Our country is the richest country in magnesite resources, not only the total amount is large, but also a variety of categories. Since 1950, our country has gradually begun the development and utilization of magnesite resources, but due to the low level of technology at that time, the development and utilization of magnesite resources has not been well developed. To the 1970s and 80s of the 20th century, our country’s magnesite resources development and utilization and have a progressive breakthrough. Because in this period, China’s iron and steel industry is entering a brand new stage, the demand for refractory materials is relatively large, so the consumption of magnesite also increased. By about 1990, China established the magnesite industry association, making has been a messy industry has been effectively managed, our magnesite industry gradually to the right track. Not only has there been a great improvement in the industrial level, but also the quality of the products has been upgraded, and at the same time new production processes and technologies have been developed, which can be said to have fundamentally promoted the development and comprehensive utilization of this industry. The following are the main products of China’s magnesium refractory raw materials, the current situation of production and existing problems.
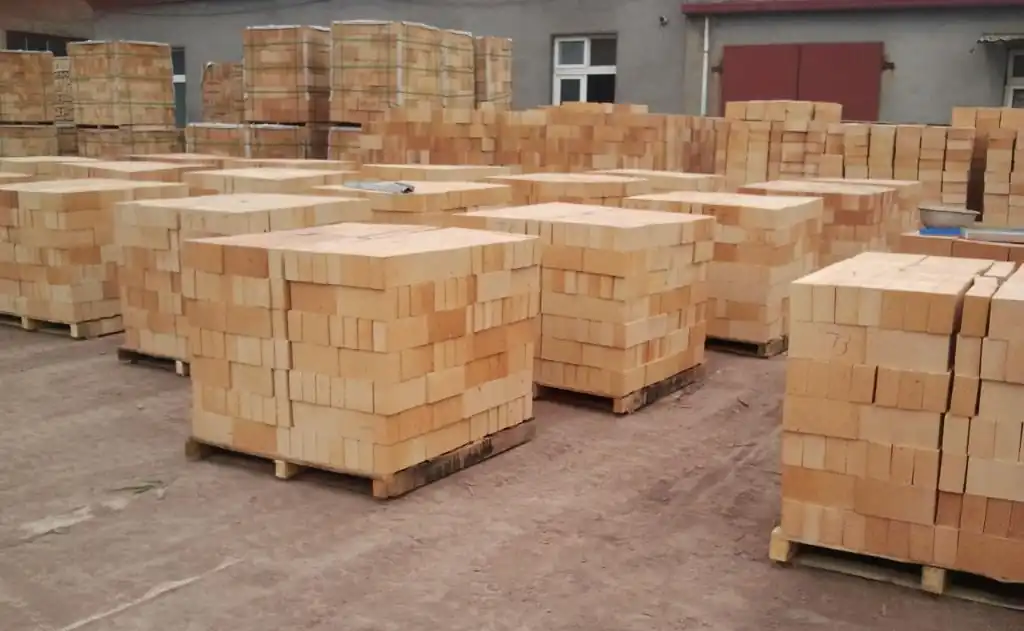
1, light burned magnesium oxide
At present, China to magnesite as raw material, through the reflection furnace light burning processing for light burned magnesium oxide powder (CCM). Lightly burnt magnesium oxide is a very important basic raw material of magnesium because of its large quantity and wide use. According to its different chemical composition, particle size and performance, they are applied to: calcined into various grades of sintered magnesia (DBM) by ball pressing, synthesize magnesium-aluminum spinel sand, magnesium-calcium sand and other composite materials with raw materials containing Al2O3, CaO, etc., produce electrofused magnesia (FM, refractory grade or electrician grade), and produce magnesium balls of converter sputtering slag furnace protection. The above products are mainly used as raw materials for refractory products. In addition, it is also the raw material of magnesium chemical products such as light Mgo, light MsCO, magnesium fertilizer, magnesium building materials, feed additives and so on.
Traditionally, light-burned magnesium oxide is roasted with magnesite in a reflecting furnace. The use of reflecting furnace production of light burned magnesium oxide after seventy or eighty years of survival and development has not been eliminated, because the furnace has its outstanding characteristics: 1) process is simple, practical; 2) investment is small, on the horse quickly, easy to operate; 3) suitable for Liaonan region magnesite characteristics.
In recent decades, the production process of the reflecting furnace has also been greatly improved, mainly in:
(1) switch to clean fuel, the original direct burning of bituminous coal to simple gas generator production of gas as fuel for roasting, to avoid fuel ash on light burning magnesium oxide pollution; basic solution to the black smoke emissions on the environment pollution, and improve the thermal efficiency.
(2) The kiln type is remodeled to increase the volume of the kiln, which improves the output and reduces the fuel unit consumption. Early reflector furnace only 7.8 m3, yield 10 t-d-1; later expanded to 18 m3, yield 20 t-d-1. After continuous improvement of the kiln type and castor plate material, the current reflector furnace single furnace output up to about 30 t-d-1, the fuel consumption accordingly continue to decline.
