The main components of cement clinker are four compounds such as CaO, SiO2, Al2O3 and Fe2O3, and the secondary components are compounds such as MgO, R2O and SO3, while the MgO content is allowed to be up to 5%, which is the most abundant of the secondary components. It is usually believed that MgO affects the stability of cement products and the limiting value is stipulated, but actually MgO affects the calcination of clinker to a certain extent, which is often neglected. Now according to the research results at home and abroad and plant production practice, discuss the influence of MgO on clinker calcination and its product properties for the reference of relevant technical personnel.
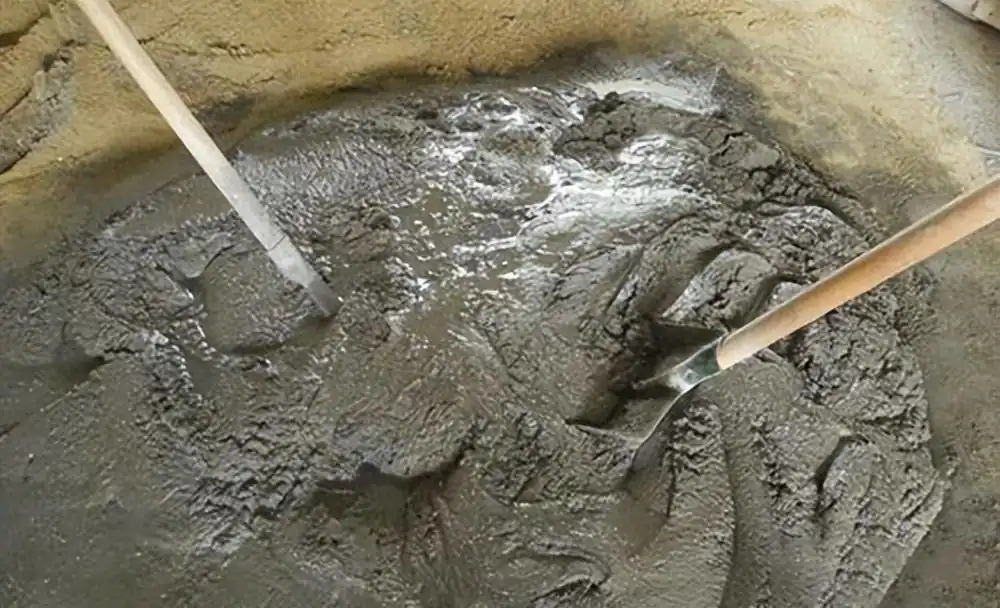
1、MgO in cement raw materials
Cement production, the raw material in the MgO mainly from the limestone in the magnesium minerals, these minerals are mainly magnesium silicate, dolomite, magnesite, iron dolomite and other different types exist. When MgO in limestone exists in the form of magnesium silicate, uniformly distributed and fine (1-5μm) magnesite crystals can be obtained, whereas when it exists in the form of dolomite or magnesite, coarse (25-30μm) magnesite crystals are easily generated. Our institute has tested the effect of MgO content on clinker strength of limestone formed in different ages, and found that the content of MgO in limestone has a certain effect on clinker strength, and the general trend is that the higher the content of MgO in limestone, the lower the clinker strength. According to the test study, the decomposition temperature of MgCO3 in magnesium minerals is 660-700℃, the decomposition temperature of Mg(CO3)2 in dolomite is 800℃, and the decomposition temperature of CaCO3 in limestone is close to 900℃. In the process of cement clinker production, MgO is formed first than CaO.
2, MgO effect on clinker calcination
Clinker calcination, about 2% of MgO and clinker minerals combined into a solid melt, such solid melt is very much, such as CaO-MgO-SiO2, 2CaO-MgO-SiO2, 2CaO-MgO-2SiO2, 3CaO-MgO-2SiO, 7CaO-MgO-2Al2O3, 3CaO-MgO-2Al2O3, MgO- Al2O3, MgO-Fe2O3, and C3MS2, etc. The stabilization temperature of such compounds is in the range of 1200-1350°C, while it may also contain some trace elements. At temperatures above 1400°C, the MgO compounds decompose and crystallize out of the melt. When clinker contains a small amount of MgO with fine magnesite lattice, it can reduce the clinker liquid phase generation temperature, increase the number of liquid phase, reduce the viscosity of liquid phase, increase the surface tension of liquid phase, which is conducive to the clinker formation and agglomeration, and also conducive to the generation of C3S, and it can also improve the clinker color. When the MgO of coarse magnesite crystals is more than 2%, it is easy to form magnesite crystals, resulting in poor clinker stability. When the content of magnesium oxide is too high, it is easy to generate large, knot circle and knot thick kiln skin, as well as the surface of the liquid phase of clinker particles, such clinker is easy to damage the grate cooler grate plate.
