required micron-grade particle size section.
Example three: choose natural cryptocrystalline magnesite to produce light burnt magnesium oxide powder; light burnt magnesium oxide digestion, acid and alkali neutralization and decalcification, at a temperature of 30 ℃, time for 15 minutes for the reaction, the generation of magnesium hydroxide, and then after washing, filtration, drying at a temperature of 1,150 ℃, time of 2.5 hours under the calcinations, can be obtained from the high purity of light burnt magnesium oxide powder; the use of airflow milling processed into the required micron level particle size section.
After practice, the method of the present invention made of silicon steel grade magnesium oxide coating and its technical indicators are shown in Table 1:
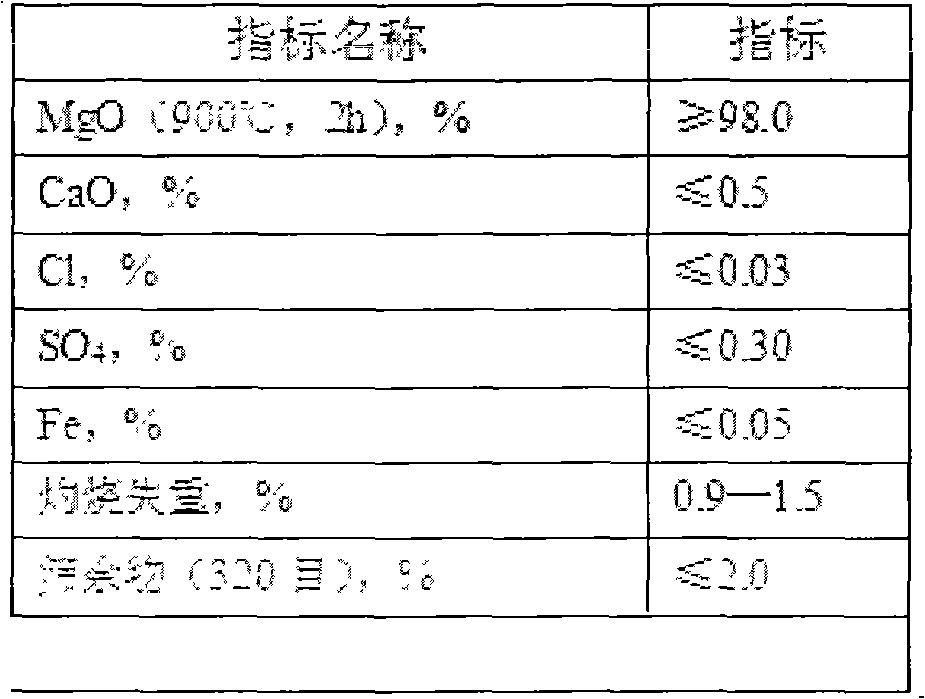