Magnesite was utilized to prepare aqueous heavy magnesium solution, which was used as the precursor solution for the preparation of magnesium carbonate trihydrate whiskers by thermal decomposition method. The effects of pyrolysis time, concentration of heavy magnesium aqueous solution and stirring rate on the composition and morphology of the products were investigated with the help of X-ray diffraction (XRD) and scanning electron microscopy (SEM), and the crystallization kinetics was also studied. The results showed that rod-shaped MgCO3·3H2O whiskers with an average diameter of 6.0 μm and an average length of 100 μm were prepared by thermal decomposition at a temperature of 50 ℃, a pyrolysis time of 120 min, and a heavy magnesium water mass concentration of 2.75-3.39 g/L. The results showed that the average diameter of MgCO3·3H2O whiskers was 6.0 μm and the average length was 100 μm. With the increase of time and concentration, the surface or the whole rod structure of MgCO3·3H2O crystals would dissolve to reform amorphous particles and gradually form porous rods 4MgCO3·Mg(OH)2·3H2O.The stirring rate affects the yield of the MgCO3·3H2O whiskers. In the MgCO3·3H2O crystals, the [MgO6] ortho-octahedra are connected through Mg-O bonds in a co vertices are tightly connected and infinitely linked along the [010] direction, where the chemical bonding force is stronger, to form long chains. The results of linear fitting of the crystallization kinetics indicate that the induction period time is shortened by increasing the concentration of heavy magnesium aqueous solution.
INTRODUCTION
Magnesium carbonate trihydrate whisker (MgCO3·3H2O) is a micrometer-sized magnesium carbonate single crystal, which is cost-effective and a new type of multifunctional fine inorganic material with important industrial applications and great economic potential, and has attracted much attention in the field of new materials. Due to its extremely high purity and low thermal decomposition temperature, MgCO3·3H2O whisker can be used as a precursor for the preparation of fine magnesium salt products such as magnesium nitrate, magnesium sulfate, magnesium hydroxide and magnesium oxide. Due to the good mesostability, MgCO3·3H2O whiskers are also mainly used as soft templates for the synthesis of hierarchical structural materials such as mesoporous titanium dioxide, silicon dioxide and nickel oxide. Due to the excellent physical and chemical properties and excellent mechanical properties, rod-shaped MgCO3·3H2O whiskers are widely used as reinforcing fillers in pharmaceutical, cosmetic, plastic, coating, rubber, glass, ceramic and printing industries.
At present, domestic and foreign researchers mainly use co-precipitation method to synthesize MgCO3·3H2O crystals.Mitsuhashi et al. used Mg(OH)2 aqueous solution to react with CO2 to produce needle-like MgCO3·3H2O crystals.Kovacheva et al. used brine and carbonate as the raw materials to prepare the sub-stable rod-like MgCO3·3H2O crystals and the stable alkaline magnesium carbonate crystals, and investigated the phase transition process. and the phase transition process was studied.G. Jauffret et al synthesized acicular MgCO3·3H2O crystals in a MgO-CO2-H2O multiphase system and investigated the thermal decomposition process of MgCO3·3H2O. Wang Y et al. prepared acicular magnesium carbonate trihydrate with a diameter of about 5 μm by using MgCl2 and (NH4)2CO3 as reaction materials, and it was found that the crystal morphology could be controlled by controlling the conditions of reaction temperature, equilibrium time, and stirring speed. Shao Minghao et al. prepared rod-like MgCO3·3H2O crystals with diameters of 10-20 μm in MgCl2-Na2CO3-NaHCO3 solution and analyzed the effect of pH on whisker growth. Yang Chen et al. prepared rod-shaped MgCO3·3H2O crystals with high aspect ratio by using magnesium chloride and soda ash as the reaction raw materials and SDS as the additive, and initially investigated the crystal growth process of magnesium carbonate trihydrate from the viewpoint of crystal nucleation and growth.Du et al. prepared needle-shaped MgCO3·3H2O crystals as well as flake-shaped MgCO3·3H2O crystals by using the co-precipitation method with MgSO4 and (NH4)2CO3 as the raw materials. 4MgCO3·Mg(OH)2·4H2O crystals, mainly investigating the phase transfer process of magnesium carbonate trihydrate. For the purpose of morphology modulation, numerous researchers have applied additives to the controlled synthesis of magnesium carbonate trihydrate crystals. Yan Pingke et al. used MgCl2·6H2O or MgSO4·7H2O and NH4HCO3 as raw materials and different kinds of surfactants as crystal shape controlling agents to prepare rod-like, radial, bundle-like and shark’s-fin-like MgCO3·3H2O crystals, respectively, and investigated the crystal stability and morphology regulating process. Wu Dan et al. prepared rod-shaped MgCO3·3H2O whiskers from MgCl2·6H2O and NH4HCO3, and the test conditions were applicable to the brine resource system. The whiskers of magnesium carbonate trihydrate with high aspect ratio were prepared by Su-Ping Wang using industrial magnesium hydroxide and CO2 as raw materials and sodium citrate as additive.
