Abstract: Magnesium hydroxide-based flame retardant, as an important inorganic flame retardant material, has received extensive attention in the research of flame retardant materials due to its halogen-free, non-toxic and green environmental protection properties. However, its performance is greatly affected by its strong surface polarity, poor compatibility with polymers and difficulty in uniform dispersion. The performance of magnesium hydroxide-based flame retardant can be effectively improved by ultrafine particles and surface modification. This paper mainly introduces the relevant progress of ultrafine particles and surface modification of magnesium hydroxide. Combined with the development trend of flame retardant materials, the research direction and development of magnesium hydroxide-based flame retardant in the future are prospected.
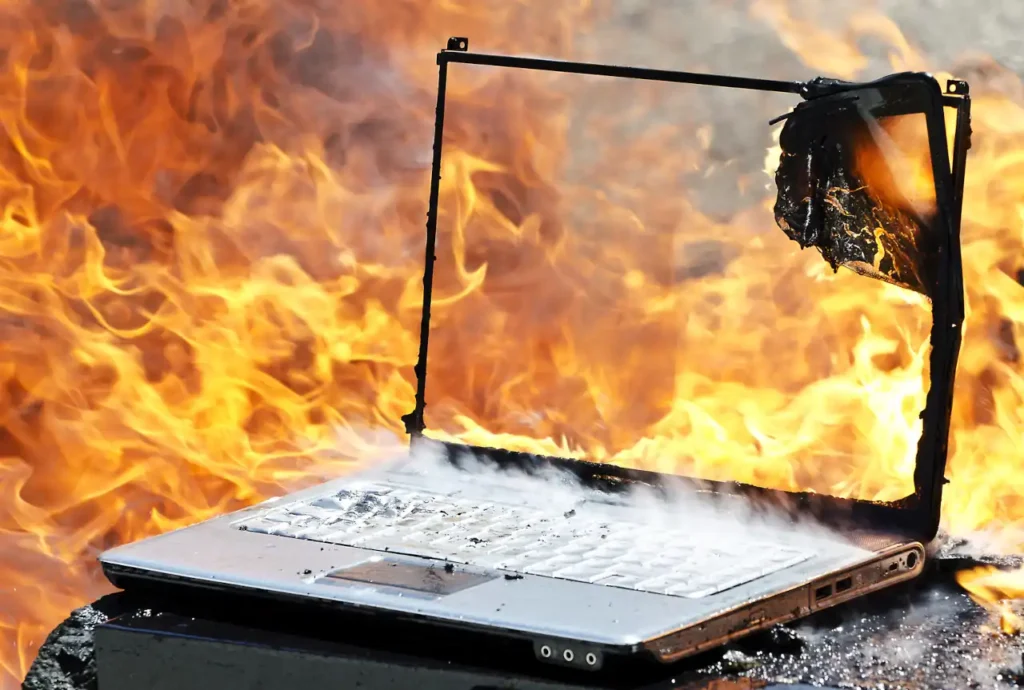
Fires bring not only astonishing economic losses to daily production and life, but also shocking casualties. While the strictness of fire safety standards is increasing, the use of effective flame retardants to reduce fires is also becoming one of the important strategic measures. Against this background, the application and sales of flame retardants around the world have been in a stage of rapid growth. Among the existing flame retardants, halogen-based flame retardants have been widely used due to their advantages such as good flame retardant effect, little effect on the physical and chemical properties of materials, and low production cost. However, during the flame retardant process, the smoke and toxic gases (dibenzofuran and dibenzodioxin) released by thermal decomposition seriously endanger human health and bring huge environmental problems. Therefore, the halogen-free process of flame retardants is accelerating. Flame retardants based on inorganic hydroxides have gained wide attention in the flame retardant material market due to their high efficiency in smoke suppression, green and non-toxicity, and no secondary hazards.
Inorganic hydroxide flame retardants are additive flame retardants and are mostly used for flame retardant of thermoplastic polymers. Its flame retardant mechanism is summarized as follows:
(1) As a filler, it can reduce the flammability of polymers;
(2) It has a large heat capacity and can effectively delay the decomposition of the matrix;
(3) It absorbs heat by decomposition and can effectively dilute oxygen;
(4) The decomposition products can effectively isolate the air and inhibit further combustion.
