Active magnesium oxide is one of the many varieties of magnesium oxide products, activity refers to the ease of reaction of magnesium oxide, by the magnesium oxide solid particles of the degree of coarseness and fineness (specific surface area decision).
Some of the indexes of active magnesium oxide are different from common magnesium oxide requirements; for example, there should be suitable particle size distribution, average particle size: <2 µm (2000nm); micro-morphology is irregular particles or nearly spherical particles or flaky crystals; activity indicated by citric acid (CAA value) is 12-25s (the smaller the value, the higher the activity); activity indicated by the iodine-absorbing value is 80-120 (mgI2/100gMgO); specific surface area of the solid particles is determined by the degree of coarseness of the solid particles (specific surface area) of magnesium oxide. 100gMgO); specific surface between 5~20m3/g, apparent specific volume between 6~8.5mL/g.
Active magnesium oxide is one of the important raw materials of CR adhesive, the activity of magnesium oxide reflects the strength of magnesium oxide and CR adhesive reaction ability. The higher the activity, the faster the reaction speed with CR adhesive. The role of active magnesium oxide in CR adhesive is multi-faceted, the main vulcanization crosslinking, acid absorption, anti-scorch, and resin chelating and other roles.
Activated magnesium oxide due to its large surface area, high activity, used in CR adhesive, can improve the initial adhesion of the adhesive, adhesive strength. Improve the transparency of adhesive. The biggest feature can prevent the delamination and precipitation of the adhesive. The activity of active magnesium oxide is generally expressed by the size of the iodine absorption value, the iodine absorption value is less than 400mg/g for low activity, the iodine absorption value is 40-100mg/g for medium activity, and more than 100mg/g for high activity. High-quality CR adhesives generally use high-activity magnesium oxide.
CR adhesive is an important variety of rubber adhesive with large production and wide usage, with initial adhesion, high bonding strength, flexible layer, good elasticity, impact resistance, oil resistance, alkali resistance, acid resistance and solvent resistance, ozone resistance, aging resistance, durability, and flame retardant, can be bonded to a variety of metal, non-metallic materials. It can be used to bond rubber, leather, fabric, artificial leather, wood, concrete and asbestos, etc. It is especially suitable for the bonding of these materials with different materials such as metal and plastic. It includes solvent-based, emulsion-based and non-solvent-based three varieties, of which solvent-based CR adhesive is the most widely used. Solvent-based CR adhesive is also divided into hot vulcanization type and cold bonding type. Currently use more CR adhesive is solvent-based cold adhesive adhesive.
1. Activated magnesium oxide in CR adhesive vulcanization mechanism.
1.1 hot vulcanization type CR adhesive
