PVC itself is prone to thermal degradation during hot processing (such as calendering, extrusion, coating) or prolonged exposure to high-temperature environments. This mainly manifests as:
- Yellowing and discoloration
- Material embrittlement
- Release of HCl gas (accelerating degradation)
To improve the thermal stability of PVC plastic sheeting, heat stabilizer systems are usually added, and magnesium oxide (MgO) is an effective auxiliary agent.
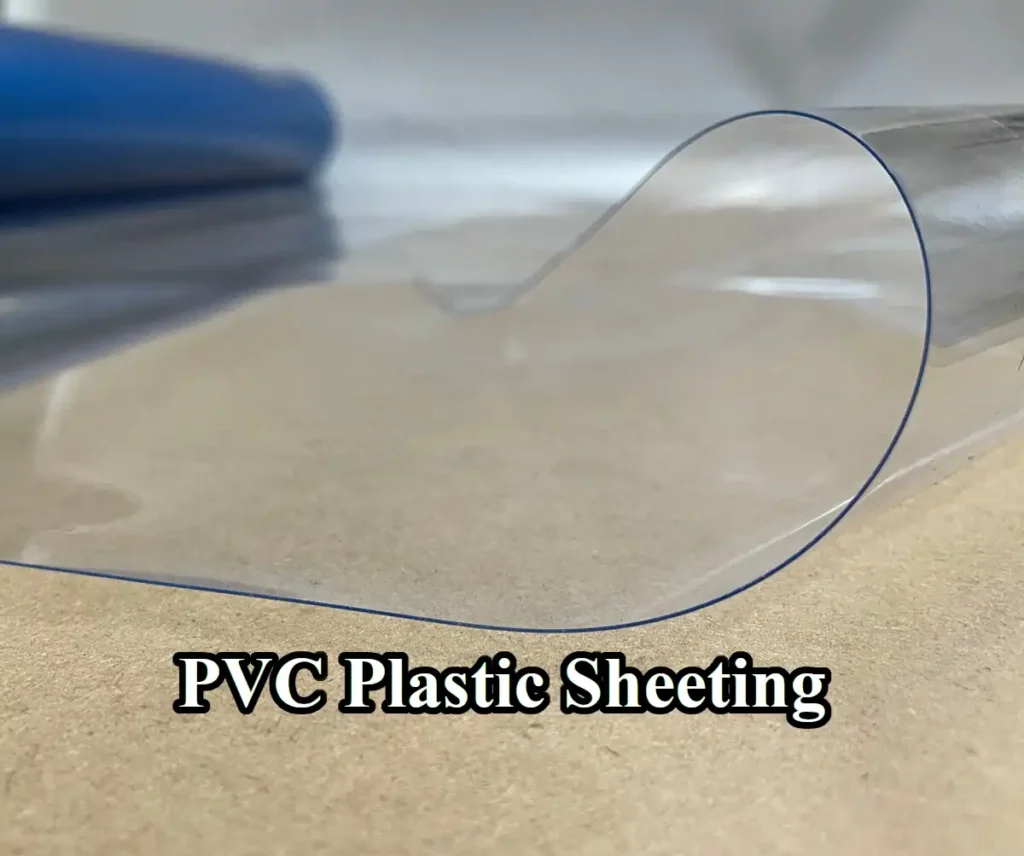
I. Basic Properties of Magnesium Oxide
- Chemical Properties: Strongly alkaline, capable of neutralizing acidic gases (such as HCl)
- Thermal Stability: Resistant to high temperatures (melting point up to 2800°C)
- Adsorption: Good capture effect on hydrogen chloride (HCl) gas
- Filler Properties: Fine, uniformly dispersed, with a certain reinforcing effect
II. Main Heat Resistance Modification Mechanisms of Magnesium Oxide in PVC Plastic Sheeting
1. Capturing HCl and Delaying PVC Degradation
PVC first releases HCl at high temperatures, leading to chain degradation.
Magnesium oxide can quickly react with HCl to form MgCl₂, inhibiting further catalytic degradation by HCl and improving the thermal stability of PVC.
2. Synergistic Effect with Other Stabilizers
Magnesium oxide is often used in conjunction with calcium-zinc stabilizers, organotin stabilizers, rare earth stabilizers, etc., to enhance the overall heat resistance effect.
Especially when combined with zinc-based stabilizers, it can avoid the early degradation and blackening problems easily caused by zinc-based stabilizers alone.
3. Improving Processing Window
After adding magnesium oxide, the processing temperature range of PVC plastic sheeting becomes wider, and the material is less likely to scorch or foam at high temperatures, improving the stability of the production process.
III. Influencing Factors
- Particle Size: Fine particle size magnesium oxide (nanoscale or micron-scale) has a better effect, reacts faster, and has excellent dispersibility.
- Dosage Control: The generally recommended addition amount is 1–3 phr (parts per hundred resin). Too much may cause a rough surface of the product and affect the appearance.
- Activated Magnesium Oxide: Magnesium oxide that has undergone surface treatment or activation has superior performance and can better compatibilize with the additives in the PVC system.