In summary, researchers can synthesize MgCO3·3H2O whiskers by using soluble magnesium salts and carbonate or bicarbonate as raw materials, and adopting the precipitation method in which one kind of raw material is dropped into the other, and this process exists the problems of higher preparation cost and by-products that can easily lead to the environmental pollution; in addition, the above reports have not carried out an exhaustive study of the formation mechanism of the crystal morphology of MgCO3·3H2O.
China has the resource advantage of rich reserves of magnesium-containing minerals with good quality, and the use of magnesite, dolomite, magnesite, salt lake brine, etc. as magnesium sources for the preparation of magnesium carbonate trihydrate whiskers has the advantages of cheap and easy to obtain raw materials and a wide range of sources. Chen Min et al. synthesized magnesium carbonate crystals with a diameter of about 5 μm and an aspect ratio of 10-20 by using magnesite as a raw material using the hydrated carbonation method. Liu et al. obtained MgCO3·3H2O whiskers with lengths of 40~80 μm by preparing a heavy magnesium aqueous solution through the hydrated carbonation method using lightly burned dolomite as raw material and regulating the temperature and time.
On the basis of the previous research, this study used natural magnesite as raw material to prepare heavy magnesium aqueous solution, and used this as the precursor solution to prepare MgCO3·3H2O whiskers by thermal decomposition method, mainly investigated the effects of the thermal decomposition time, the concentration of heavy magnesium aqueous solution, and the stirring rate on the composition and morphology of the crystals and analyzed the kinetic process of the crystallization of MgCO3·3H2O.
1 Test
1.1 Test raw materials
The test raw material was natural magnesite produced in Kuandian, Liaoning Province, with the main chemical composition of MgO (47.61%), CaO (0.50%), SiO2 (0.66%), and the purity was about 99.58%. Lightly burnt magnesium oxide was obtained by calcining magnesite in a muffle furnace at 750 °C for 3.0 h. The MgO content was 96.89%.
1.2 Preparation of magnesium carbonate trihydrate whiskers
Grind and sieve the lightly burnt magnesium oxide, weigh the magnesium oxide with a particle size of ﹤74 μm and mix it with hot water in the ratio of m(MgO) : m(H2O) of 1 : 40, stir it for a period of time in a water bath at 60 ℃ at a rate of 500 r/min and then cool it down to room temperature, and then sieve and remove impurities to obtain the hydrated solution. To the above hydration solution into the CO2, homemade ice water water bath stirring, when the solution pH value of 7.5 (or lower), stop the ventilation and stirring, filtered to obtain heavy magnesium aqueous solution. Deionized water was used to adjust the concentration of heavy magnesium aqueous solution, different concentrations of heavy magnesium aqueous solution was placed in a 50 ℃ water bath, stirring pyrolysis at different rates for a certain period of time after filtration, the filter cake was washed with deionized water, filtered, and then placed into the 60 ℃ electric blower drying oven drying for 6.0 h, to obtain a white powder.
1.3 Detection and characterization
The X-Pert type X-ray diffractometer (XRD) from Panaco, the Netherlands, was used to characterize the physical composition of the products, with a radiation source of copper target K, λ = 0.154 1 nm, nickel filter, super energy detector, X-ray tube operating voltage of 40 kV, tube current of 45 mA, scanning rate of 4 °-min-1, scanning range of 2 θ = 5 ° ~ 90 °; a JEOL JSM-6360LV scanning electron microscope (SEM) was used to observe the morphology of the products with an accelerating voltage of 20.0 kV.
2 RESULTS AND DISCUSSION
2.1 Effect of pyrolysis time
Figure 1 shows the XRD images of the products obtained from the aqueous solution of heavy magnesium pyrolyzed at 50 ℃ for different times, and Figure 2 shows the SEM images of the products obtained from different pyrolysis times.