General solvent-based CR adhesive consists of CR, metal oxides, resins, antioxidants, fillers, crosslinking agents, accelerators, solvents and other components. Formulation is different, the composition is not the same. Metal oxides in CR adhesive can obtain processing safety and vulcanization speed balanced vulcanization system. Zinc oxide and active magnesium oxide in metal oxides are commonly used vulcanizing agents in CR, and their mechanism of action is more complex. In the CR vulcanization crosslinking process, zinc oxide and active magnesium oxide synergistically react to CR. Especially the activity size of active magnesium oxide has a great influence on the safety of CR processing and the performance of vulcanized rubber. Considering the comprehensive factors, CR vulcanization system should be selected appropriate activity of magnesium oxide. At present, the CR vulcanization mechanism has many different opinions, of which the more recognized one is as follows:
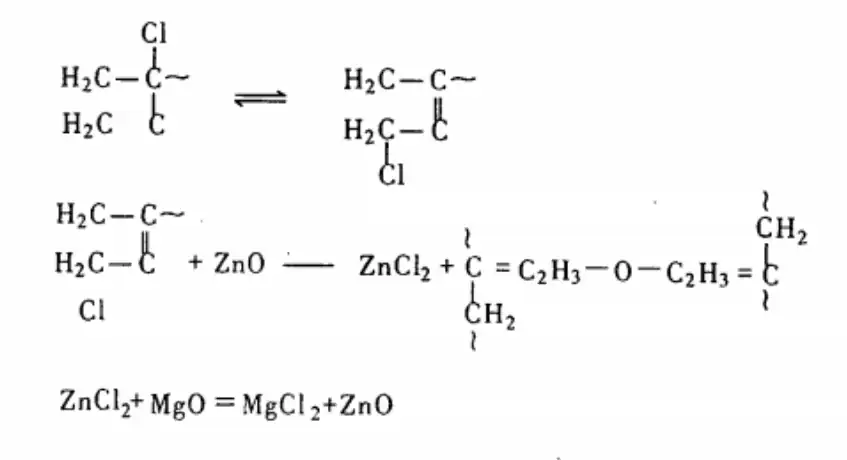
The vulcanized rubber has good thermal stability due to the generation of C-O-C (ether) cross-linking bonds with high bonding energy. If zinc oxide is used alone, it is not only prone to scorching, but also the mechanical properties of vulcanized rubber are poor. After adding active magnesium oxide, it avoids the generation of a large amount of zinc chloride and prevents the vulcanized rubber from having a tendency to scorch. In addition, the newly generated zinc oxide is reused in the vulcanization reaction process, thus increasing the degree of crosslinking. Another main role of active magnesium oxide is acid absorption, which can prevent early vulcanization of the rubber material and prevent the adhesive from producing gel during processing and storage. Active magnesium oxide can also effectively absorb the residual solvent of the adhesive film, accelerate the drying speed of the adhesive, improve the initial bonding strength.
1.2 Cold-type CR adhesive
Cold adhesive room temperature curing does not produce vulcanization crosslinking reaction. The adhesive force of the adhesive is accomplished by the CR crystallinity and the adhesive force of the resin. Zinc oxide in the cold adhesive CR adhesive as an acid-absorbing agent does not work crosslinking, thus making the glue turbid, delamination and precipitation, sticky film, affecting the drying speed. Now, most manufacturers do not add or add less zinc oxide or use a small amount of alkaline zinc carbonate in the formulation of cold adhesive CR adhesive. The active magnesium oxide in the cold adhesive CR adhesive and resin chelating, to prevent the adhesive liquid delamination and precipitation, can make the adhesive liquid transparent, heat-resistant, fast drying speed, and improve the adhesive force. At the same time, the active magnesium oxide absorbs the acid in the glue. Reduce the amount of zinc oxide, increase the amount of magnesium oxide, can improve the performance of the glue. But the dosage of magnesium oxide is too large, the stability of the glue will decrease. Generally suitable dosage of about 8-12 parts. The effect of the dosage of magnesium oxide on the bond strength is shown in the figure below the table:
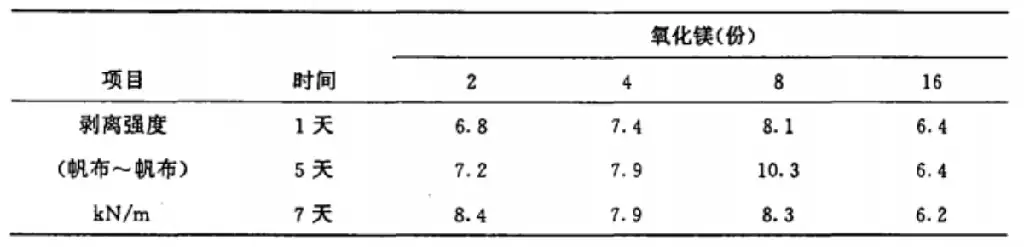
2. The role of active magnesium oxide in the pre-reaction
The main component of CR adhesive is not only CR, but also resin. Resin has a greater influence on CR adhesive. The role of the resin to improve adhesion, improve cohesive strength, prolong the adhesion retention time. Commonly used resins: tert-butylphenol formaldehyde resin, mushroom ene phenol formaldehyde resin, petroleum resin, rosin resin and so on. Among them, tert-butyl phenolic resin has the best effect.