However, China to magnesite by reflex furnace roasting production of light burned magnesium oxide powder at present there are still the following problems: (1) mining activities are simple, artificial sub-mining; (2) manual operation, kiln temperature stability is poor, high energy consumption; (3) the kiln with lump ore, crushed ore discarded, material consumption is high; (4) the flue gas is not processed, polluting the environment; (5) cooling open, poor labor conditions, resulting in the current difficult to recruit workers; (6) grinding equipment Simple, particle size control is poor, the final product quality is low and fluctuates greatly.
Therefore, China’s light burnt magnesium oxide production must be implemented mining a finished product of a package of the whole process control, according to the user requirements of production, and research and promotion of advanced light burnt magnesium oxide roasting technology and kiln. Recommended for large-scale suspension kiln, multi-storey furnace (consumption furnace MHK) for light burned and high efficiency light burned magnesium oxide.
2、Sintered magnesia
The national standard GB/T 2273—2007 stipulates the physical and chemical properties of various sintered magnesias with Mgo mass fraction of 83% to 98% applicable to the production of refractory materials. From the historical perspective, sintered magnesia is known as metallurgical sand, re-fired magnesia, medium-grade magnesia, high-purity magnesia.
2.1 Metallurgical sand
During the period of China’s first five-year plan (1952-1957), China’s first production of alkaline refractory materials factory built with the aid of the former Soviet Union – Anshan Iron and Steel Company Dashiqiao Magnesium Brick Factory Phase I project went into operation, the sand-making workshop used a semi-dry process of fine grinding of ore, ball-forming pan, grate machine, rotary kiln, the production of metallurgical sand used for Flat furnace sintering bottom and repair. With the change of steelmaking flat furnace to converter, the product was eliminated in the 1990s.
2.2 Re-fired magnesia
At present, China’s total output of sintered magnesia is 4 million to 4.5 million tons per year. Following the industry’s custom, sintered magnesia is roughly divided into re-fired magnesia, medium-grade magnesia and high-purity magnesia.
Before 1980s, in the long period of more than 30 years, the production of sintered magnesia is mainly undertaken by the former Anshan Iron & Steel Dashiqiao Magnesia Mine, which successively adopts 25, 32, 40, 47 and 55 m3 vertical kilns, using coke as fuel and massive magnesite as raw material, and adopts one-step calcination and artificial discharging to produce re-sintered magnesia with w(MgO)≈92%, which is a raw material for the bricks of the flat furnaces of the country’s steelmaking. The defects of the process are:
(1) Low ore utilization. Fine-grained ore can not be utilized.
(2) High impurity content. The ash in the coke will pollute the magnesia and increase the SiO2 and Al2O3 content of the magnesia, and the highest Mgo content (w) can only be guaranteed at 92%.
(3) Poor degree of continuous operation. Large magnesite ore thermal decomposition of small particles of ore adhering to the kiln wall, resulting in “sticky kiln”, the kiln material is prone to “lump”, which causes frequent changes in the kiln material flow and thermal regime, resulting in shutdown accidents, can not achieve mechanized operation.
(4) low density of magnesia. Magnesite in the kiln pre-tropical decomposition, the release of CO2 into light burning MgO, but its MgCO3 mother salt artifacts still exist, not conducive to the further densification of magnesia, resulting in sintered magnesia bulk density of only 3.0 ~ 3.1 g-cm-3.
(5) Serious environmental pollution. Magnesite decomposition of a large number of CO2 and burning smoke mixed with fine coke particles and light burning dust flying out of the kiln, polluting the environment, and high-temperature flue gas treatment difficulties.
At present, China’s re-fired magnesia is still used in the second and third grade ore calcined in the solid fuel vertical kiln production. Re-fired magnesia w (MgO) = 90% ~ 92%, bulk density of about 3.10 g – cm – 3. Re-fired magnesia is the production of ordinary magnesium sintered bricks and the main raw material of non-conformable refractories, Liaoning Province, the current annual output is estimated to be 2.5 million t. Due to the use of tertiary ore, the product price is low and there is a market for the product, it is difficult to phase out at present.
2.3 Medium grade magnesia
In order to improve the density and purity of magnesia, China refractories community carried out two-step calcined magnesia process research and industrial tests. The use of new technology, new processes suitable for national conditions, promote the technical progress of sintered magnesia production. in the early 1980s, Haicheng magnesium mines using high-quality magnesite by the reflecting furnace light burning, Raymond mill grinding, semi-dry two-stage balling, coke vertical kiln calcination, the production of w (MgO) ≥ 95%, bulk density of ≥ 3.20 g-cm-3 of the mid-range magnesia. The result was quickly popularized, forming a scale with an annual output of several hundred thousand tons. Since then the process has also been popularized for the production of synthetic sand products such as synthetic magnesium-calcium sand.
At present, the mid-range magnesia can be divided into 94, 95 two grades, bulk density of 3.20~3.25 g-cm-3. Mid-range magnesia is an important variety of magnesia, mainly used in the production of mid-range magnesium bricks, direct bonded magnesium bricks, magnesium spinel bricks, and some magnesium unshaped refractory materials.