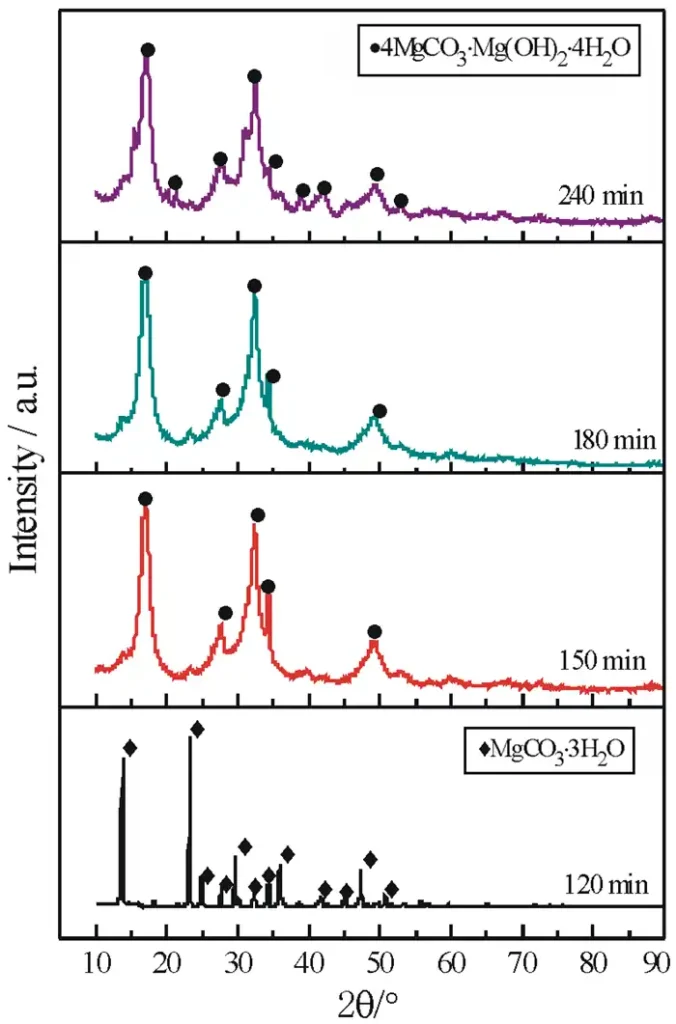
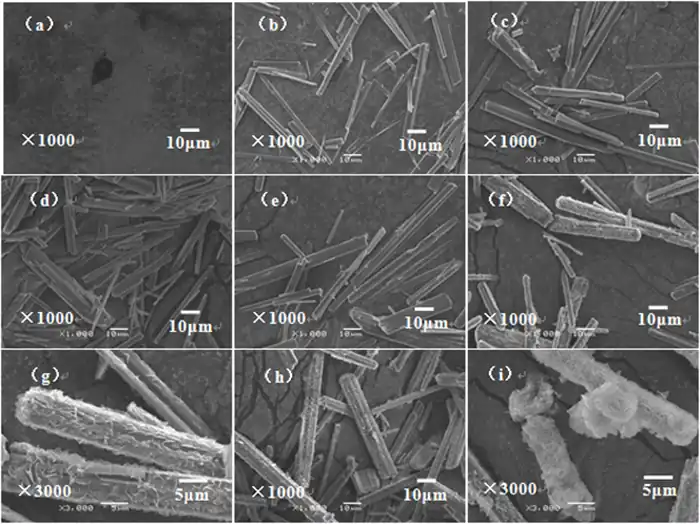
(a)5 min;(b)30 min;(c)60 min;(d)90 min;(e)120 min;
(f)150 min;(g)150 minProduct partial enlargement;(h)180 min;(i)240 min
As can be seen in Fig. 1, all the diffraction peaks of the product obtained at 120 min are consistent with the XRD standard pattern (JCPDS 00-020-0669) of magnesium carbonate trihydrate (MgCO3·3H2O) in the monoclinic crystal system, with the space group P121/n1(14) and the lattice constants of a=12.11 Å,b=5.365 Å,c=7.697 Å,β=90.42°. The diffraction peaks were sharp and of high intensity, and no impurity peaks were found, indicating that the MgCO3·3H2O prepared at this time was well crystallized without the presence of other substances. 150~180 min, the characteristic peaks of MgCO3·3H2O in the product disappeared, and the positions of the diffraction peaks were all the same as those of the XRD standard pattern of alkaline magnesium carbonate (4MgCO3·Mg(OH)2·4H2O) (JCPDS 00-025-0513) agreed with the lattice constants of a=10.11 Å,b=8.95 Å,c=8.38 Å,β=114.44°. Compared with the characteristic peaks of MgCO3·3H2O at 120 min, the diffraction peaks of 4MgCO3·Mg(OH)2·3H2O are broad, with low intensity and non-smooth base, indicating that the MgCO3·3H2O crystals disappeared during that time, and the small-sized and poorly crystalline 4MgCO3·Mg(OH)2·3H2O was obtained.The diffraction peaks of the product at 240 min At 240 min, the number of diffraction peaks increased, and the position was consistent with that of 4MgCO3·Mg(OH)2·3H2O, and the peaks were narrow and the base was smooth, which indicated that the 4MgCO3·Mg(OH)2·3H2O obtained at this time was well crystallized.The XRD results showed that, keeping the other conditions unchanged, the product prepared at 120 min was the well-crystallized MgCO3·3H2O, and the product was the well-crystallized MgCO3·3H2O, and the product was the well-crystallized MgCO3·3H2O, and the product was the well-crystallized MgCO3·3H2O when pyrolysis time continued to be prolonged. When the pyrolysis time continued to be extended, MgCO3·3H2O was gradually transformed into 4MgCO3·Mg(OH)2·3H2O.
