Abstract
The present invention provides a method for preparing ultra-high specific surface area magnesium oxide. Magnesium oxalate is prepared by reacting magnesium acetate solution and oxalic acid solution, and this magnesium oxalate can be roasted at high temperature to obtain magnesium oxide with ultra-high specific surface area of more than 400 m2-g-1. This method is characterized by cheap raw materials, simple operation and good performance of the obtained product.
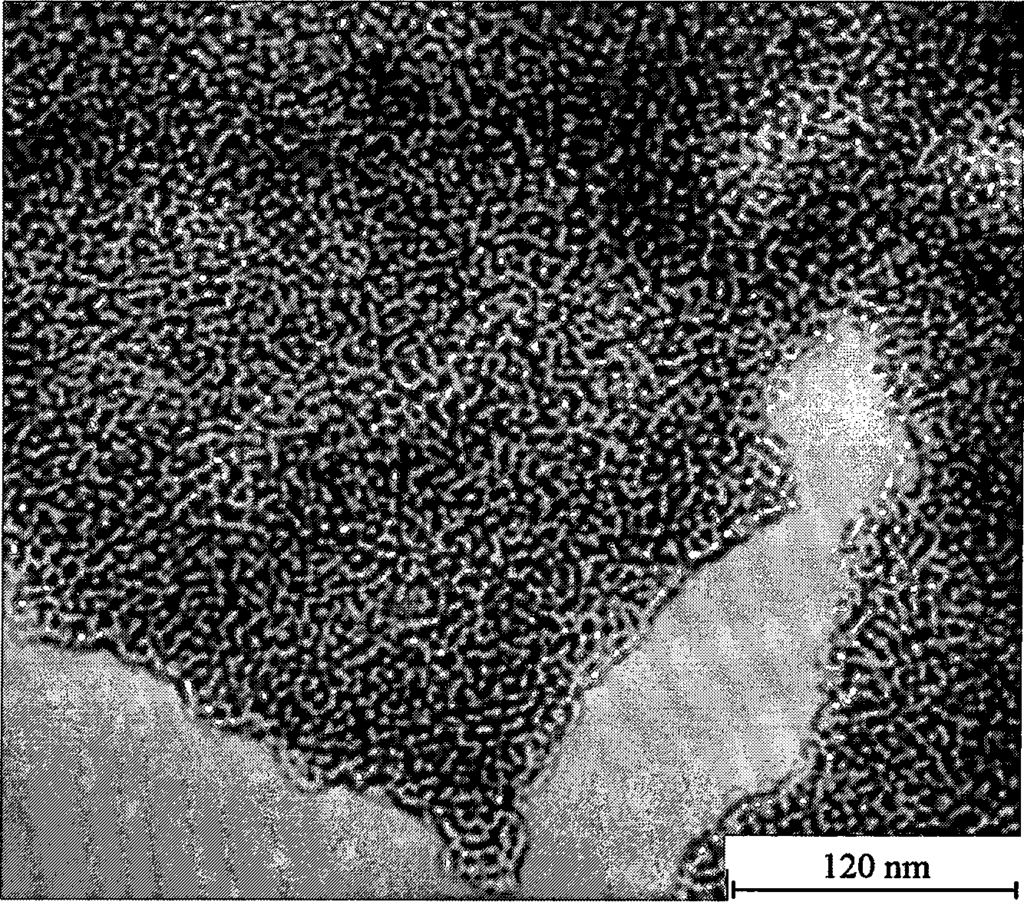
Description
Preparation method of magnesium oxide with high specific surface area
Technical Field
The present invention relates to a simple method for preparing magnesium oxide with high specific surface area, which belongs to the field of preparing inorganic non-metallic materials.
Background Technology
Magnesium oxide is a metal oxide with the highest melting point, and has a wide range of applications in the fields of refractories, ceramics, textiles, coatings, superconducting materials, catalysts, catalyst carriers and adsorbents. Increasing the specific surface of magnesium oxide can improve the properties of the catalysts and adsorbents concerned.
The specific surface area of general commercial magnesium oxide is only about 40m2-g-1. There are two commonly used methods to prepare magnesium oxide with high specific surface area (SBET>100m2-g-1): one is to obtain Mg(OH)2 by precipitation method, and then by alcohol replacement and other treatments, and then roasted at 350-400°C, magnesium oxide with specific surface area of 100-300m2-g-1 can be obtained, but the specific surface of magnesium oxide obtained by this method is not high, and its thermal stability is not good; the other is the gas-gel method, which can obtain the specific surface of magnesium oxide with a specific surface area of 100-300m2-g-1. gel method, which can obtain magnesium oxide with a specific surface area of 300-500 m2-g-1. For example, Mel’gunov et al. (Journal of Physical Chemistry, 2003, 107: 2427-2434) used Mg(OCH3)2 as a raw material, and after hydrolysis, supercritical drying and 500 °C magnesium oxide with a specific surface area of 412 m2-g-1 was obtained by vacuum roasting of Mg(OCH3)2. This method is expensive in raw materials and complicated in preparation, which makes it difficult to be applied industrially.
