PVC plastic sheeting is a flexible material made from polyvinyl chloride (PVC) as the main raw material, supplemented by plasticizers, stabilizers, fillers, additives, etc., through calendering or coating processes. It is widely used in advertising banner cloth, tarpaulins, awning cloth, inflatable products, and other fields. Magnesium carbonate (MgCO₃) is a white powdery inorganic mineral material, divided into light and heavy grades, and can also be processed into activated magnesium carbonate through surface modification. It is commonly used in industry as a high-temperature resistant filler, flame retardant, and stabilizer. In PVC plastic sheeting, magnesium carbonate is a multi-functional additive, not just a “cheap filler,” but plays an important role in enhancing thermal stability, processing performance, and the quality of the final product. The rational use of magnesium carbonate can help manufacturing enterprises optimize costs and enhance market competitiveness while ensuring performance.
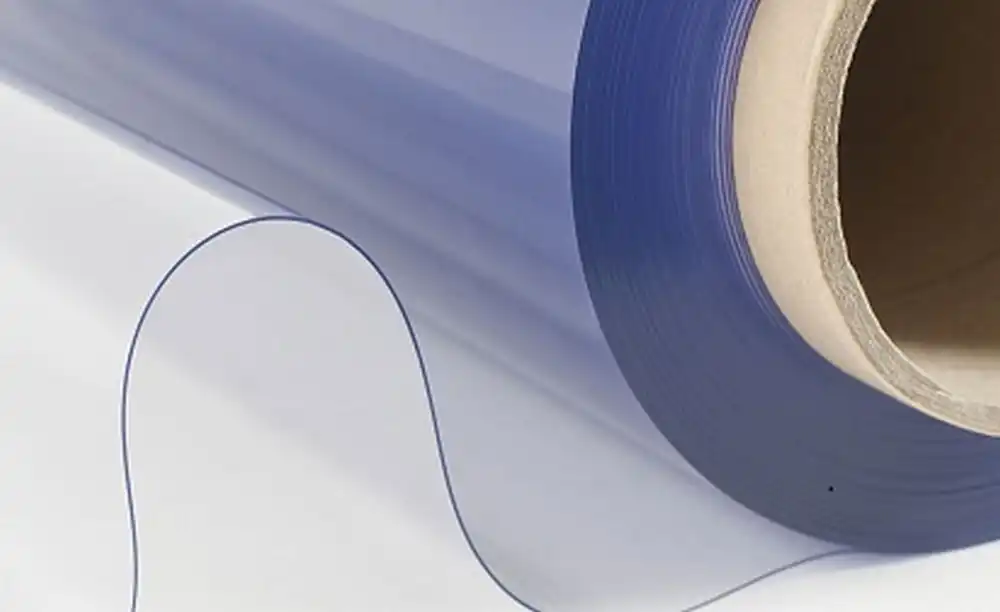
I. Specific Roles of Magnesium Carbonate in PVC Plastic Sheeting
(1) As a Filler:
- Increases the volume of the plastic sheeting, reducing raw material costs.
- Improves the thickness and texture of the product, making the material feel fuller.
(2) As an Auxiliary Heat Stabilizer:
- PVC is prone to decomposition due to high temperatures during processing, releasing HCl gas, which leads to yellowing and embrittlement of the material.
- Magnesium carbonate can adsorb some of the HCl, playing a role in inhibiting degradation and extending the service life of the material.
(3) Improving Processing Performance:
- The presence of magnesium carbonate can improve fluidity during the melt mixing process, making calendering, coating, extrusion, and other processes smoother.
- Reduces the phenomenon of sticking to molds and rollers, improving production efficiency.
(4) Enhancing Physical and Mechanical Properties:
- When added in appropriate amounts, it can improve the dimensional stability and a certain degree of tear resistance of the plastic sheeting.
- Especially in applications requiring high weather resistance (such as outdoor tarpaulins), the synergistic effect of magnesium carbonate is more significant.
II. Application Notes
- Control Dosage: It is generally recommended to add around 3% to 8% to the formula. Excessive addition can lead to brittleness and a decrease in breaking strength of the product.
- Particle Size Selection: Magnesium carbonate with smaller particle size and good dispersibility has better effects and can avoid affecting the surface smoothness of the product.
- Combination with Other Additives: It is usually necessary to combine it with organic tin stabilizers, calcium-zinc stabilizers, or lubricants to achieve the best overall performance.