As shown in Figure 2, at 5 min, the product in the solution is amorphous particles (Figure 2a), and from 30 to 120 min, the amorphous particles gradually transform into smooth needle-like crystals or rod-like whiskers. As the pyrolysis time increases, the length of the rod-like whiskers increases, the aspect ratio increases, and the particle size uniformity improves (Figure 2b to 2d). At 120 min, the surface of the rod-like MgCO3·3H2O whiskers is very smooth, with an average diameter of 6.0 μm and an average length of 100 μm (Figure 2e). At 150 min, the product is still a rod-like whisker with a large aspect ratio, but from the enlarged image (Figure 2g), it can be seen that the surface of the rod-like whiskers becomes rough, and flaky particles are obviously grown. At 180 min, the length of the rod-like crystals with rough surfaces became shorter, and some short and thick columnar crystals were mixed in the product (Figure 2h). At 240 min, the smooth rod-like crystals disappeared, and the products were all rod-like 4MgCO3·Mg(OH)2·3H2O crystals with a porous structure on the surface. The porous structure was composed of overlapping nanosheets, and the leaves were curved. The thickness of the leaves was only a few nanometers (Figure 2i).
Combined with the results of previous studies and the above analysis, it can be seen that thermal decomposition of heavy magnesium water at low temperature (≤50 ℃) firstly produces sub-stable phase MgCO3·3H2O crystals, and with the prolongation of time, the MgCO3·3H2O is gradually transformed into 4MgCO3·Mg(OH)2·3H2O, so the time of pyrolysis was chosen to be 120 min.
2.2 Effect of the mass concentration of heavy magnesium aqueous solution
Figure 3 shows the XRD patterns of the products obtained by pyrolysis of aqueous solutions of heavy magnesium with different mass concentrations (referred to as concentrations), and Figure 4 shows the SEM patterns of the products obtained by pyrolysis of Mg(HCO3)2 solutions with different concentrations.
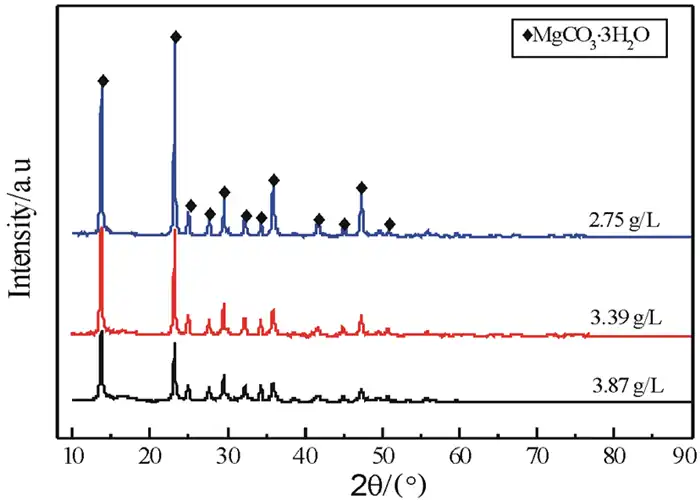
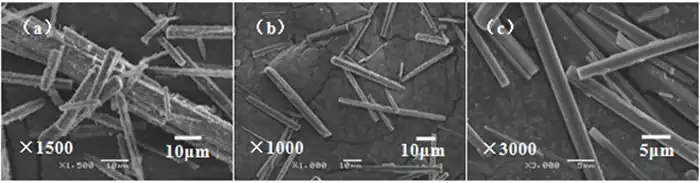
From the XRD spectra of Figure 3, it can be seen that at 50 °C, the products obtained by pyrolysis of heavy magnesium aqueous solution with different concentrations are all MgCO3·3H2O, and the base of the diffraction peak is smooth without other impurities, indicating that the MgCO3·3H2O crystals obtained at different concentrations are well crystallized and have high relative purity; but the diffraction peak intensity of the MgCO3·3H2O crystals obtained at lower concentrations is much greater than the peak intensity of the product obtained at higher concentrations, indicating that the crystallinity of the MgCO3·3H2O crystals obtained at lower concentrations is better than that of the crystals obtained at higher concentrations.
