Abstract: Magnesium hydroxide is an important non-halogenated flame retardant. In order to improve its shortcomings such as low flame retardant efficiency and poor compatibility with polymer materials, it is usually necessary to use flame retardant additives to give it special treatment so that it has better flame retardant properties. The characteristics of magnesium hydroxide as a flame retardant and its flame retardant mechanism; the structural characteristics of silane coupling agent and the method and mechanism of modifying magnesium hydroxide; the factors affecting the modification and the evaluation method of modification effect are mainly introduced, and the research progress of the modification of magnesium hydroxide by silane coupling agent is summarized.
Keywords: silane coupling agent; magnesium hydroxide; surface modification; flame retardant
1,Introduction
How to improve the flame retardancy of synthetic polymers and natural polymer materials has become an urgent problem. Because inorganic hydroxide is easy to handle, does not produce toxic and corrosive gases during combustion, and has good smoke suppression effect, inorganic hydroxide flame retardants account for an increasing proportion of the sales of flame retardants, especially aluminum hydroxide and magnesium hydroxide, which are becoming more and more broad market.
Compared with aluminum hydroxide, magnesium hydroxide thermal decomposition temperature of 330 ℃, 100 ℃ higher than aluminum hydroxide, which makes the addition of magnesium hydroxide plastics can withstand higher processing temperatures, which is conducive to accelerate the speed of extrusion, shorten the molding time. At the same time, the decomposition energy of magnesium hydroxide (1. 37 kJ/mol) is higher than that of aluminum hydroxide (1. 17 kJ/mol), and the heat capacity is also 17% higher, which also helps to improve the efficiency of flame retardant. China is a big country of magnesium resources, combined with different resource conditions and market demand, the planning and development of magnesium hydroxide flame retardant has a bright future. Silane coupling agent is a kind of organosilicon compound with special structure, at the same time, it has reactive groups that can combine with inorganic materials (such as glass, cement, metal, etc.) and organic materials (such as synthetic resin, etc.). Therefore, the silane coupling agent can make two materials with great difference in properties connect together at the interface, in order to improve the performance of the composite material and increase the bonding strength, so as to obtain new composite materials with excellent performance and reliability. Silane coupling agent has become one of the indispensable auxiliaries in material industry. This paper mainly introduces the research progress of silane coupling agent modified magnesium hydroxide and its applications.
2 Magnesium hydroxide flame retardant and smoke reduction mechanism and properties
2.1 Flame retardant mechanism
Magnesium hydroxide dehydration reaction of heat absorption and degradation equation is as follows.
Mg(OH)2(s) →MgO(s) + H2O(g)
It is believed that the flame retardant mechanism of magnesium hydroxide mainly consists of the following aspects. 1) The polymer with magnesium hydroxide releases crystalline water and absorbs a large amount of latent heat (total amount of absorbed heat 44.8kJ/mol) during thermal decomposition, and the initial temperature of decomposition is 340℃, and it completely decomposes when it reaches 490℃, which can inhibit the temperature of the polymer from rising, reduce the actual temperature of the flame on the surface of the material, and decrease the burning speed, so that the polymer degrades to a flame retardant material. Burning speed, so that the polymer degradation into low molecular speed slowed down. 2) decomposition product MgO is a good refractory material, in the condensed phase to generate a stable oxide protective film, covering the surface of flame retardant materials, cutting off the supply of oxygen, blocking the transfer of heat to improve the polymer material resistance to the flame. 3) the decomposition process generates a large number of water vapor, which reduces the concentration of combustible materials in the gas phase combustion zone, so that surface combustion is more difficult to carry out. It is difficult to carry out combustion on the surface, which is conducive to the formation of surface carbonization layer, preventing the entry of oxygen and heat. 4) Water vapor is not involved in the reaction of increasing CO release. Figure 1 shows the oxygen index curve of adding different proportions of magnesium hydroxide polymer, which further confirms that magnesium hydroxide has good flame retardant effect.