If the resin is directly added to the CR adhesive modification effect is very poor, and very easy to produce delamination. Only by adding the resin with magnesium oxide after pre-reaction, it will significantly improve the bonding strength, heat resistance, layer stability and storage stability. Resin and magnesium oxide pre-reaction to generate chelates. The quality of resin, the activity of magnesium oxide, the choice of solvent and catalyst, reaction temperature, reaction time and other factors have a great influence on the pre-reaction. Now commonly used reaction conditions for the amount of magnesium oxide for 10% of the resin, and add about 1% of the amount of resin in water (or triethanolamine, morin, N a methyl a 2 a bilobalide ketone and other weakly alkaline organic compounds) as a catalyst, stirring in the solvent reaction, the solvent and the resin in equal quantities, the temperature of 20-25 ° C, the time of 6 a 8 hours. The structural formula of the chelating compound is:
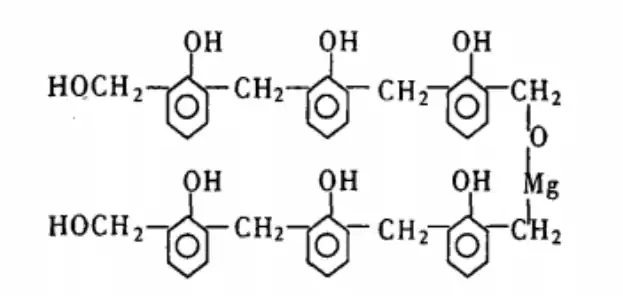
In the chelating reaction process, active magnesium oxide reacts with tert-butyl phenolic resin, which requires high activity of active magnesium oxide (iodine-absorbing value is more than 100 mg/g ), large specific surface area, fine particles, good dispersion, and moderate stacking density (0.2 g/cm3-0.3 g/cm3). Large stacking density, easy precipitation; small stacking density, harsh operating environment. In addition, it is necessary to prevent the active magnesium oxide from absorbing moisture. Because, moisture adsorption on the surface of activated magnesium oxide, part of the inner and outer surface wetting, so that the activity of activated magnesium oxide is weakened, affecting the chelating reaction. So before use, active magnesium oxide should strictly control the moisture content, preferably drying. The chelates generated by the pre-reaction should meet the following requirements: pre-reaction ash content is greater than 6%, the melting or decomposition temperature of the chelates is greater than 250 ℃; the appearance of light yellow, and does not change; viscosity is greater than 2000 mpas; placed overnight little or almost no precipitation.
The effects of pre-reaction of resin with magnesium oxide on improving the performance of CR adhesives are shown in the following table:
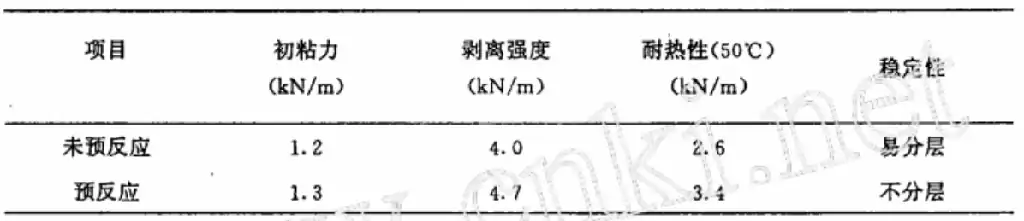
3. Solvent-based CR adhesive basic formula and process
3.1 Basic formula: mass parts
CR | 100 |
Tert-butyl phenol Tsuen resin | 45 |
Active magnesium oxide | 8 |
Active oxidation (or alkaline zinc carbonate) | 1 |
Antioxidant 264 | 1 |
Water | 1 |
Mixed solvent | 500 |
Solvent-based CR adhesives are mainly used in the footwear industry, construction industry, automobile manufacturing industry. According to the different uses, the composition can be adjusted appropriately on the basis of the basic formula, such as adding reinforcing agent white carbon black, changing the mixed solvent components.
3.2 Preparation process
Activated magnesium oxide is divided into two parts, one part is used as an acid absorber and the other part is used as a reactant for resin. The preparation process includes three steps of refining, pre-reaction and preparation of glue.
Rubber refining: CR in the open refiner, low-temperature plasticizing, mixing, under the sheet, and then put into the automatic cutting machine cut into small pieces of sheet for use. In the mixing process, part of the active magnesium oxide and antioxidant are added first, and zinc oxide or alkaline zinc carbonate is added last.
Pre-reaction: add part of active magnesium oxide and resin in the mixed solvent, add water after stirring for a certain time, and react at a certain temperature to get the pre-reaction liquid.
Preparation of glue: add mixed solvents in the glue mixing kettle, add mixing glue, stir to dissolve completely, then add the pre-reaction liquid and the rest of the mixed solvents, stir well to make the product.