Observing Figure 4, it is found that when the concentration of heavy magnesium aqueous solution is high, the products obtained are all MgCO3·3H2O crystals with granular fragments on the surface, the uniformity of the particle size becomes worse, and the aspect ratio is small (Figure 4a). When the concentration is reduced to 3.39 g/L, the product contains rod-shaped MgCO3·3H2O whiskers with rough surfaces, fragments, and very smooth surfaces, with an average diameter of 2.6 μm and an average length of 40 μm (Figure 4b). When the concentration of Mg(HCO3)2 solution was further reduced to 2.75 g/L, all the products were rod-shaped MgCO3·3H2O whiskers with very smooth surface, uniform particle size, average diameter of 2.5 μm and average length of 30 μm (Figure 4c). According to the crystallization thermodynamics theory, the greater the supersaturation of the solution, the smaller the size of the critical crystal nucleus, and the more particles that are converted into secondary crystallization centers. Therefore, the surface of the MgCO3·3H2O rod-shaped crystals obtained at higher concentrations is not smooth and many amorphous fragments are attached, which is caused by the dissolution of the generated MgCO3·3H2O.
In order to obtain magnesium carbonate trihydrate whiskers with high purity, good crystallization and smooth surface, the concentration of heavy magnesium aqueous solution is controlled between 2.75 and 3.39 g/L.
2.3 Effect of stirring rate
The heavy magnesium aqueous solution is an extremely unstable solution. The stirring intensity has a great influence on the stability of the solution. Increasing the stirring intensity can accelerate the decomposition of the heavy magnesium aqueous solution. Therefore, the effect of stirring rate on the product composition and morphology was investigated. The results are shown in Figures 5 and 6.
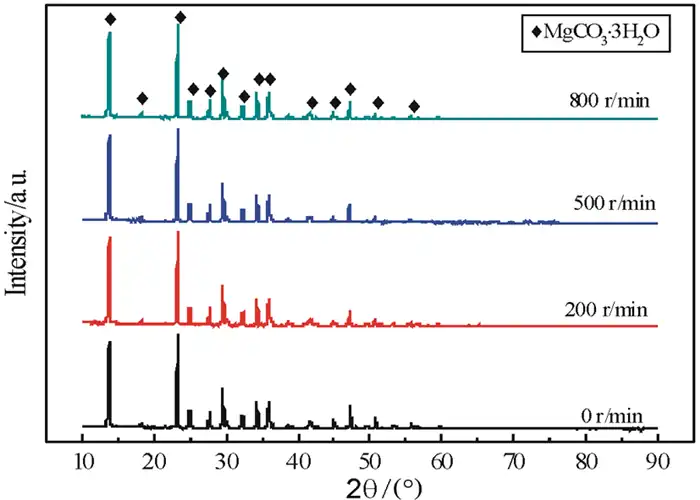
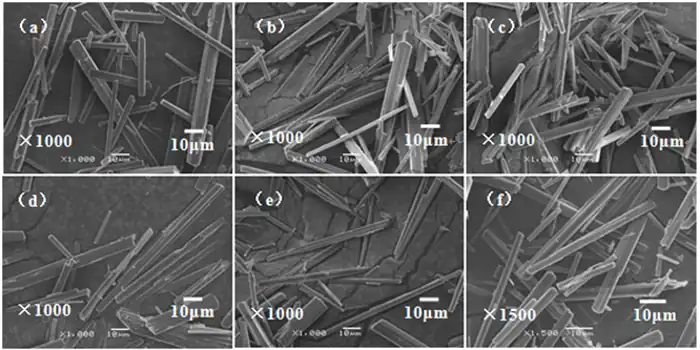
(a)0 r/min; (b)200 r/min; (c)400 r/min;
(d)500 r/min; (e)600 r/min; (f)800 r/min
Combined with the XRD patterns (Fig. 5) and SEM images (Fig. 6) of the products, it can be seen that the stirring rate does not have a significant effect on the physical composition and morphology of the products during the low-temperature thermal decomposition of heavy magnesium water. Smooth rod-shaped MgCO3·3H2O whiskers were obtained at different stirring rates, but at low rotational speeds, the yield of the product was lower and the crystallization speed was slow, while at high rotational speeds, the generated rod-shaped crystals were easily stirred up by the stirring paddles, which would cause the crystal length to become shorter and the length-to-diameter ratio to decrease. It was also found during the test that the yield of crystals was lower when there was no stirring, and the quality and yield of crystals generated were higher when stirred. This is due to the fact that when the solution is in unstirred action (i.e., at equilibrium), the first precipitates spontaneously generated in the solution are not uniformly mixed in the solution, mass transfer is more difficult, and the number of crystallization centers generated is limited, thus negatively affecting nucleation in the subsequent crystallization process. When the solution is stirred, the first spontaneously generated precipitates enter the solution near the moment when the solution becomes unstable, and the stirring effect accelerates