A method for preparing industrial-grade basic magnesium carbonate for battery materials from salt lake brine, comprising the steps of conversion coupling, solid-liquid separation, slurry washing, dehydration, drying and packaging. First, the tail liquid of lithium carbonate electrodialysis separation and the tail liquid of lithium carbonate conversion are mixed to carry out continuous conversion reaction; then the mixed liquid after the reaction is filtered to obtain a solid-phase basic magnesium carbonate filter cake, and the liquid phase is an external lithium-containing waste liquid; the basic magnesium carbonate filter cake is subjected to multiple filter pressing dehydration and washing and grinding; the basic magnesium carbonate filter cake after washing is dehydrated to obtain a basic magnesium carbonate crude product; the basic magnesium carbonate crude product is dried and crushed, and then sealed and packaged.
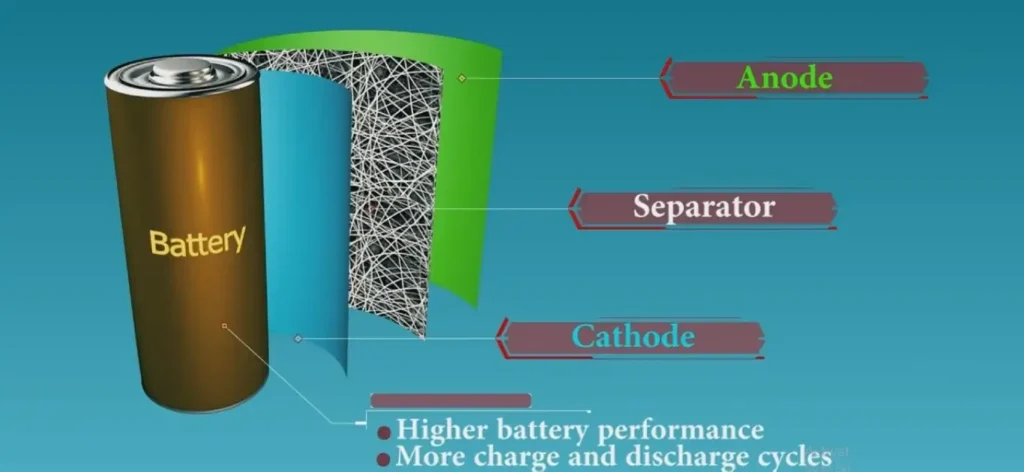
Basic magnesium carbonate can be used for battery materials, which has the advantage of improving the performance of lithium batteries; in addition, this preparation method has the advantages of simple process, low production cost, high output of basic magnesium carbonate produced, and good quality.
Hebei Meishen Technology Co., Ltd. uses magnesium carbonate for battery materials, and has the following requirements in the lithium battery industry:
First, the main content of magnesium ions should be controlled to be stable. The main content of magnesium carbonate is controlled at 40% to 42%. The stability of the main content during production is conducive to the accurate addition of other materials. At present, for the production process and production technology level of domestic magnesium carbonate manufacturers, it is difficult to control the lower limit of the magnesium ion content of magnesium carbonate. If the product is not dried and the moisture content exceeds the standard, it will directly affect the problem of unstable magnesium ion content. If the impurity control is unstable, it will also have an adverse effect.
Secondly, the magnetic impurities should be controlled in a lower range. Magnetic impurities will affect the performance of the battery. It is necessary to control the magnetic impurities to less than 500 to be more stable. The detection method of magnetic impurities is the core technology in China, and only a few manufacturers can detect it. The core of the magnesium carbonate impurity removal process is the removal of magnetic impurities.
To control the particle size span, a large span should not occur. Magnesium carbonate is generally detected by a laser particle size analyzer in China. Its particle size D50 is about 2 microns and D90 is about 20 microns. The fineness is not the finer the better. The ideal state is that the particle size is similar to that of other materials when added in production, and they are all within the same span, which is more conducive to production.