As an effective precipitant, active magnesium oxide shows a broad application prospect in the field of hydrometallurgy, especially in the metal precipitation process of copper-cobalt ore and laterite nickel ore. With technological progress, cost reduction and improvement of supply capacity, active magnesium oxide is expected to realize larger-scale application in the next few years and may be substituted in specific fields, thus promoting the development of related enterprises and the technological progress of the whole industry.
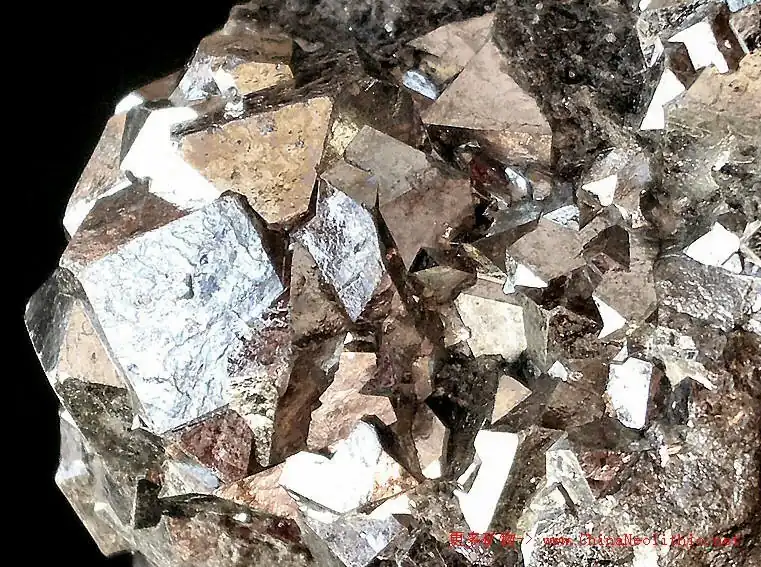
The wet metallurgical treatment process of nickel and cobalt-bearing laterite ore is relatively long, which includes a series of processes such as leaching, decontamination, precipitation, dissolution, extraction (decontamination and separation of nickel and cobalt) and electrowinning. After wet leaching of laterite ore, a solution of sulfate system containing 3~6g/L nickel and <1g/L cobalt was obtained. Along with the leaching of valuable metals, iron, aluminum, manganese, magnesium pen metal elements in laterite ore also enter into the above leaching solution system in the form of ions, which requires the separation of these impurity ions from nickel and cobalt ions.
The traditional method of removing impurities a precipitation nickel cobalt process, the method first in the lower pH value of the conditions for the removal of iron (iron alum method, iron ore method, neutralization and precipitation method, etc.), in addition to the removal of iron after the liquid to adjust up the pH for the depth of purification in addition to the iron and aluminum and other impurities, in addition to the removal of impurities after the liquid precipitant nickel cobalt precipitation nickel cobalt intermediate products, and ultimately will be controlled in the magnesium precipitation of magnesium before the separation of magnesium and nickel cobalt products. This method is simple and practical process, low cost, at present the industry basically apply this method.
Nickel and cobalt precipitant has a variety of: caustic soda, soda ash, magnesium hydroxide, magnesium oxide, sulfide, milk of lime, the actual industrial production can be based on the project process requirements, the local precipitant type, price, transportation conditions and so on to choose.
In nickel and cobalt hydrometallurgical process, magnesium oxide (MgO) has various applications:
I. Neutralizer
Adjustment of pH value
After the acid leaching process of nickel and cobalt ore, the leaching solution is usually acidic. For example, when leaching nickel and cobalt ores with sulfuric acid, a large number of hydrogen ions will be produced, making the pH value of the leaching solution low. Magnesium oxide is a basic oxide, which can undergo a neutralization reaction with acid. The reaction equation is MgO+2H+=Mg2++H2O.
By adding magnesium oxide, the pH value of the leaching solution can be adjusted to a suitable range. Generally, specific pH conditions are required when precipitating certain impurity metal ions or precipitating nickel and cobalt hydroxides.
When precipitating impurities such as iron, aluminum, etc., the pH is usually adjusted to about 4 – 5. The amount of magnesium oxide to be added can be precisely calculated based on the acidity of the leach solution and the target pH. This precise pH adjustment helps to selectively precipitate impurities without affecting the presence of valuable metals such as nickel and cobalt, thus achieving initial purification.
Controlling the precipitation process
Proper pH control is especially important when precipitating nickel and cobalt hydroxides. For nickel hydroxide precipitation, the pH value generally needs to be adjusted to about 7 – 8, and the pH conditions for cobalt hydroxide precipitation are similar. Magnesium oxide slowly neutralizes the acid in the solution, so that the pH value is gradually increased, which can avoid the local high pH leading to the rapid precipitation of nickel and cobalt and the inclusion of impurities. It can make the precipitation process more uniform, stable, and conducive to the generation of higher purity of nickel and cobalt hydroxide precipitation.
II. Precipitant
Precipitation of magnesium ion itself
In some nickel and cobalt hydrometallurgical processes, the raw material ore itself contains magnesium. After acid leaching and other processes, magnesium exists in solution in ionic form (Mg2+). As the process proceeds, especially in later processes such as refining of nickel and cobalt, the magnesium ions need to be removed. The magnesium ions can be precipitated by adding excess precipitant. Since magnesium oxide will generate magnesium hydroxide precipitate (MgO+H2O=Mg(OH)2↓) when added to the solution, by controlling the reaction conditions, such as temperature, pH, etc., the magnesium ions can be almost completely precipitated, thus reducing the influence of magnesium on the purity of the subsequent nickel and cobalt products.
Co-precipitation of impurities
Magnesium oxide can also form co-precipitation with some impurity ions. For example, in the precipitation process, it can adsorb some trace heavy metal impurity ions, such as lead, cadmium, etc., together with precipitation into the slag. This is because the magnesium hydroxide precipitation has a large specific surface area, can adsorb some impurity ions with opposite charge, so as to play a certain degree of depth purification of the solution, is conducive to improving the quality of nickel and cobalt products.
III. As an additive to improve the nature of the precipitate
Improve the nature of precipitation particles
After adding magnesium oxide, in the process of precipitating nickel and cobalt hydroxide, it can change the size and morphology of precipitated particles. The presence of magnesium hydroxide precipitate can act as a crystal seed or template, inducing the nickel-cobalt hydroxide precipitate to grow in a particle morphology more favorable for filtration and washing. For example, it can cause the particles of the nickel-cobalt hydroxide precipitate to become coarser, which can increase the filtration rate, reduce the filtration time, and lower the production cost during subsequent filtration.
Improvement of precipitate stability
After mixing magnesium oxide and nickel-cobalt hydroxide precipitate, it can improve the thermal stability and other properties of the precipitate. In the subsequent drying, calcination and other processing, this mixed precipitate can better maintain its chemical composition and physical structure, which is conducive to the preparation of high-quality nickel-cobalt oxides and other end products. For example, in the preparation of nickel-cobalt oxides for use as battery materials, a stable precipitate structure ensures the stability of the product’s performance during the battery charging and discharging process.