the diffusion process from the solution body to the surface, reducing the thickness of the surface layer of the solution, which results in fluctuations in the concentration of the solution and generates localized high supersaturated zones. In these localized high supersaturated zones, the degree of supersaturation of the solution increases, and the crystal nucleation and growth rates increase accordingly. In addition, the stirring effect increases the frequency of interactions between crystals, which in turn leads to crystal fragmentation and ultimately to an increase in surface area.
In summary, considering the need to obtain whiskers with higher yields and larger diameters, a suitable stirring rate of 500 r/min was chosen.
3 Mechanism analysis
3.1 Magnesium carbonate trihydrate crystal growth motifs
According to the cell parameters in the XRD characterization results of MgCO3·3H2O, the crystal structure of MgCO3·3H2O along the direction of b-axis [010] was simulated and plotted using Diamond software, as shown in Fig. 7.
![Fig.7 Crystal structure of nesquehonite in projection parallel to a [010] Fig.7 Crystal structure of nesquehonite in projection parallel to a [010]](https://meixi-mgo.com/wp-content/uploads/2024/12/Fig.7-Crystal-structure-of-nesquehonite-in-projection-parallel-to-a-010.webp)
As can be seen in Fig. 7, the stronger O-H and C-O bond interactions formed before the crystallization process occurs form H2O and CO32-, respectively, in the crystal structure of MgCO3·3H2O, whereas the weaker Mg-O bonds formed during the crystallization process form distorted [MgO6] ortho-octahedra along the direction of [010].The growth motifs of MgCO3·3H2O are [MgO6]. In the crystal structure, each CO32- connects three [MgO6] ortho-octahedra, with two of the orthohedra connected in a co-vertex fashion and the other in a co-prismatic fashion. MgCO3·3H2O is tightly linked in a co-vertex fashion through Mg-O bonds, which are infinitely connected along the [010] direction, where the chemical bonding forces are stronger, to form long chains.
3.2 Kinetic analysis of MgCO3·3H2O crystallization
The preparation of MgCO3·3H2O whiskers from low temperature thermal decomposition of heavy magnesium aqueous solution is a complex multiphase crystallization process. From the discussion of the previous results, it can be seen that the concentration of heavy magnesium water has an important influence on the morphology and composition of magnesium carbonate trihydrate. From the previous results, it can be seen that MgCO3·3H2O crystals are produced in an intermittent crystallization process, in which the solution concentration remains practically unchanged for a certain period of time at the beginning, which is called the induction period tind, and which is one of the main kinetic features of the crystallization process. The duration of the induction period is highly dependent on factors such as supersaturation and temperature. One of the main indicators used to determine the crystallization process is the concentration of the substance in solution, since the change in concentration with time reflects the crystallization kinetics to some extent. According to the thermodynamic theory of phase generation, the induction period time is calculated as:
lgtind=kind – nNlg(c/ceq)=kind – nNlgs
Where: kind=lg[Δc/mNkNceqnN)]; mN and kN are constants; nN denotes the process order. The above relation is correct when s > 1.