In the early market, cheap aluminum hydroxide was the main material. However, subsequent studies have shown that compared with aluminum hydroxide, magnesium hydroxide has a higher decomposition temperature, a softer texture, and a smaller particle size, which is more suitable for polymer processing requirements. In addition, during the flame retardant process, the polymer carbonized layer and low combustion smoke formed by magnesium hydroxide can effectively inhibit combustion; the decomposition product magnesium oxide is also a high-temperature resistant material, which can greatly improve the efficiency of air isolation when covered on the polymer surface, and further prevent combustion; the raw materials are abundant and easy to obtain, and can be mass-produced, with the advantage of strong market competitiveness. It can be foreseen that inorganic flame retardants based on magnesium hydroxide have broad market application prospects.
However, there are still many problems in the use of magnesium hydroxide as a flame retardant. These include: the crystal surface has a strong surface polarity due to the positive charge; good hydrophilicity, but poor affinity with lipophilic polymer molecules; the crystals are prone to secondary agglomeration, resulting in poor dispersion; when the addition amount is high (mass fraction> 40%), the mechanical properties of polymer composites will be significantly reduced. Only by effectively treating the surface of magnesium hydroxide can the problems in its application process be overcome (referring to its wide application in the field of high-end flame retardants) and the common requirements of multiple fields such as materials, fire protection, and environmental protection be met.
In recent years, with the global attention paid to environmental protection issues, many companies and research groups at home and abroad have conducted extensive research on improving the performance of magnesium hydroxide-based flame retardants, mainly from the two aspects of particle ultrafineness and surface modification, which greatly improved the matrix compatibility of magnesium hydroxide and further expanded the application range of magnesium hydroxide-based flame retardants.
This paper mainly introduces the research progress of surface modification technology of magnesium hydroxide-based flame retardants. Combined with the current research status in China, it points out the main problems in magnesium hydroxide-based flame retardant modification technology in my country, as a country with a large reserve of magnesium salts, and expounds the future development direction of magnesium hydroxide-based flame retardant modification research.
1 Performance improvement method of magnesium hydroxide-based flame retardant
Magnesium hydroxide can be used as a flame retardant material for polymer materials such as polyester, polypropylene, polyvinyl chloride, polypropylene, polyvinyl acetate, epoxy resin and unsaturated resin. Therefore, it has broad application prospects in flame retardancy and smoke suppression in the fields of wires, cables, wood, rubber, paint, coatings and fiber products [8]. According to the requirements of the flame retardant mechanism of magnesium hydroxide, it is necessary to treat the magnesium hydroxide to improve the performance of magnesium hydroxide-based flame retardants. It mainly includes: ultrafine particles and surface modification. Among them, ultrafine magnesium hydroxide can effectively reduce the influence of high filling amount on the mechanical properties of materials; while surface modification can effectively improve the activity of magnesium hydroxide, thereby improving the interfacial adhesion and compatibility between fillers and substrates.
1.1 Ultrafine particles
The size of existing magnesium hydroxide flame retardants is mostly concentrated in the micron level, with low flame retardancy, and requires extremely high filling rate to obtain good flame retardant properties. In addition to wasting raw materials, high filling rate will also greatly affect the mechanical properties of materials. Ultrafine magnesium hydroxide can improve the interfacial adhesion and compatibility between fillers and substrates, thereby reducing the influence of fillers on the mechanical properties of polymer matrix materials. Qiu et al. prepared nano-magnesium hydroxide and studied the effect of magnesium hydroxide particle size on the flame retardant effect of EVA (ethylene-vinyl acetate copolymer). The results showed that the oxygen index of the composite material of nano-magnesium hydroxide and EVA (mass ratio of 1:1) reached 38.3, while the oxygen index of the composite material of micron-magnesium hydroxide and EVA was only 24 at the same filling ratio, which effectively proved the effect of ultrafine particles on improving the performance of magnesium hydroxide flame retardant.