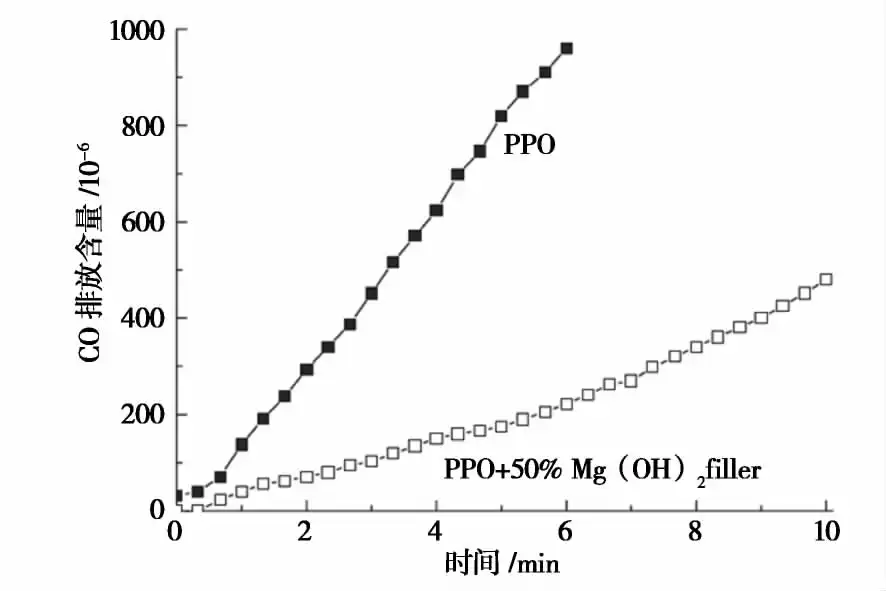
2.2 Smoke elimination mechanism
Compared with other two inorganic flame retardants calcium carbonate and aluminum hydroxide, the flame retardant effect of magnesium hydroxide mainly occurs in the solid degradation zone, reducing the generation of combustible materials and smoke generation, but the effect on the pre-combustion zone and combustion zone is very small, so the complete combustion of combustible materials is not much affected by it, so the smoke elimination effect of magnesium hydroxide is very obvious. Figure 2 shows the CO emission content curve of magnesium hydroxide doped polyphenylene ether (PPO) in the combustion process.
2.3 Properties of magnesium hydroxide
Magnesium hydroxide is a kind of green flame retardant, which has the following advantages.
1) It acts as flame retardant and filler at the same time, and has very good smoke suppression ability.
2)Magnesium hydroxide is a non-halogenated flame retardant.
3) Decomposition temperature is 110 ℃ ~ 140 ℃ higher than aluminum hydroxide, more suitable for high-temperature thermoplastic processing, to avoid the phenomenon of multi-foam and porous in the finished product.
4) It is non-toxic and odorless, and does not produce harmful gases.
5) It is non-volatile and not affected by water.
6)Raw materials are easy to obtain, mainly from natural minerals and bitter halide, low cost.
However, magnesium hydroxide as a flame retardant also has the following disadvantages.
1) low flame retardant efficiency, thus requiring a high amount of additive, in some polymer matrix of magnesium hydroxide flame retardant additives up to 60% or more, the mechanical properties of the material and the processing performance of the greater impact.
2) ordinary magnesium hydroxide is mostly hexagonal crystal or amorphous crystals, large specific surface area, easy to coalesce between the grains into a group, its surface hydrophilic and oleophobic, even if very dry magnesium hydroxide will adsorb a certain amount of water; resulting in poor dispersion in the polymer materials, difficult to be compatible with the material, need to be used as a flame retardant after a special treatment, so that it has a special structure and properties.
At present, the commonly used methods of powder surface modification include coating modification, surface chemical modification, precipitation reaction modification, encapsulation modification and mechanochemical modification. Among them, the modifiers commonly used for surface chemical modification include coupling agents, surfactants and organic silicon.
3 Structure and Modification Mechanism of Silane Coupling Agents
3.1 Structure of silane coupling agent
Silane coupling agent is a class of low molecular organosilicon compounds with special structure, its general formula is RSiX3, R on behalf of amino, mercapto, vinyl, epoxy, cyano and methyl propylene vinyl acryloyloyloxy and other groups, these groups and the different matrix resins have strong reactivity; X on behalf of hydrolyzable groups such as halogens, alkoxyl, acyloxy and so on. Therefore, the silane coupling agent can not only act with the hydroxyl group in the inorganic material, but also interact with the long molecular chain in the organic polymer, so that the two different properties of the material coupled together to improve the various properties of the matrix. Table 1 shows the commonly used silane coupling agents.
