Magnesium Oxide for Silica Removal: Applications and Advantages Across Industries
Magnesium oxide (MgO) silica removal technology, with its advantages of high efficiency, simplicity, and controllability, is widely applied in various industrial and environmental fields. The following outlines its practical uses and technical advantages in several key industries:
I. Water Treatment and Ultrapure Water Production
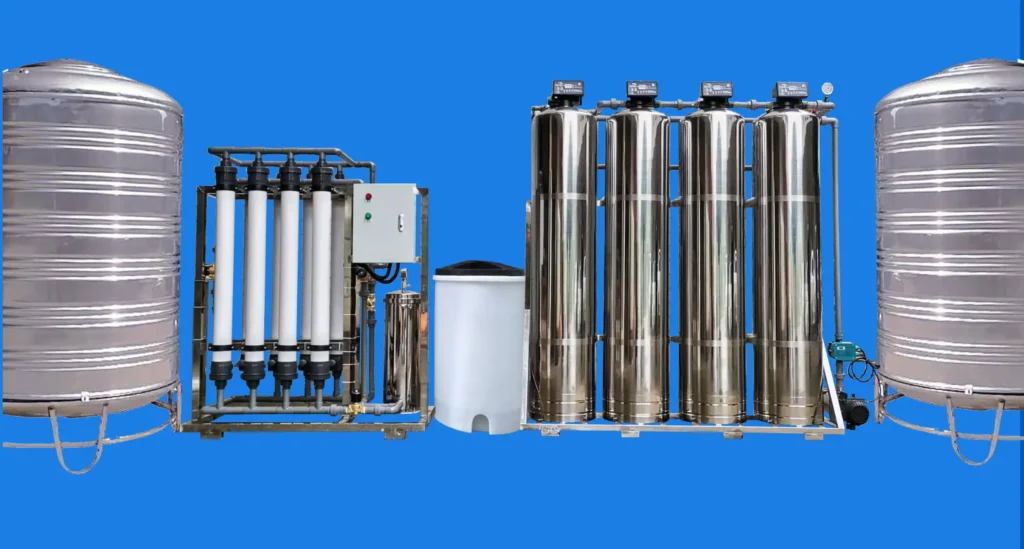
Application Background:
Soluble silicon (Si) is a common difficult-to-remove impurity in industrial circulating water, boiler feedwater, and electronic-grade ultrapure water, easily forming scale or interfering with resistivity control.
Role of Magnesium Oxide:
Magnesium oxide slowly hydrolyzes in water to form magnesium hydroxide, which reacts with silicate ions to produce magnesium silicate precipitate.
It can simultaneously remove both colloidal and dissolved silica.
Advantages:
- Compared to traditional aluminum and iron salts, it does not introduce excessive metal ion pollution.
- The precipitate is easy to filter, and the residue is easy to handle.
- It can be used as pretreatment for membrane systems such as ultrafiltration and nanofiltration to prevent membrane fouling.
II. Silica Removal in Hydrometallurgy
Application Background:
In the hydrometallurgical process of extracting metals such as lithium, nickel, cobalt, and copper from ores, silicon often enters the solution as an impurity along with the minerals, affecting product purity and crystallization processes.
Role of Magnesium Oxide:
Adding magnesium oxide can react with silicic acid in the solution to form stable precipitates and simultaneously adjust the pH of the liquid phase.
It is used in the leaching solution purification stage to reduce the burden of subsequent impurity removal processes.
Advantages:
- No need to introduce additional alkali agents.
- Can be combined with phosphorus and iron removal operations to improve purification efficiency.
III. Silica Gel Recovery or Separation Processes
Application Background:
In some processes (such as silica gel production and wastewater treatment), it is necessary to selectively remove silica or recover silicon resources from a mixed system.
Role of Magnesium Oxide:
Controlling the reaction conditions allows it to react with free silicon to form amorphous or microcrystalline magnesium silicate, facilitating subsequent separation.
It can be used for pretreatment in silicon-aluminum separation and silicon-iron separation processes.
IV. Chemical Synthesis and Adsorbent Material Preparation
Application Background:
Magnesium silicate, as a functional material, can be used in adsorbents, catalyst supports, flame retardants, fillers, etc.
Transformation of Magnesium Oxide Silica Removal Process:
When designing synthesis routes, the desired structure can be directly generated by reacting MgO with a silicon source in one step.
For example, it can be used as a precursor for synthesizing composite materials such as layered nickel magnesium silicate (Ni-Mg silicate).
V. Ultrapure Water Systems in the Electronics/Photovoltaic Industry
Application Background:
The cleaning and preparation of electronic-grade wafers and photovoltaic silicon wafers require extremely low silicon content in water (ppb level).
Role of Magnesium Oxide:
Adding magnesium oxide in the pretreatment stage can capture trace amounts of silicic acid, reducing the burden on subsequent reverse osmosis and EDI systems.
It is suitable for operation in weakly alkaline environments without disrupting the water quality system balance.
VI. Impurity Silicon Control in Alkaline Slurry Systems
Application Background:
In the alkaline extraction processes of alumina, phosphate rock, or rare earth ores, silicon may form “sodium silicate colloids,” causing filtration difficulties.
Role of Magnesium Oxide:
Reacts with free silicic acid to precipitate as solid magnesium silicate.
Stabilizes the slurry structure and improves solid-liquid separation performance.
VII. Reutilization of Building Material By-products
Application Background:
Some silicon-containing waste liquids in the building materials industry can be converted into fillers or cement admixtures.
Magnesium Oxide Reaction Utilization:
Utilizes the reaction between magnesium oxide and silicon in waste liquids to generate magnesium silicate, which can be used as an additive.
Saves resources and achieves the goal of solid waste resource utilization.