There are many reports on the preparation of nano-magnesium hydroxide. Using magnesium chloride and ammonia water as raw materials, Wu Shijun et al. used the direct precipitation method (adding a precipitant to a solution containing Mg2+), and Yi Qiushi used the reverse precipitation method (adding Mg2+ to a precipitant) to obtain nano-magnesium hydroxide. The precipitation method is simple and has low requirements for equipment and technology, but the prepared nano-magnesium hydroxide has problems such as wide product particle size distribution, easy agglomeration, and poor repeatability in batch production. Song Yunhua et al. used the ultra-gravity method to use refined magnesium chloride solution and industrial ammonia water/gas as raw materials, or magnesium sulfate solution and industrial ammonia/gas as raw materials, and mixed the reactants evenly in an instant under a rotating filling environment, so that the products nucleated and grew simultaneously, which can effectively improve the uniformity and purity of nano-magnesium hydroxide particles. Wu et al. used magnesium chloride and ammonia as raw materials, and adopted a simple oil-in-water microemulsion method to blow ammonia into the magnesium chloride microemulsion area to obtain magnesium hydroxide nanosheets with uniform particles. However, the above methods can only achieve small-scale preparation in the laboratory, which is far from large-scale industrial production.
1.2 Surface modification technology
Because magnesium hydroxide itself has strong hydrophilicity and polarity, it is more difficult to disperse it evenly in most polymer matrices (mostly non-polar), and its adhesion to the matrix is poor. Therefore, it is particularly important to carry out necessary surface modification of magnesium hydroxide to improve the interfacial adhesion and compatibility between the filler and the matrix to improve the performance of magnesium hydroxide-based flame retardants. According to different surface modification principles, it can be divided into surface chemical modification and surface physical modification.
1.2.1 Surface chemical modification and mechanism
Surface chemical modification is to make magnesium hydroxide have a “hydrophobic and lipophilic” surface property through surface chemical reaction or adsorption of surfactants, coupling agents, unsaturated organic acids and other substances with amphoteric groups, which effectively alleviates its water absorption and agglomeration phenomenon and enhances the dispersibility of magnesium hydroxide in the matrix material.
Due to the wide variety of chemical modifiers, there is a large space for selection, and they can be selected according to the specific polymer material. The surfactants used for magnesium hydroxide surface modification are mostly anionic surfactants. Because the surface of magnesium hydroxide is mostly positively charged and has a high potential, negatively charged anionic surfactants such as stearic acid, oleic acid and other salts can be used to change its interfacial properties. The hydrophilic end of the magnesium hydroxide is adsorbed on the surface of the powder, and the hydrophobic end is adsorbed on the matrix material, thereby enhancing the bonding ability of magnesium hydroxide with the matrix, improving its compatibility and dispersibility in the matrix material, and thus improving the mechanical properties and processing rheological properties of the composite material. Li et al. used oleic acid as a surfactant, and obtained good dry and wet modification technology by improving the process conditions, and obtained good flame retardant properties in EVA composite materials.
The coupling agents used for modification are mainly silane coupling agents, titanates and aluminates. Part of the activated groups in the molecules can be adsorbed with the hydroxyl groups on the surface of nano magnesium hydroxide powder; while the other part of the hydrophobic groups can react chemically with the polymer matrix and form physical entanglement, thereby playing a “bridge” role and tightly connecting the two materials with large polarity differences. Chen and Ma et al. studied the modification effect of vinyl trimethoxysilane on magnesium hydroxide, respectively, and confirmed that it can improve the strength of the composite. Du Gaoxiang et al. studied the modification of ultrafine magnesium hydroxide by two titanates (JN-201 and JN-101) and H-containing silicone oil. The results showed that JN-101 can effectively improve the dispersibility of magnesium hydroxide powder in a dry state due to chemical adsorption reaction. Liu Lihua et al. studied the modification effect of sodium stearate as a surface modifier on nano magnesium hydroxide powder, and confirmed that it has a significant improvement effect on the flame retardant and tensile properties of soft PVC system composite materials.
1.2.2 Surface physical modification and mechanism
Surface physical modification can be divided into high-energy surface modification and surface coating modification. High-energy surface modification mainly uses electromagnetic wave radiation or plasma modification to modify the particle surface. The principle is that it does not produce chemical reactions. It mainly changes the surface activity of magnesium hydroxide through radiation and other methods, generates relevant active sites on the particle surface or generates gas free radicals, thereby initiating the grafting of the matrix on the particle surface. Surface coating modification is to modify magnesium hydroxide particles using a dispersant that does not react chemically with them to improve their flame retardant properties.
