Nickel and cobalt are valuable metals with a very wide range of uses. The methods of extracting nickel and cobalt from nickel and cobalt-bearing ores are broadly divided into two categories, one is pyrometallurgical smelting, and the other is hydrometallurgical smelting. As wet smelting has the advantages of small energy consumption, less pollution, environmental protection, etc., it has been widely used in recent years, especially active magnesium oxide plays an indispensable role in nickel and cobalt refining.
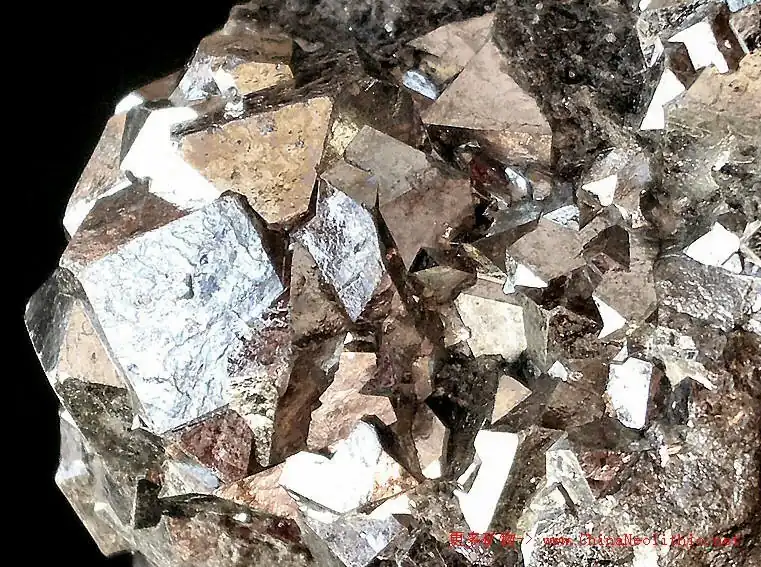
The current process for producing nickel and cobalt in the DRC includes making a slurry of nickel and cobalt containing ores, acid leaching, and obtaining a leaching slurry; injecting said leaching slurry into an atmospheric pressure circulating leaching tank, and adding a neutralizing agent to the atmospheric pressure circulating leaching tank to neutralize the leaching slurry; carrying out a solid-liquid separation of the neutralized leaching slurry, and obtaining a leaching liquid and a leaching residue; carrying out a section of purification of the said leaching liquid in order to remove iron and aluminum, and obtaining A section of purification liquid and a section of purification slag containing iron and aluminum; a second section of purification of said section of purification liquid to remove the remaining iron and aluminum again, obtaining a second section of purification liquid and a second section of purification slag; returning said second section of purification slag to said atmospheric pressure circulating leaching tank, in order to recover the valuable metals contained in the second section of purification slag; and carrying out nickel and cobalt precipitation on said second section of purification liquid.
Activated magnesium oxide was used to enrich nickel and cobalt by selective precipitation from sulfate media containing manganese and magnesium. The results show that the optimal precipitation conditions are as follows: after slurrying, add 2 times the theoretical amount of activated magnesium oxide, reaction residence time of 6h, precipitation temperature of 25℃. Under these conditions, the precipitation rates of nickel and cobalt were 97.96% and 96.43%, and the contents of nickel, cobalt, manganese and magnesium oxide in the precipitates were 8.51%, 13.05%, 2.29% and 4.97%, respectively. When 0.2g of flocculant AN905 was added to each cubic meter of the slurry, the average static free settling velocity of the slurry was 180mm/min.