In addition, it has been reported in the literature that the thermal decomposition of magnesium oxalate can be utilized to obtain magnesium oxide with a higher specific surface area.Dollimore et al. (Proceedings of the Technical Program: International Powder and Bulk Solids Handing and Processing 1981), 143-6. 143-6) and Razouk et al. (J. Appl. Chem. Biotechnol. 1973, 23: 51) have prepared magnesium oxide by roasting magnesium oxalate in a flowing atmosphere and in vacuum, respectively, and they obtained magnesium oxide with a specific surface area of 200-300 m2-g-1 at 500 °C.
In the existing literature and patents on the thermal decomposition of magnesium oxalate for the production of magnesium oxide, research workers have tried to obtain magnesium oxide with a high specific surface by reducing the grain size of the precursor magnesium oxalate (e.g., by adding dispersants during the synthesis process, etc.), but the maximum specific surface of magnesium oxide was not up to 300 m2-g-1 (roasted at 500 °C) (Journal of Inorganic Chemistry, 2005, 21(2): 221).
Contents of the invention
The purpose of the present invention is to solve the problems of high cost in the preparation of high specific surface magnesium oxide and the difficulty in obtaining high specific surface by roasting at high temperature, and to provide a preparation method with low cost and high specific surface of the resulting product magnesium oxide.
The technical program of the present invention is as follows:
Magnesium oxalate is prepared by reacting magnesium acetate and oxalic acid, and this magnesium oxalate is aged, filtered and dried, and then roasted at a high temperature of 450-800°C in a flowing atmosphere or in a vacuum to obtain magnesium oxide with a high specific surface.
The present invention utilizes magnesium acetate and oxalic acid as raw materials, is prepared under acidic conditions of magnesium oxalate, preferably under constant stirring, the magnesium acetate solution will be added dropwise to the oxalic acid solution according to the equivalence ratio, and this solution is aged at room temperature for a period of time and then filtered, and the precipitate obtained is then dried, and the one thus produced is usually MgC2O4-2H2O.
The flowing atmosphere during the above roasting can be flowing air or nitrogen, preferably dry air or dry nitrogen, and the optimal temperature for high-temperature roasting is 520 °C.
The thermal decomposition of magnesium oxalate yields magnesium oxide, while a large amount of CO and CO2 gas is produced. This is a strong heat-absorbing reaction with a thermal decomposition temperature range of 400-500°C. Before complete decomposition, the local temperature of magnesium oxalate does not exceed the decomposition temperature, thus inhibiting intergranular sintering of the newly generated magnesium oxide grains, resulting in magnesium oxide with a high specific surface.
Compared with the magnesium oxalate prepared in neutral or alkaline solution (with ammonium oxalate or sodium oxalate as precipitant) reported in the existing literature, the magnesium oxalate prepared in acidic solution with oxalic acid as precipitant of the present invention has a larger grain size, and it is found in the present invention that precursor magnesium oxalate with a larger grain size can be roasted under the same conditions to obtain magnesium oxide with a higher specific surface, because the decomposition of magnesium oxalate is a strong heat-absorption reaction, due to the heat conduction factor and the heat transfer factor, the precursor magnesium oxalate with large grains can be burned under the same conditions to obtain magnesium oxide with a higher specific surface. Because the decomposition of magnesium oxalate is a strong heat-absorbing reaction, due to the influence of heat conduction factors and the thermal decomposition of magnesium oxalate, the magnesium oxalate with a larger grain size is more conducive to maintaining a lower local temperature when decomposing and generating magnesium oxide, which can reduce the sintering of the newly generated magnesium oxide between the grains to a greater extent, and even if the magnesium oxide is not easy to grow up with the sintering, so as to make the product of the specific surface of the magnesium oxide be improved by a factor of one.
It is on the basis of the above findings that the present invention for the first time makes magnesium oxalate by the reaction of magnesium acetate solution and oxalic acid solution, and the grain size of the resulting magnesium oxalate is larger than that of all the magnesium oxalates in the literature that have been prepared using other raw materials. This magnesium oxalate can be roasted in flowing dry nitrogen or air to obtain ultra-high specific surface of magnesium oxide. The optimal conditions of the sample prepared by roasting at 520 ℃ for 1h after the specific surface as high as 534m2-g-1, magnesium oxide grain size of only 4-5nm, far better than the best results reported in the literature. The magnesium oxide so produced has very good resistance to high-temperature sintering, and its specific surface is still as high as 229m2-g-1 and 134m2-g-1 after roasting at 650°C and 800°C for 2h, respectively, which is also much higher than the literature value. The method is cheap in raw materials, simple in operation, and the resulting product has good performance, which is much better compared with the aerogel method, which is currently recognized as the most effective method in the literature for the preparation of high specific surface magnesium oxide.