Li et al. [24] used gamma rays generated by cobalt-60 to irradiate and crosslink a mixture of magnesium hydroxide/EVA in the presence of triacyltrimethylolpropane, and then tested its properties. It was found that as the cobalt-60 radiation dose increased, the degree of crosslinking of the magnesium hydroxide/EVA mixture gradually increased, and the tensile strength and flame retardant properties also increased significantly. Shafiq et al. used gamma ray radiation to improve the thermal mechanical properties of magnesium hydroxide/sepiolite/linear low-density polyethylene composites. The results showed that at a dose not exceeding 150 kGy, the elastic modulus of the composite material was significantly improved, and the strength of the hydroxyl group on the surface of magnesium hydroxide decreased with the increase of the absorbed dose, and eventually the hydroxyl functional group was gradually lost. Liu et al. irradiated a high-energy electron radiation on a high-density polyethylene/magnesium hydroxide/EVA composite in the presence of triallyl isocyanurate (a radiation sensitizer) and studied its flame retardant properties. The results show that the formation of a cross-linked network structure improves the thermal stability and mechanical properties of the composite material and greatly improves the smoke suppression effect.
In the study of surface coating modification, Yang Xuyu et al. systematically studied the modification of magnesium hydroxide nanopowders by five kinds of superdispersants. The results show that when the amount of superdispersant is 4% of the powder mass, the modification effect is the best, and the magnesium hydroxide modified by the superdispersant terminal carboxyl liquid nitrile (CTBN) has good dispersion in polyolefin resin, and the oxygen index, tensile strength and elongation at break of the flame retardant system all reach the maximum value; Zhang et al. introduced ultrasonic-assisted coating modification and obtained magnesium hydroxide powder with good compatibility and dispersibility in the organic phase, which effectively shortened the surface modification treatment time.
2 Development trend of magnesium hydroxide-based flame retardants
Particle ultrafineness and surface modification have an important influence on the improvement of the performance of magnesium hydroxide-based flame retardants. However, with the further enrichment of base materials and the continuous improvement of market requirements for flame retardant performance, relying solely on a single modification method or process can no longer meet the development requirements of magnesium hydroxide-based flame retardant materials. Combined with the problems in the development process of magnesium hydroxide-based flame retardant materials, the future research directions of magnesium hydroxide-based flame retardants will focus on the following aspects.
2.1 Morphology control in ultrafineness
The research results show that flaky or fibrous (needle-shaped) magnesium hydroxide particles have a significant effect on the mechanical properties of organic materials, especially on the improvement of material torsional strength and elongation. However, how to effectively control the particle size of magnesium hydroxide while achieving effective morphology control is one of the important directions for future research on magnesium hydroxide-based flame retardant materials.
2.2 Composite modifiers and comprehensive modification technology
In previous magnesium hydroxide modification studies, most of the performance of magnesium hydroxide-based flame retardants was studied with a single modifier or modification process. However, the relatively single modification mechanism and environment make the modification research results less consider the impact of comprehensive factors in the actual production process. Therefore, developing composite modifiers based on multiple modification principles and effectively combining different modification processes are important research contents for improving the performance of magnesium hydroxide-based flame retardants.
2.3 Synergistic flame retardancy
Magnesium hydroxide-based flame retardants have excellent performance, but according to the flame retardant mechanism of different stages of polymer combustion, different flame retardant performance is required in each stage. Using the advantages of magnesium hydroxide-based flame retardants and other flame retardants for synergistic flame retardancy is of great significance to improving the flame retardant effect, reducing the amount and cost of flame retardants, and further expanding the application range of flame retardants. It is particularly important for industrial production and is a research hotspot for magnesium hydroxide-based flame retardants.
3 Results and Prospects
Magnesium hydroxide-based flame retardants have irreplaceable advantages, and their flame retardant properties are comprehensively affected by factors such as particle size, morphology, and surface properties. In recent years, the research on ultrafine particles and surface modification has continued to increase, the performance of magnesium hydroxide-based flame retardants has been significantly improved, and the scope of application has continued to expand. However, it should be noted that domestic related technologies still need to develop rapidly, especially the improvement of the preparation and modification technology of nano-magnesium hydroxide flame retardant materials, which is of great significance for my country to transform from a major exporter of magnesium salt raw materials to a strong exporter of magnesium hydroxide-based high-end flame retardants.