The application of active magnesium oxide in nickel and cobalt hydrometallurgy not only improves the extraction efficiency of the metal, but also brings economic benefits to the related enterprises. In this paper, the role mechanism of active magnesium oxide and its performance in actual production are discussed in depth.
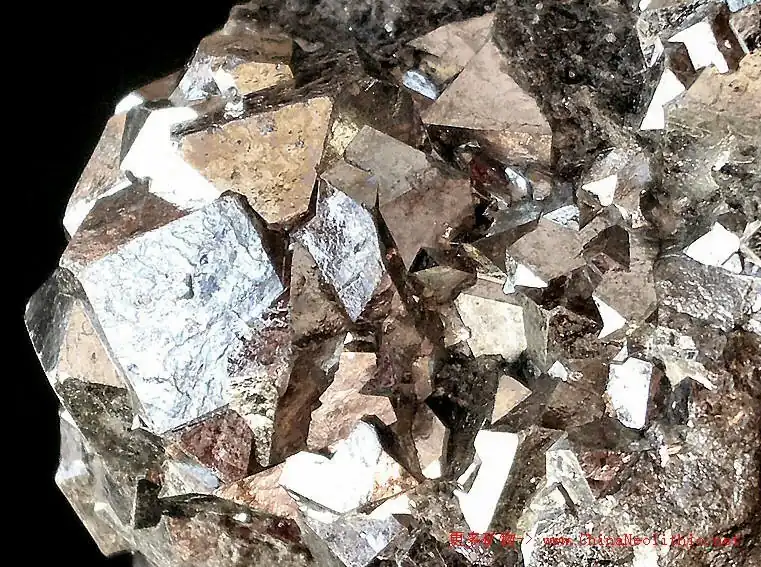
Magnesium oxide (MgO) precipitation of nickel and cobalt in hydrometallurgy is a common technique, especially in the treatment of nickel and cobalt-bearing sulfide ores or intermediates. This method usually involves the following steps:
1, Leaching:
First, the nickel and cobalt containing ores or intermediates are dissolved by acid or alkaline leaching to form a solution containing nickel, cobalt and other metal ions.
2, PH adjustment:
In the solution of nickel and cobalt ions add active magnesium oxide, magnesium oxide will react with water to form magnesium hydroxide (Mg(OH)2), which will increase the pH of the solution. The optimum precipitation pH range of different metals is different. By precisely controlling the pH value, nickel and cobalt ions can be selectively precipitated from the solution, while other metals remain dissolved.
3, Precipitation:
Under appropriate pH conditions, nickel and cobalt ions will react with hydroxide ions (OH-) in the solution to form insoluble nickel hydroxide (Ni(OH)2) and cobalt hydroxide (Co(OH)2) precipitation.
4, Solid-liquid separation:
Separate the precipitated nickel hydroxide and cobalt hydroxide from the solution by physical methods such as filtration or centrifugation.
5, Washing and drying:
The precipitate is washed to remove the attached impurities, and then dried to get the pure nickel hydroxide and cobalt hydroxide products.
6, Further processing:
The nickel hydroxide and cobalt hydroxide can be further processed, such as calcined into oxides, or through other metallurgical processes into nickel metal and cobalt metal.
Activated magnesium oxide has become an indispensable part of nickel and cobalt hydrometallurgy, which brings significant economic benefits to enterprises by improving metal recovery and reducing energy consumption. With the continuous progress of technology, the application prospect of active magnesium oxide in nickel and cobalt industry will be more broad. It should be noted that the quality of magnesium oxide (such as purity, particle size and specific surface area) will directly affect its performance in the precipitation process. Therefore, the selection of high quality magnesium oxide is crucial for the hydrometallurgical process. Messi Biology specializes in the production of high reactive magnesium oxide products suitable for hydrometallurgy to meet the needs of the industry.
Experimental data and examples of industrial applications:
In industrial tests in the DRC, the grade and recovery of a cobalt hydroxide product could be optimized by controlling the amount of magnesium oxide used. The experiments showed that when the amount of magnesium oxide used was 1.0 times the amount of cobalt metal in solution, the cobalt grade reached up to 36.4%, the recovery was about 81.5%, and the impurity content in the product could be further reduced by increasing the washing process.