2.4 High-purity magnesia
In 1980, the former Ministry of Metallurgy Mines Division organized the implementation of “natural magnesite to obtain high-quality high-purity magnesia new technology and high-temperature vertical kiln” project, in Haicheng magnesium mine to build an annual output of 0.7 million t of high-purity magnesia pilot production line, for the large crystallization of magnesite difficult to sintering characteristics, the development of the magnesite light burning, grinding, high-pressure ballasted and dead burned “two-step calcination “new process, after several years of research, made w (MgO) ≥ 98%, bulk density of 3.30 g-cm-3 high-purity magnesia, to achieve the goal of research. Based on the use of powder ore, flotation process, and from Europe to introduce an annual output of 50,000t of high-purity magnesia production line of key equipment (suspension roaster, roller mill, high-pressure ballast, high temperature oil vertical kiln, etc.), independent research combined with the introduction of the end of China’s history of no high-purity magnesia.
From 2006 to 2010, Dashiqiao Jinding Company (former Anshan Iron & Steel Dashiqiao Magnesium Mine) and Magnesium Company (RHI) cooperated to build the project of high purity magnesia with annual output of 100,000t, among which the annual output of sintered sand and electrofused sand is 50,000t each. magnesite flotation process is adopted to improve the purity of magnesite outside the magnesite grade, and multi-storey furnace (MHK) is used for light burning. Its sintered magnesia production line of light burning magnesium oxide with ball milling a selection of powder machine powder, the high-pressure ballast machine ball, liquefied petroleum gas-fueled high-temperature vertical kiln calcined to produce w (MgO) = 98%, bulk density of 3.40 g-cm-3, m (CaO) / m (SiO2) > 2 high-quality sintered magnesia, reached the international advanced level.
Based on China’s national conditions, now the production process of high purity magnesia is mostly as follows: selecting high quality magnesite, light burning in the reflection kiln fueled by gas, fine grinding of the light burning powder with raymond machine, dry balling with high pressure press, and finally calcining in high temperature oil vertical kiln, and ultimately producing high purity magnesia with roost (MgO)=97% and bulk density of 3.25~3.30 g-cm-3. The equipment of this process is completely localized, and the products meet the requirements of magnesia needed for most of the high-grade magnesium refractories in China, and a certain amount of exports.
High-purity magnesia has 97, 98 two grades, at present in the Chinese market in fact there is no stable supply of products, in Liaoning only a few enterprises can produce and supply plus (MgO) ≥ 97.5%, m (CaO) / m (SiO2) ≥ 2, bulk density ≥ 3.30 g-cm-3 superior high-purity magnesia, such as after the Ying Group and Xiuyan Wancheng Group, and the demand exceeds supply. At present, the annual output of mid-grade magnesia and high-purity magnesia in Liaoning Province is about 2 million tons.
3、Electrofused magnesia
The development of electrofusion magnesia is accompanied by the development of MgO-C brick production technology and rapid development. High quality MgO-C bricks require magnesia not only to have high purity and density, but also to have a larger grain size, so this magnesia is usually obtained by electrofusion process. Electrofusion magnesia to magnesite (preparation of ordinary electrofusion magnesia) or lightly burnt Mgo (preparation of large crystallization electrofusion magnesia) as raw materials in the electric melting furnace after melting and slow cooling and produced. However, due to the production of electrofused magnesia to consume a lot of electricity, belongs to the national energy policy to limit the development of the industry, its development will be categorized by the implementation of the impact of the tariff policy.
3.1 Technology development of electrofused magnesia
Electromelting magnesia production enterprise technology development focuses on energy saving, improve the comprehensive utilization of magnesite resources and soot control. The main technical measures are:
(1) to carry out the preparation of electrofusion magnesia comprehensive energy-saving technology research. 20 century before the 1990s, our country’s electrofusion magnesia furnace capacity is mostly 300 ~ 600 kVA. in order to produce grain larger electrofusion magnesia and save electricity, and constantly improve the power of the electric furnace, most of the electrofusion furnace capacity is now more than 1,400 kVA, the joint venture up to 3,500 kVA, the national 863 technology research and development of the Large electric furnace to reach 5,000 kVA; the implementation of energy-saving power supply to the furnace of electric magnesia, energy-saving intelligent control and the development of new energy-saving electric magnesium furnace.
(2) Smoke and dust management, waste heat recovery. Liaoning province is taking corresponding governance measures, summarize the experience to solve the production of electric melting furnace fume pollution and magnesia melting cooling waste heat recovery.
3.2 Resource problems of electrofusion magnesia production
At present, Liaonan electric fusion magnesia products are mainly divided into: ordinary electric fusion magnesia, two calcium sand, large crystallization sand three categories. Liaoning Province, the current annual output of electrofused magnesia nearly 1.7 million t. Liaonan electrofused magnesia is currently w (MgO) > 47% of magnesite as raw material, due to the current decline in magnesite grade, 98 (MgO mass fraction) grade electrofused magnesia is only 97.2%. Therefore, the use of flotation process to concentrate powder and light burning magnesium oxide ballast with ore into the furnace electrofusion, not only can greatly reduce the unit power consumption of electrofusion magnesia, and high-grade electrofusion magnesia harvest rate is also increased accordingly.