I. Flame Retardant Mechanism of Magnesium Hydroxide
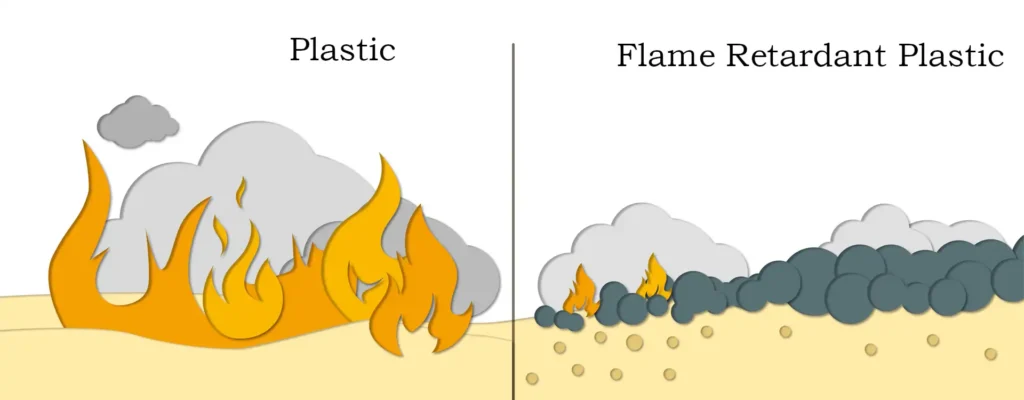
Magnesium hydroxide, often used as an inorganic flame-retardant filler, belongs to a class of polymer composite materials with vast application prospects. When magnesium hydroxide is used as a flame retardant, it releases water molecules upon heating, absorbing heat and thereby reducing the flame temperature on the surface of the polymer material to some extent. This process slows down the rate at which the polymer degrades into low molecular weight substances. Additionally, the released water vapor dilutes the oxygen concentration on the material’s surface, inhibiting combustion. Therefore, magnesium hydroxide not only possesses excellent properties such as low smoke and non-toxicity, but the magnesium oxide produced after its decomposition also has stable chemical properties and does not cause secondary pollution.
II. Why Modify Magnesium Hydroxide?
It is important to note that compared to halogenated flame retardants, achieving the same flame-retardant effect with magnesium hydroxide typically requires a filler loading of over 50%. This is because magnesium hydroxide, being an inorganic compound, has poor surface compatibility with polymer matrices. Moreover, such a high filler loading in polymer materials can negatively impact the mechanical properties of the resulting composite.
Therefore, the Tengmei R&D team conducts surface modification treatment on magnesium hydroxide products to effectively improve the dispersibility of its powder and its compatibility with polymer matrices. This process also enhances the surface activity of the particles to a certain extent, ensuring that the mechanical properties of the filled material do not decrease and may even improve in some cases.
III. Modification Methods for Magnesium Hydroxide Products
Magnesium hydroxide is typically modified using surface modification methods, mainly including dry and wet methods. Generally, the dry method is employed for treatment. The dry modification process involves adding dry magnesium hydroxide to an appropriate amount of inert solvent. Then, a coupling agent diluted with an appropriate amount of inert solvent is sprayed onto the magnesium hydroxide powder. The mixture is then stirred and mixed in a low-speed kneader for modification treatment. Wet surface treatment involves directly adding a surface treatment agent or dispersant to a suspension of the inorganic flame retardant to perform surface treatment.
Alternatively, a refinement method can be used to pulverize the magnesium hydroxide powder, reducing the particle size as much as possible to the nanometer scale. This increases the contact area between the flame retardant and the polymer matrix, enhances the affinity between magnesium hydroxide and the polymer, and improves their compatibility. The goal is to reduce the amount of flame retardant needed while increasing its efficiency.