3, MgO on clinker grain effect
3.1 Factors affecting clinker granulation
Clinker particles in the kiln is formed under the action of the liquid phase (some information called melt), the liquid phase in the crystal outside the formation of capillary bridges. Liquid-phase capillary bridges play two roles: one is to make the particles together, the other role is to serve as an intermediate medium, so that CaO and C2S diffusion in the molten state to generate C3S, the strength of the particles depends on the strength of the capillary bridges, the strength of the bridge, that is, connecting the particles of the force with the liquid-phase surface tension and the reduction of the particle diameter and increase. The number of capillary bridges is inversely proportional to the square root of the particle diameter. To form good particles, there must be enough liquid phase, and require particles in the liquid phase distribution, the formation of higher surface tension, lower viscosity of the liquid phase, appropriate time and temperature of granulation.
3.2 Effect of MgO on liquid phase properties
3.2.1 Liquid phase quantity
The amount of clinker liquid phase is too small to not easy to crystallize, too much easy to crystallize into dense bulk clinker. The amount of liquid phase is related to the content of Al2O3, Fe2O3, K2O, Na2O and MgO contained in the liquid phase. From the liquid phase volume calculation formula published abroad in recent years, the coefficient of MgO can be improved, indicating that MgO has a greater impact on the liquid phase volume, and the coefficient of Fe2O3 is close. Its calculation formula is:
Liquid phase volume at 1400°C
L=3.0Al2O3+2.25Fe2O3+K2O+Na2O+MgO
The liquid phase amount is most favorable for agglomeration when it is 25-28%.
Multiply the value by a factor of 1.5 when the MgO content exceeds 2% or more.
3.2.2 Liquid phase surface tension
Liquid phase surface tension is an important property of the liquid phase, and has a direct relationship with the granulation. Liquid-phase surface tension increases easy granulation, clinker particle size and liquid-phase surface tension is a good linear relationship (see Figure 1).
The surface tension of the liquid phase is related to the electronegativity of the outer electrons of the elements (see Figure 2), some elements such as K, Cl, S have lower surface tension values, which are not favorable to granulation, while Mg, Al and other elements have higher surface tension values, which are favorable to granulation.
3.2.3 Liquid phase viscosity
The liquid phase viscosity value of clinker of different compositions is different, generally speaking, the liquid phase viscosity value is reduced, which is favorable to CaO and C2S diffusion in the liquid phase to generate C3S, and also easy to granulate, the liquid phase viscosity is related to the temperature, and it decreases with the increase of temperature.
The liquid phase viscosity value of several elements coexisting is not the superposition of the liquid phase viscosity value of a single element.
In recent years, some domestic units have published reports that MgO, R2O, SO3 have a greater effect on crusting and granulation. To explain this phenomenon, the liquid-phase isoviscosity line in the presence of MgO-R2O-SO3 composite is shown in Fig. 3. From Fig. 3, the increase in the content of R2O increases the viscosity value, which is unfavorable to the granulation; the increase in the content of SO3 reduces the viscosity value, but the viscosity value of SO3 is much lower than that of R2O, so the granulation is improved by the presence of SO3; if the content of R2O, R2O and SO3 is increased, the viscosity value is reduced, so the viscosity value of SO3 is lower than that of R2O. improved; if R2O, SO3 are present, MgO content increases, the liquid phase viscosity value is greatly reduced, which is favorable for granulation.