Usually, the absolute supersaturation Δc, the relative supersaturation δ and the supersaturation coefficient s are used to express the degree of supersaturation, which are calculated as:
Δc=c-ceq |
δ=(c-ceq)/ceq |
s=c/ceq |
In the above three equations, c denotes the initial concentration of the solution, g·(100 mL)-1 H2O or g·(100 g)-1 H2O; ceq denotes the concentration, i.e., the solubility, of MgCO3·3H2O at the equilibrium, g·(100 mL)-1 H2O. Since MgCO3·3H2O is a substable phase crystal, its solubility decreases with the increase of temperature, and its solubility reaches the maximum value of 0.151 8 g·(100 mL)-1 H2O at 19 °C. For the convenience of calculation, the solubility of MgCO3·3H2O at 50 °C is approximately equal to 0.151 8 g·(100 mL)-1 H2O. The solubility reached the maximum value of 0.151 8 g·(100 mL)-1 H2O at 19 ℃. For the convenience of calculation, the solubility of MgCO3·3H2O at 50 ℃ was approximately equal to 0.151 8 g·(100 mL)-1 H2O.
The induction period times tind1~tind9 in the crystallization process of magnesium carbonate trihydrate corresponding to the concentrations of c1~c9 were determined during the experiment and their corresponding Δc, δ and s were calculated according to Eqs. (1)~(4), and the results are shown in Table 1.
Table 1 The supersaturation and induction time of solution during the crystallization for 50 ℃ | |||||
No. | c/g·(100 mL)-1H2O | Δc/g·(100 mL)-1H2O | δ | s | tind/s |
1# | 0.565 | 0.413 2 | 2.722 0 | 3.722 0 | 10 |
2# | 0.478 | 0.326 2 | 2.148 9 | 3.148 9 | 10 |
3# | 0.402 | 0.250 2 | 1.648 2 | 2.648 2 | 40 |
4# | 0.387 | 0.235 2 | 1.549 4 | 2.549 4 | 60 |
5# | 0.347 | 0.195 2 | 1.285 9 | 2.285 9 | 60 |
6# | 0.339 | 0.187 2 | 1.233 2 | 2.233 2 | 180 |
7# | 0.277 | 0.125 2 | 0.824 7 | 1.824 7 | 300 |
8# | 0.275 | 0.123 2 | 0.811 6 | 1.811 6 | 360 |
9# | 0.234 | 0.082 2 | 0.541 5 | 1.541 5 | 600 |
Based on the data in Table 1 and the linear fitting calculation of lgtind and lgs according to Eq. (1), the relationship equation can be obtained and the result is shown in Fig. 8.
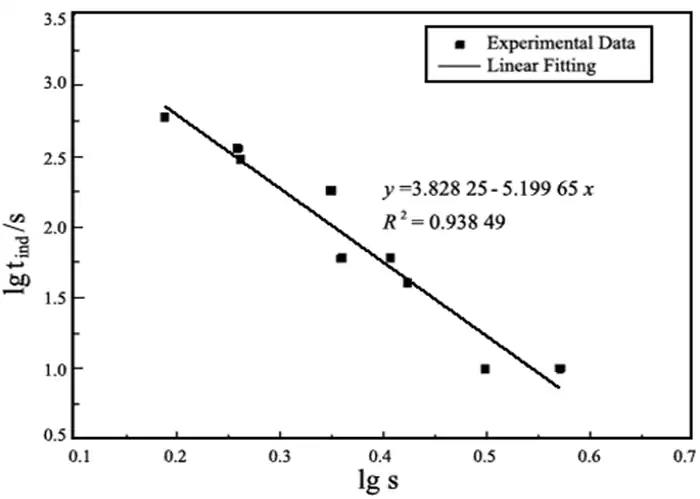
As can be seen from Fig. 8, lgtind is linearly related to f(lgs) y=3.828 25-5.199 65x, with a coefficient of determination R2=0.983 49, which indicates that the model fits well. Even if the straight line is extrapolated to the supersaturation level of lgtind→0, the value of lgs corresponding to a very small value of lgtind can be obtained, which does not change significantly due to fluctuations in the data and changes in the number of points of deployment. The reaction of thermal decomposition of heavy magnesium aqueous solution to form MgCO3·3H2O is a heat-absorbing reaction, and increasing the pyrolysis temperature favors the reaction to the right. When the temperature and other conditions are the same, the continuation time of tind is greatly prolonged with the decrease of heavy magnesium aqueous concentration and shortened with the increase of solution concentration, and the model fitting results are in good agreement with the data measured in the experiment. At the end of the induction period, i.e., at the instant when crystallization just starts to occur, the change in HCO3– ion concentration tends to decrease rapidly, while the change in CO32- ion concentration tends to increase rapidly, and a supersaturated solution of MgCO3·3H2O is formed. Due to the centripetal force between molecules, van der Waals force and hydrogen bonding with selectivity and