Table 1 Variety of silane coupling agent commonly used | ||
Product Name | Chemical Name | |
1 | A - 143 | γ – Chloropropyltrimethylsilane |
2 | A - 151 | Vinyltriethoxysilane |
3 | A - 171( Y - 4302) | Vinyltrimethoxysilane |
4 | A - 174( KH - 570) | γ-(Methacryloyloxy)propyltrimethoxysilane |
5 | A - 186 | β-( 3,4 Epoxycyclohexyl)ethyltrimethoxysilane |
6 | A - 187 | γ-Glycidyl Ether Propyl Trimethoxysilane |
7 | A - 189( KH - 590) | γ – Mercaptopropyltrimethoxysilane |
8 | A - 1100 | γ – Mercaptopropyltriethoxysilane |
9 | A - 1120 | N-β-(aminoethyl)aminopropyltrimethoxysilane |
10 | A - 1160 | γ-ureidopropyltriethoxysilane |
11 | KH - 560 | γ – ( 3,2 – epoxypropyl) methyltrimethoxysilane |
12 | KH - 580 | γ – Mercaptopropyltriethoxysilane |
13 | KH - 792 | γ-(Ethylenediamino)propyltrimethoxysilane |
14 | KH - 550 | γ-Aminopropyltriethoxysilane |
3.2 Modification mechanism of silane coupling agents acting on magnesium hydroxide
Arkles proposed a 4-step reaction model for the modification mechanism of silane coupling agent.
1) Hydrolysis of 3 Si-X groups linked to silicon to Si-OH;
2) Dehydration and condensation between Si-OH to oligosiloxanes containing Si-OH;
3) Hydrogen bonding between Si-OH in the oligomer and OH on the surface of the substrate.
4) Covalent bonding with the substrate by dehydration during heating and curing. It is generally accepted that at the interface, the silica of the silane coupling agent has only one bond with the surface of the substrate, leaving two Si-OHs, which are either condensed with Si-OHs in other silanes, or are free in the medium. The four-step reaction can be illustrated in Fig. 3.
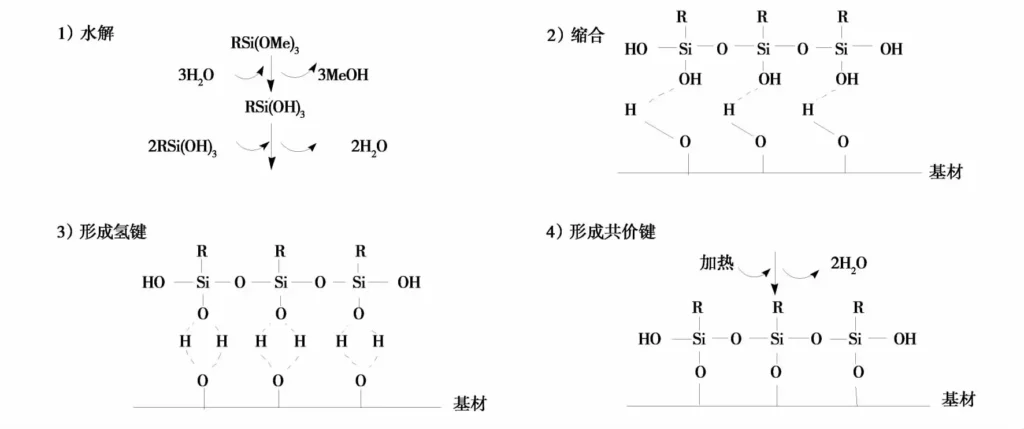
4 Modification method, evaluation of modification effect and factors affecting modification effect
4.1 Modification method
The surface modification of magnesium hydroxide using silane coupling agent is mainly divided into two methods: dry method and wet method. Among them, wet modification refers to adding well-dispersed silane coupling agent into a certain mass fraction of magnesium hydroxide slurry, and constantly stirring, and modification under a certain temperature. Dry modification refers to the modification of magnesium hydroxide and silane coupling agent by loading them into a high-speed mixer at a certain temperature according to a certain material ratio. Li Jin et al. used dry and wet methods for surface coating of magnesium hydroxide with different kinds of coupling agents, and found that the data obtained by the dry method were better than that of the wet method, and suggested that the dry method requires less equipment, simple process flow, easy to control the operation, and no pollution to the environment, while the wet method requires a large number of instruments and equipment, the process is complex, not easy to control, and may cause pressure on the environment due to the volatilization of solvents or the dissolution of modifiers. pressure due to solvent or modifier volatilization and dissolution.
In the modification process, the amount of silane coupling agent and coupling agent species and the specific surface area of the filler is related to the assumption of monomolecular layer adsorption, can be calculated according to the following formula.