The viscosity of the liquid phase is related to the negative electronegativity of the outer electrons of the elements, and the viscosity of the liquid phase decreases gradually according to the order of their decreasing alkalinity (K-Na-Ca-Mg), and MgO only has a proper decrease in the viscosity of the liquid phase (see Fig. 2)
From some experiments, the liquid-phase surface tension and viscosity of clinker changed after the addition of Mg2+, SO32-, K– and other ions in appropriate amounts to the calcined clinker composition.The study conducted by Ocoknh showed that the clinker containing 25-35% liquid phase at 1450°C had a viscosity of 0.16 Pa.S and a surface tension of 0.58 N/m, and that the addition of MgO and other compounds had a change in the liquid-phase surface tension and viscosity. Both surface tension and liquid phase viscosity changed, affecting clinker agglomeration (see Table 1). In addition, in addition to the effect of MgO content on the liquid phase surface tension and liquid phase viscosity, it is also necessary to consider the factors of other components within the liquid phase.
4. Effect of MgO on clinker strength
MgO exists in the clinker, will affect the amount of CaO, and thus MgO to a certain extent affect the strength of clinker. In order to moderate the impact of MgO on clinker strength, in the production of cement clinker, should try to increase the lime saturation factor KH and silicate rate SM value, and correspondingly increase the content of C3S and C2S, in order to improve the strength of clinker.
5、Effect of MgO on product stability
In the silicate cement clinker, MgO solid melt up to 2% of the total amount of excess MgO that is crystallized out of the free form of magnesite, it will produce harmful effects.
Clinker in the magnesite crystal generation rate and magnesium mineral decomposition temperature, the lower the decomposition temperature, the greater the opportunity for crystal growth. In general, dolomite and other high magnesium raw materials decomposition temperature is higher, easy to generate large lattice MgO.
Magnesite crystallization size changes with different cooling speeds, fast cooling when the crystals are fine, magnesite hydration is slow, it takes months or even years to be obvious, hydration generates Mg (OH)2, volume expansion of 148%, resulting in poor stability. The severity of magnesite expansion is related to its content, crystal size, etc. Magnesite crystals less than 1 μm and the content of 5%, causing only slight expansion, magnesite crystals for 5-7 μm and the content of 3%, will cause serious expansion.
6, moderate the impact of MgO on production and product quality
The main composition of raw material is CaO, SiO2, Al2O3, Fe2O3 four, in the process of clinker calcination, mainly by the composition of the above four oxides calculated by the lime saturation coefficient KH, silicate rate SM, aluminum oxygen rate AM and SiO2, CaCO3 and other particles gradation, that is, the ease of burning of the raw material determines the firing conditions. However, when the MgO content is high, it has an effect on the amount of clinker liquid phase, liquid phase surface tension, liquid phase viscosity, as well as clinker calcination temperature, clinker agglomeration, strength, as well as kiln rings, crust, and so on. If in the production process, the influence of MgO appears, mitigation measures should be taken from the following aspects.
6.1 Do a good job of raw material batching and homogenization:
Foreign companies in the study proposed that within the raw material containing MgO, the lime saturation factor should be adjusted as follows:
LSF=100CaO/(2.80SiO2+1.18Al2O3+0.65Fe2O3) (without MgO)
LSF=100(CaO+0.75MgO)/(2.80SiO2+1.18Al2O3+0.65Fe2O3) (MgO<2%)
LSF=100 (CaO +1.150 MgO)/(2.80SiO2+1.18Al2O3+0.65Fe2O3) (MgO>2%)
Do a good job of homogenization of raw materials to ensure that the MgO content in the raw material is uniform into the kiln.
6.2 Control the appropriate liquid phase volume, liquid phase surface tension, liquid phase viscosity
Liquid phase volume is an important factor in clinker agglomeration. When calculating the liquid phase volume, attention should be paid to the correction factor when MgO exceeds 2%, and the factor of alkali content should also be considered. In order to moderate the impact of MgO on the amount of liquid phase, under the premise of improving the quality of clinker, appropriately increase the lime saturation factor KH and silicate rate SM value, reduce the content of Al2O3 and Fe2O3, slow down the impact of MgO on the amount of liquid phase, and accordingly slow down the tendency to form large balls. Meanwhile, the increase of KH value and SM value increases the content of CaO and SiO2, as well as the generation of C3S and C2S and clinker calcination temperature, which is conducive to improving the clinker strength.