directionality, they promote the formation of a large number of crystallization centers through addition and coordination, which makes the pyrolysis rate of heavy magnesium aqueous solution accelerated significantly. From the classical crystallization theory, when Mg2+, CO32-, OH–, Mg2+ and CO32- or Mg2+ and OH– conjugated ion pairs migrate to the surface of the crystal, they do not enter the crystal lattice immediately, but lose a degree of freedom and move freely on the surface of the crystal, thus an adsorption layer is formed at the interface between the crystal surface (crystalline phase) and the solution (substable phase) and a kinetic equilibrium is established between this adsorption layer and the heavy magnesium A kinetic equilibrium is established between this adsorption layer and the heavy magnesium solution. From the crystal growth kinetics, it can be seen that the ions or ion pairs are always easily or preferentially connected to the positions with the highest lattice attraction, so that the porous rod-like 4MgCO3·Mg(OH)2·3H2O is finally obtained, and the growth schematic is shown in Fig. 9.
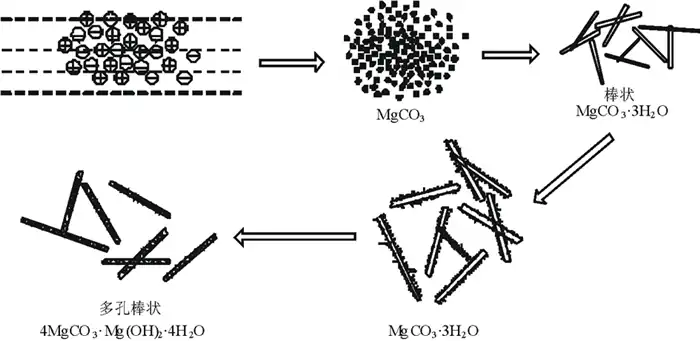
As can be seen from Fig. 9, during thermal decomposition of heavy magnesium aqueous solution, the amorphous material is first transformed into sub-stable rod-shaped MgCO3·3H2O crystals, and when the conditions such as solution concentration or pyrolysis time are changed, the surface of the rod-shaped MgCO3·3H2O crystals or the whole rod structure will dissolve to re-form the amorphous particles, and ultimately porous rods of 4MgCO3·Mg(OH)2·3H2O will be formed.
4 Conclusions
(1) When the thermal decomposition temperature is 50 ℃ and the pyrolysis time is 120 min, the thermal decomposition of heavy magnesium aqueous solution is prepared to obtain rod-like MgCO3·3H2O whiskers with a smooth surface, an average diameter of 6.0 μm and an average length of 100 μm. The time continued to be extended, and MgCO3·3H2O was gradually transformed into porous rod-like 4MgCO3·Mg(OH)2·4H2O.
(2) The concentration of heavy magnesium water has an effect on the crystallinity and surface finish of MgCO3·3H2O; the lower the concentration, the higher the crystallinity of MgCO3·3H2O and the smoother the surface. The stirring rate has no significant effect on the composition and morphology of MgCO3·3H2O, but affects the crystal yield, and the suitable stirring rate is 500 r/min.
(3) The growth motifs of MgCO3·3H2O are [MgO6] ortho-octahedra, which are tightly connected in a co-vertex manner through Mg-O bonds, and infinitely connected to form a long chain along the [010] direction, which is the direction of stronger chemical bonding force. The relationship between lgtind and f(lgs) was calculated using linear fitting as y=3.828 25-5.199 65x, with the coefficient of determination R2=0.983 49. The fitting results are in good agreement with the experimental results, where the increase in the concentration of heavy magnesium aqueous solution shortens the induction period time.
(4) During thermal decomposition of heavy magnesium aqueous solution, the amorphous material is first transformed into sub-stable rod-shaped MgCO3·3H2O crystals, and when the conditions such as solution concentration or pyrolysis time change, the surface of the rod-shaped MgCO3·3H2O crystals or the whole rod structure will dissolve to re-form the amorphous particles, and ultimately porous rods of 4MgCO3·Mg(OH)2·3H2O are formed.