Application requirements of magnesium hydroxide flame retardant materials
As a flame retardant, magnesium hydroxide has the following requirements:
(1) It must have extremely high purity (Mg(OH)2>93%). Magnesium hydroxide with high purity not only has high flame retardant properties, but also can reduce its addition amount in the material.
(2) Small particle size. The composite materials prepared with micro-nano magnesium hydroxide are far superior to micron-grade magnesium hydroxide in all aspects of performance (including flame retardant effect, smoke suppression and mechanical properties, etc.).
(3) Low surface polarity. When the surface polarity of magnesium hydroxide decreases, the degree of agglomeration will decrease, and the dispersibility and compatibility will increase. It can be added to polymers as a flame retardant material to have good compatibility with polymers and reduce the impact on the mechanical properties of the material.
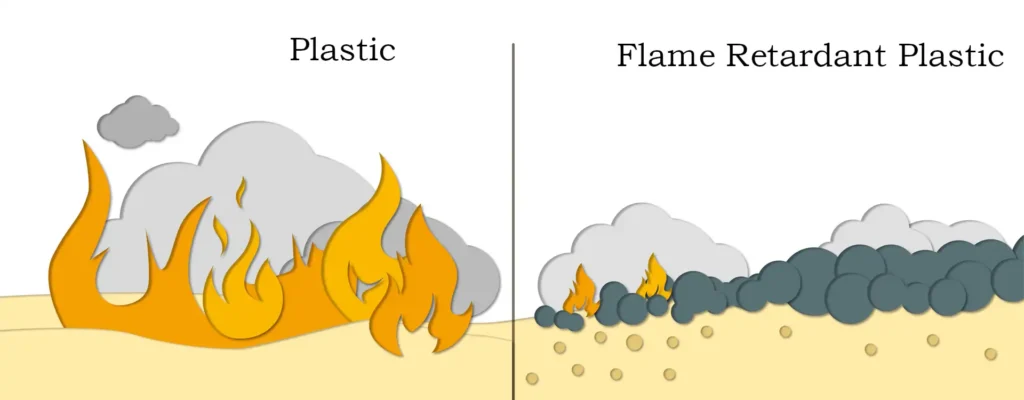
Reasons for modification of magnesium hydroxide flame retardant materials
At present, most of the magnesium hydroxide flame retardants produced on the market are micron-grade (d>5μm), with a wide particle size distribution, and require a large amount of filling in the application; in addition, the prepared magnesium hydroxide products are easy to agglomerate, have strong hydrophobicity, and are incompatible with high molecular polymers. In practical applications, magnesium hydroxide has caused serious damage to the mechanical properties of polymer materials, greatly limiting the application of magnesium hydroxide flame retardants.
Obtaining magnesium hydroxide flame retardants with low surface polarity, strong hydrophilicity, small particle size and narrow distribution, and good compatibility with polymers through certain physical and chemical methods has become a hot topic for current scientific and technological workers.
On the one hand, the surface modification of magnesium hydroxide using organic functional groups can reduce the polarity of the surface of magnesium hydroxide and improve its compatibility with polymers; the micro-nano-level ultrafine magnesium hydroxide has a low filling amount, and the composite material prepared using it has good performance.
On the other hand, the flame retardant performance of micro-nano-level magnesium hydroxide of the same quality is several times higher than that of micron-level magnesium hydroxide, and the impact on the performance of polymer polymer materials is also low. Low-polarity micro-nano-level magnesium hydroxide can be evenly dispersed in polymer materials, so that the flame retardant and mechanical properties of the entire material remain consistent. Therefore, surface modification and ultrafineness of magnesium hydroxide flame retardants can solve the shortcomings in the application of magnesium hydroxide flame retardants.
Study on surface modification of magnesium hydroxide
As a flame retardant for polymers, the most important thing for magnesium hydroxide is to be well compatible with polymers, achieve uniform dispersion, and ultimately achieve the purpose of flame retardancy. Using specific compounds to modify the surface of magnesium hydroxide can reduce the surface polarity of magnesium hydroxide, make its surface hydrophobic, and improve the compatibility of magnesium hydroxide with polymers.