MgO content affects the liquid phase surface tension and liquid phase viscosity to a certain extent, which affects clinker granulation. In the production process, when the liquid phase surface tension and liquid phase viscosity cause clinker to form large balls or too fine dust clinker, in the adjustment measures, the MgO content can be considered to be adjusted by adjusting the value of the batching rate, but the influence of the alkalinity, sulfide and other trace elements brought in by the raw materials and fuels should be considered.
Due to the different composition of raw materials in each production line, different dosing rate value, SiO2, CaCO3 and other particles with different gradation, the number of MgO and different crystal size, alkali (R2O), SO3 and trace elements are not the same, coupled with the amount of liquid phase, liquid-phase surface tension, liquid-phase viscosity of the sampling and determination of the difficulty of the actual production of the calculations and tests can only be carried out through analysis, judgment, measurement, trial firing after production. It is difficult to calculate and test in the actual production, and can only be analyzed and judged through the calculation and production after trial firing. From the production of some domestic production lines with high MgO content, by adjusting the values of KH and SM, the clinker with better grains and higher strength can be produced, and the overall situation is summarized as follows:
(1) When the content of MgO in the raw material is high and the burnability is good, the grindability of SiO2 is good and the particles are fine, and the alkali content and sulfur content do not have much effect on the viscosity of the liquid phase, C2S is conducive to combining with CaO to produce C3S, then the SM value can be increased to more than 3.60, and the grains are even in the process of production, and the content of f-CaO is low, so that the strength of the clinker is high.
(2) Raw material in the MgO content is high but easy to burn poor, SiO2 easy to grind poor and coarse particles, in addition to raw materials with high alkali content, the liquid phase viscosity has a greater impact on the liquid phase is not conducive to the liquid phase of C2S and f-CaO combined to generate C3S. in the production process, in order to ease the impact of MgO on the amount of liquid phase, you can increase the value of SM; but after the increase in the value of SM, it is even more detrimental to the generation of C3S, easy to make the f-CaO content, the strength of clinker is higher. Easy to make f-CaO content is high; in order to reduce the f-CaO content, production to increase the firing temperature, but also easy to increase the lattice of C3S is easy to form flying sand material, is not conducive to the improvement of clinker strength; this condition, the SM value is very difficult to improve.
The above situation shows that the raw material of each production line is not consistent with the ease of burning, its particle grading is not consistent, the MgO content of limestone is not equal and the crystal size is different, in addition to the alkali content of raw fuel into the raw material is also not consistent, at this time can only be combined with the actual situation, through the analysis, to find the optimization point, in order to improve the strength of clinker.
6.3 Operation measures
(1) In the production process, increase the air volume of the kiln fan to minimize the reducing atmosphere in the kiln, to avoid the decomposition of sulfate in the reducing atmosphere caused by the kiln back to form a long thick kiln skin, to slow down the MgO content of high kiln materials appearing circles, eggs, thus further aggravating the kiln ventilation is poor, the reducing atmosphere aggravated by the generation of the malignant operating conditions.
(2) Appropriately accelerate the kiln speed to reduce the tendency to form thick kiln skin.
(3) Avoid overfiring at the kiln head, reduce the large clinker with liquid phase on the surface falling into the grate cooler and damaging the grate plate at the front end, or the formation of large crystal lattice clinker with liquid phase on the surface of the cooler inlet bonded into a snowman’s accident.
(4) Strengthen the grate cooler front ventilation, on the one hand, make the clinker cold, conducive to the formation of small lattice MgO minerals, accordingly slowing down the expansion effect of MgO hydration; on the other hand, the surface of the liquid phase of the material ball curing, to avoid overheating damage to the grate plate.
Conclusion
MgO is the most abundant minor compound in clinker minerals, which affects the calcination, grain formation, strength and stability of clinker. In the production process, when encountering the high content of MgO on the calcination of cement clinker, we should analyze the burnability of raw materials and particle grading, combined with the content of MgO and the status of alkali (R2O) and SO3 brought in by the raw materials and fuels, make judgments, make calculations, and adjust the value of clinker rate, carry out the necessary tests and trial burns, and carry out the industrialized production on the basis of success, which will make the system show low process accidents, product stability and stability. The system presents a benign production condition with low process accident rate, high product quality and high yield, and low consumption.