Magnesium oxide (MgO) has important application value in electronic low-dielectric low-temperature co-fired ceramics (LTCC). Magnesium oxide significantly improves the performance of high-frequency electronic devices in LTCC through dielectric regulation, low-temperature sintering assistance and thermal expansion matching. Future development directions include doping modification of nano-magnesium oxide, design of multifunctional composite systems (such as high thermal conductivity + low dielectric), and optimization of higher frequency application scenarios for 6G communications.
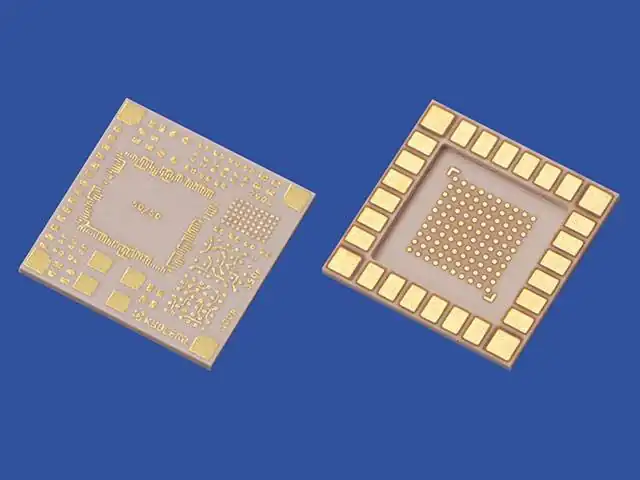
1. Dielectric property regulation
Low dielectric constant (Dk): LTCC materials require low dielectric constants in high-frequency/microwave circuits to reduce signal transmission delays and losses. The dielectric constant of magnesium oxide is about 9-10 (1MHz), which is higher than some specially designed low dielectric materials (such as glass ceramic systems), but by compounding with other low dielectric components (such as SiO₂, Al₂O₃ or glass phase), the overall dielectric constant can be effectively reduced.
Low dielectric loss (tanδ): Magnesium oxide has low dielectric loss (about 0.0001-0.001), which helps to reduce the energy dissipation of high-frequency signals and improve device efficiency.
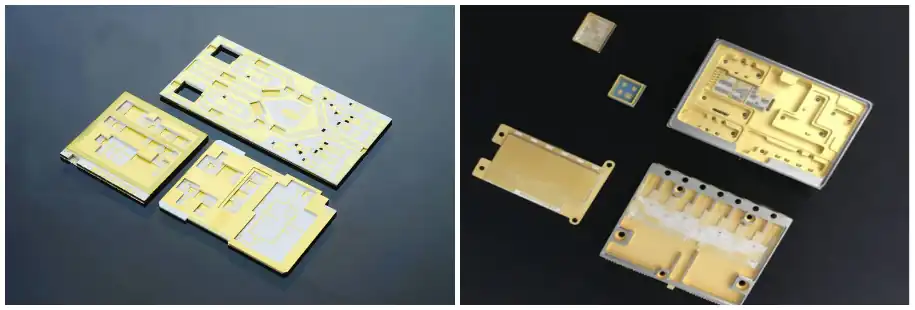
2. Low-temperature sintering characteristics
Reducing sintering temperature: LTCC needs to be sintered at 850–900°C to be compatible with low-melting-point metal electrodes such as silver and copper. Magnesium oxide can be used as a sintering aid to promote the densification between ceramic particles and reduce the sintering temperature by reacting with the glass phase to form a low-melting-point liquid phase (for example, combined with borosilicate glass).
Inhibiting abnormal grain growth: The addition of magnesium oxide can refine the grains and avoid performance degradation caused by excessive grain growth at high temperatures, thereby achieving high densification at low temperatures.
3. Thermal expansion coefficient (CTE) matching
LTCC needs to match the thermal expansion coefficient of the semiconductor substrate (such as Si, GaAs) or metal packaging materials to avoid cracking caused by thermal stress. Magnesium oxide has a high coefficient of thermal expansion (~13×10⁻⁶/K). By compounding with other low-expansion components (such as SiO₂, Al₂O₃), the overall CTE can be adjusted to be close to silicon (~3×10⁻⁶/K), thereby improving the thermal reliability of the device.
4. Mechanical and chemical stability
Mechanical strength: The addition of magnesium oxide can improve the mechanical strength of LTCC (such as bending strength) and enhance the impact resistance of the device during packaging and use.
Chemical inertness: Magnesium oxide has excellent chemical stability in high temperature and humid environments, which can improve the anti-aging performance of LTCC and extend the life of the device.
5. Typical application cases
High-frequency devices: In RF modules and microwave antennas for 5G communications, MgO-based LTCC is used to manufacture low-loss substrates, filters and resonators.
Multilayer substrates: Magnesium oxide composite ceramics are integrated with metal electrodes (such as Ag) through a co-firing process for high-density interconnect substrates to meet miniaturization requirements.
Sensor packaging: Using its low dielectric and thermal stability, it is applied to sensor packaging in high temperature/high frequency environments.
6. Technical challenges and optimization directions
Balance of dielectric properties: It is necessary to avoid excessive magnesium oxide leading to an increase in dielectric constant, which is usually optimized through a composite formula (such as MgO-SiO₂-Al₂O₃-B₂O₃ system).
Interface reaction control: The compatibility of magnesium oxide and glass phase needs to be finely controlled to prevent the generation of high-loss byproducts by interface reaction.
Green process: Develop lead-free, low-toxic magnesium oxide LTCC formula to meet environmental protection requirements.