Although magnesium hydroxide is mainly used as a halogen-free flame retardant, it also has many potential positive effects on the anti-corrosion performance of polyurea coatings.
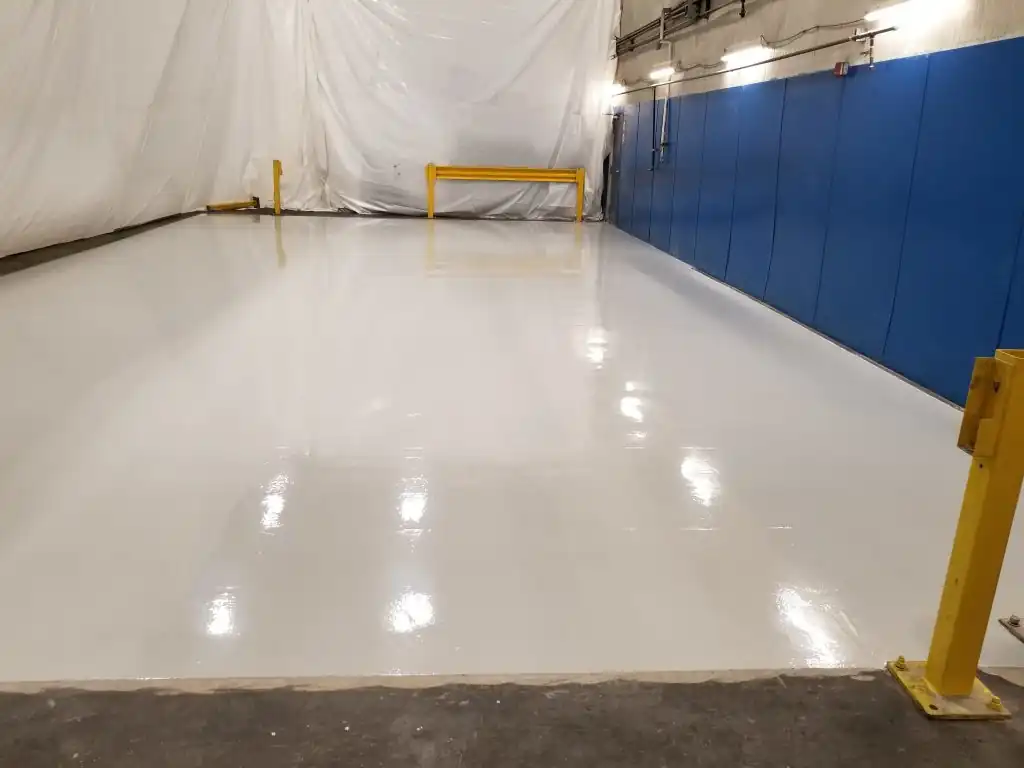
1. pH buffering effect – inhibiting acidic corrosion
Magnesium hydroxide is a weakly alkaline material. After dissolution, it can increase the local pH value and inhibit the corrosion of metals in acidic environments.
Especially in environments such as acid rain, high humidity, and high salt fog, it can slow down metal oxidation reactions.
Application scenarios: acidic corrosion environments such as bridge steel structures, chemical plant floors, and tank outer walls.
2. Adsorbed ions – inhibiting the migration of corrosive ions such as Cl⁻
Magnesium hydroxide has a certain cation exchange capacity and has an adsorption effect on corrosive anions such as Cl⁻ and SO₄²⁻.
Reducing the penetration rate of these ions helps protect the metal substrate.
It is equivalent to forming a “chemical barrier”.
3. Filling microporous structure – improving shielding performance
The addition of magnesium hydroxide can fill the microscopic gaps and defects in the polyurea system, reducing the permeation channels of water vapor, oxygen and ions.
Enhance the compactness and barrier properties of the coating.
The effect is more significant when spraying polyurea on porous substrates (such as concrete).
4. Assisting the formation of alkaline corrosion inhibition layer
In some compound systems (such as composite with zinc powder, zinc phosphate, and graphene), magnesium hydroxide can react with the corrosive medium to form alkaline corrosion inhibition deposits, such as MgCO₃.
Such products can “self-heal” at microcracks or scratches to prevent further corrosion.
5. Synergistically enhance the anti-corrosion filler system
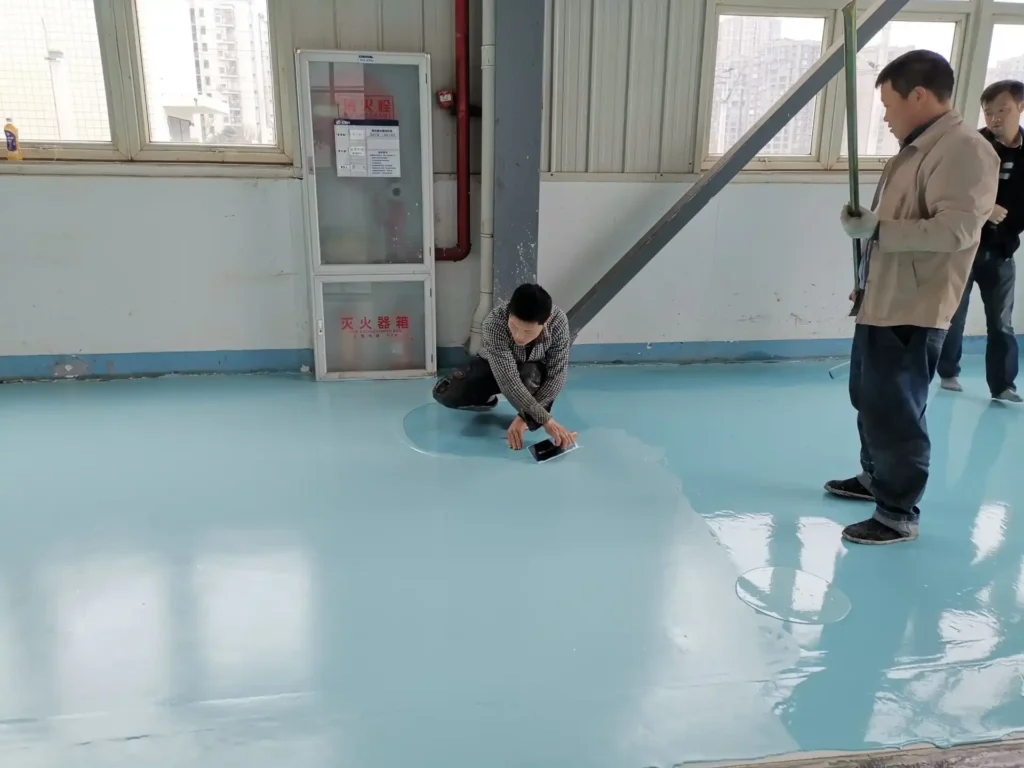
Good synergistic effect with other functional fillers:
Combined with zinc powder: Enhance the sacrificial anode protection effect and control its release rate
Synergize with silicates and phosphates: Form a more stable composite passivation layer
With flake mica and graphite: Improve the “maze effect” of the shielding layer