Amount of silane coupling agent = mass of filler (g) × specific surface area of filler (m2/g)/Minimum coating area of silane coupling agent (m2/g)
The minimum covering area of silane coupling agent varies according to the variety of silane coupling agent, and the minimum covering areas of some silane coupling agents are shown in Table 2. In general, the actual dosage is less than the dosage calculated in the above formula. When it is not possible to determine the specific surface area of the powder or the minimum coating area of the silane coupling agent, the amount of silane coupling agent can be selected as 0.1% to 1.5% of the mass of the inorganic powder. Most silane coupling agents can be used for both wet and dry modification.
Table 2 Minimum covering area of several silane coupling agent | |||||||
varietal number | A - 151 | A - 172 | A - 174(KH570) | A - 186 | A - 189(KH590) | A - 187(KH560) | A - 1100(KH550) |
Minimum Wrap Area | 411 | 279 | 316 | 318 | 380 | 322 | 354 |
4.2 Measurement of modification effect
There are several methods to evaluate the modification of magnesium hydroxide by silane coupling agent as follows.
1) Measurement of activation index
For the surface modification aiming to improve the compatibility between inorganic filler and polymer base material or surface hydrophobicity, the index can be used to detect and characterize the effect of surface modification, the amount of surface modifier can be determined with reference to the activation index, but this can not be the only quality standard for powder surface modification products, it should be considered in combination with other indicators.
2) Determination of wetting contact angle
The larger the wetting contact angle of solid material in water, the better the hydrophobicity. If organic surface modifier carries out surface modification on inorganic filler, the more completely the modifier is coated on the surface, the larger the wetting contact angle of inorganic filler in water is, and the lower the surface energy of inorganic filler is.
3) Particle size distribution and particle morphology usually use SEM, TEM, laser particle size distribution meter and other equipment to observe the size distribution of the modified particle size, which can reflect the surface modification process of the particles whether the agglomeration occurred, but also can directly observe the surface of the powder surface coating the morphology of the coating layer, the evaluation of the effect of surface modification has a certain value.
4) Surface structure
Using XRD, by comparing the standard PDF card, we can detect whether the structure of the surface modified MgOH has changed, so as to check whether the surface modification process of silane coupling agent has destroyed the original structure of MgOH.
5) Coating amount
It refers to the mass of surface modifier adsorbed on the surface of a certain mass of powder, which can be quantitatively determined by infrared spectral analysis, chemical analysis and other methods. The infrared spectral analysis method can also observe the change of characteristic absorption peaks of magnesium hydroxide before and after modification, so as to determine the type of adsorption of magnesium hydroxide on silane coupling agent and adsorption effect.
4.3 Factors affecting the modification effect
The main factors affecting the surface modification include the type of silane coupling agent, the dosage of silane coupling agent, the modification temperature, the modification time and the stirring speed during the modification process, which can be generally determined by the evaluation results. However, the above evaluation methods can not be used as the only criterion for evaluating the modified products, and different influencing factors should be decided in combination with the effects of modified magnesium hydroxide on the properties of polymers.
5 Overview of the research and application of silane coupling agent modified magnesium hydroxide
After magnesium hydroxide is modified by some specific silane coupling agent, the surface of the powder changes from hydrophilic to hydrophobic, which makes the interface of the two materials with great differences in properties can be coupled, and its dispersion is also improved to improve the performance of the composite material and adhesive strength, and to reduce the effect of high filling degree of magnesium hydroxide on the mechanical properties of the material. Through the silane coupling agent modified magnesium hydroxide can be polypropylene (PP), ethylene vinyl acetate copolymer (EVA), polyethylene (PE) and other materials for composite, improve the flame retardant properties of these materials.
Since the reactivity of a silane coupling agent with organic polymers depends mainly on the hydrophobic end of the coupling agent, it is important to select a suitable silane coupling agent for different substrates or treatment objects. The selection is mainly based on pre-selection and experimentation, taking into account existing experience or regulations. The general principles for the selection of silane coupling agents are shown in Table 3.