The chemical modification of the surface of magnesium hydroxide is to selectively adsorb or specifically adsorb or chemically react the functional groups in organic molecules or inorganic gel molecules on the surface of magnesium hydroxide powder by chemical methods, thereby coating the surface of the particles, making the surface of the particles organic or changing the polarity, and finally achieving surface modification. Commonly used surface modifiers mainly include silane coupling agents, titanates, aluminates coupling agents, and higher fatty acids and their derivatives.
Physical modification of magnesium hydroxide usually includes surface high-energy modification and surface coating modification. Surface high-energy modification mainly modifies Mg(OH)2 by radiation and other methods to change the surface activity of Mg(OH)2. The modification process does not involve chemical reactions. Surface coating modification is mainly to modify Mg(OH)2 through dispersants.
Research on ultrafine magnesium hydroxide
Ultrafine is one of the effective methods to enhance the compatibility of magnesium hydroxide with polymers and reduce the filling amount. The preparation process has a decisive influence on the physical and chemical properties of the final morphology of magnesium hydroxide, such as particle size, particle size distribution, morphology, etc. Changing the preparation process is the most effective way to obtain ultrafine magnesium hydroxide.
Solvothermal and hydrothermal methods, microwave-assisted methods and ultrasonic chemical methods have been widely verified in the preparation of micro-nano materials, and some research reports have also been made on the preparation of ultrafine magnesium hydroxide flame retardant materials.
Summary
In the past two decades, great progress has been made in the research on magnesium hydroxide modification and ultrafine preparation. The non-toxicity, wide source and low price of magnesium hydroxide are the biggest advantages of this material as a flame retardant. With the strengthening of environmental protection efforts, the application of magnesium hydroxide in flame retardant materials will continue to increase in the future. The surface modification and ultrafine preparation of magnesium hydroxide flame retardants are of great significance to their application in the flame retardant material industry.
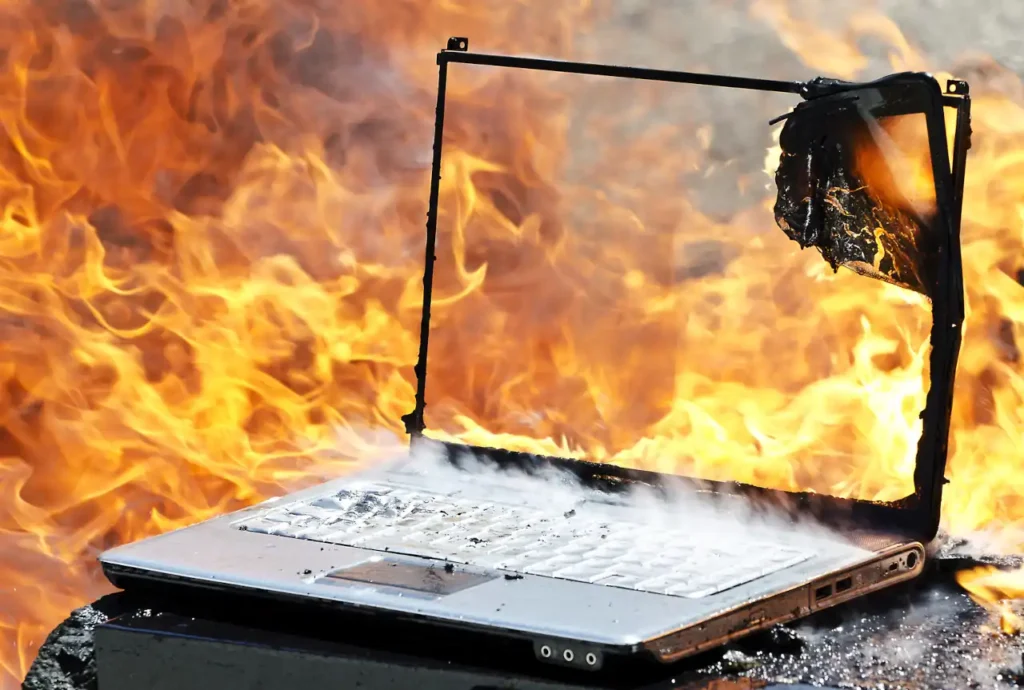