Magnesium hydroxide effectively enhances the flame retardant properties of PVC plastic sheeting through multiple mechanisms, including endothermic cooling, atmosphere dilution, formation of a protective layer, and neutralization of harmful gases. Reasonably designing the grade, dosage, and compounding system of magnesium hydroxide can achieve the best balance among environmental protection, safety, and performance.
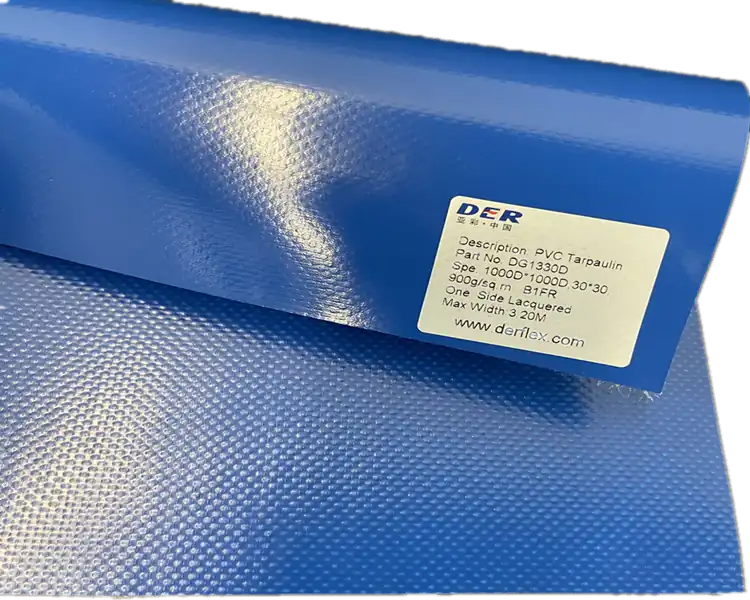
1. Why does PVC plastic sheeting need to be flame retardant?
PVC itself has a certain degree of flame retardancy because it contains chlorine. However, in practical applications, especially when made into large-area flexible materials like plastic sheeting, the addition of significant amounts of plasticizers, fillers, and other additives greatly reduces its flame retardant performance. Therefore, it is necessary to add extra flame retardants to ensure safety, such as for fire-resistant fabrics, construction barrier membranes, cable sheath fabrics, and advertising inkjet fabrics.
Magnesium hydroxide (Mg(OH)₂), as a halogen-free and environmentally friendly flame retardant, has been increasingly widely used in PVC plastic sheeting.
2. Detailed Explanation of Flame Retardant Mechanisms
(1) Endothermic Cooling
When PVC plastic sheeting is exposed to high temperatures or flames, magnesium hydroxide decomposes first, absorbing a large amount of heat.
This heat absorption process lowers the temperature of the surrounding materials, thereby slowing down the thermal decomposition and combustion rate of the PVC material itself.
(2) Release of Water Vapor, Diluting Combustible Gases
The decomposition releases a large amount of water vapor (H₂O gas), which can dilute the concentration of oxygen and combustible gases in the combustion zone.
This is equivalent to forming a local suffocating environment, making it difficult for the flame to spread.
(3) Formation of a Magnesium Oxide Protective Layer
The decomposed magnesium oxide is a high-temperature-resistant white ceramic material that can cover the surface of the material.
This layer of magnesium oxide film can block oxygen diffusion and at the same time protect the unburned PVC material inside.
(4) Synergistic Effect with HCl
PVC combustion releases toxic HCl gas. The magnesium oxide formed by the decomposition of magnesium hydroxide has a certain function of adsorbing and neutralizing HCl, reducing the emission of harmful gases.
3. Summary of the Advantages of Magnesium Hydroxide as a Flame Retardant
Magnesium hydroxide has a relatively high decomposition temperature, which is suitable for the processing temperature of PVC and will not decompose prematurely during the molding process. The release of a large amount of water vapor upon decomposition can dilute the concentration of oxygen and combustible gases in the combustion zone, inhibiting flame spread. At the same time, the generated magnesium oxide film can cover the surface of the material, providing dual protection of heat insulation and oxygen barrier. In addition, magnesium hydroxide can also adsorb some of the harmful HCl gas released by PVC combustion, reducing smoke and toxicity release. Most importantly, it is halogen-free and meets environmental regulations such as ROHS and REACH standards.
4. Precautions
High Dosage Requirement: Usually, an addition amount of more than 20% (relative to PVC resin) is needed to achieve effective flame retardancy, but this can affect the flexibility and processing flowability of the plastic sheeting.
Particle Size and Dispersion: Surface-modified magnesium hydroxide with an appropriate particle size needs to be used to avoid a rough product surface or increased processing difficulty.
Formula Balance: It is often used in combination with other flame retardant synergists (such as phosphorus-based flame retardants) to ensure flame retardant performance while taking into account mechanical properties and economy.