Table 3 Silane coupling agent application | |
Type of silane coupling agent | Scope of application |
aminosilane | Acrylic Nylon Epoxy Resin Phenolic Resin Melamine PVC Polyurethane Nitrile Rubber |
Methacryloxysilane | Unsaturated Polyester Acrylic EVA Polyolefin |
Epoxysilane | Epoxy Resin PBT Polyurethane Acrylic Polysulfide |
Vinylsilane | Grafted PE with EPDM rubber, SBR, polyolefin moisture crosslinking |
Phenylsilane | Improved hydrophobicity and dispersion of mineral-bound silanes |
Chloroalkylsilane | Polyurethane Epoxy Resin Nylon Phenolic Resin Polyolefin |
Ye Hong et al. used different silane coupling agent to dry surface modification of magnesium hydroxide, and the modified magnesium hydroxide and EVA for mixing, through the determination of the oxygen index and mechanical properties of the composite materials, compared the different modifiers, modification time, temperature and other factors on the performance of the material.
The results show that the magnesium hydroxide modified with 2% modifier and 0.5 h at 100 ℃ has the best modification effect, which can improve its dispersion and compatibility in EVA system to a certain extent, thus improving the flame retardant property of the composite material, and at the same time, reducing the adverse effect on the mechanical properties of the composite material.
Chen et al. used silane coupling agent (2,3-epoxypropoxypropyltrimethoxysilane) for dry modification of magnesium hydroxide with 2% of modifier, and blended the modified magnesium hydroxide with polypropylene (PP) in a 1:1 blend, to investigate the crystallization and melting behaviors, the crystal structure, and the processability (dynamic rheological properties) and flame retardancy of the composites, mechanical properties.
The experimental results showed that the silane coupling agent-treated magnesium hydroxide inhibited the heterogeneous nucleation of polypropylene and improved the processability of polypropylene, and the oxygen index of the silane coupling agent-modified composites was significantly higher than that of the silicone oil-modified composites with the same amount of modifier.
Wang et al. used 3% silane coupling agent (vinyltriethoxysilane) to modify the surface of magnesium hydroxide with 3% of the mass of magnesium hydroxide, and filled the modified magnesium hydroxide into linear low-density polyethylene (LLDPE) composites according to the filler amount of MH:LLDPE = 1.5∶1. It was found that the LLDPE composites with modified magnesium hydroxide had a significantly higher oxygen index than those with modified MH∶LLDPE = 1.5∶1, compared with those with pure LLDPE. It was found that compared with pure LLDPE, the thermal stability of LLDPE modified with magnesium hydroxide was significantly improved, while the limiting oxygen index (LOI) value of the composite material was increased, and its flame retardant and smoke suppressant ability was also strengthened.
Huang Honghai et al. added silane coupling agent-modified magnesium hydroxide powder to EVA, and the experimental results showed that the dispersion of magnesium hydroxide in the matrix was improved due to the modification with silane coupling agent, and the flame retardancy of the composites was improved to a certain extent.
Liu Zhifeng et al. added modified magnesium hydroxide to polystyrene (HIPS) using silane coupling agent (KH550) as a surface modifier, the oxygen index and flame retardant properties of the material were improved, and the impact strength of HIPS could be improved by using silane coupling agent treated magnesium hydroxide.
Sener et al. added silane coupling agent (vinyltrimethoxysilane) modified magnesium hydroxide into a commonly used cable material low density polyethylene (LDPE), the test results show that, in the modified magnesium hydroxide filler degree of 57% or so, the LDPE has a better flame retardant and smoke suppression properties, the use of this composite material made of cables at high temperatures have sufficient impact resistance, with the ability of continuous operation for a long time. The cables made of this composite material have sufficient impact resistance at high temperature and have the ability to work continuously for a long time.
Li Sanxi et al. dry modified magnesium hydroxide with silane coupling agent, the amount of modifier is 0.5% of the mass of magnesium hydroxide, the modified magnesium hydroxide filled with high-density polyethylene (HDPE) and then tested the performance of the composite material. Compared with the pure polyethylene material, the modified MH /HDPE system with 35% mass fraction has good thermal stability, and the modified MH /HDPE system has better compatibility with the HDPE matrix than the unmodified MH.
6, Conclusion
As the application of polymer materials becomes more and more extensive, the flame retardant performance of flame retardant materials has put forward higher requirements, the inorganic flame retardant magnesium hydroxide has gradually been emphasized due to its multiple flame retardant effects, as well as low smoke and non-toxicity, etc. However, high filler content leads to a reduction in the processing and mechanical properties of the composite material, which becomes the biggest obstacle to the application of flame retardant grade magnesium hydroxide.
Through the study of different influencing factors such as material formulation, modification time and modification temperature, the use of different silane coupling agent modified magnesium hydroxide and polymer materials composite can achieve the ideal flame retardant effect, but also make the composite material processing performance, mechanical properties of the loss of relatively reduced.