Reactive magnesium oxide (MgO), as a highly reactive chemical substance, possesses unique surface structures and chemical properties, making it exhibit a wide range of potential applications in various industrial fields.
Hydrometallurgy, which employs aqueous solutions for metal extraction and refining, is widely used in the extraction and processing of non-ferrous metals due to its advantages of low energy consumption, minimal environmental pollution, and high recovery rates. Cobalt, as an important strategic metal, is widely used in battery materials, alloy manufacturing, catalysts, and the production of special steels. Optimizing its extraction technology is of great significance for improving resource utilization efficiency and promoting industrial upgrading.
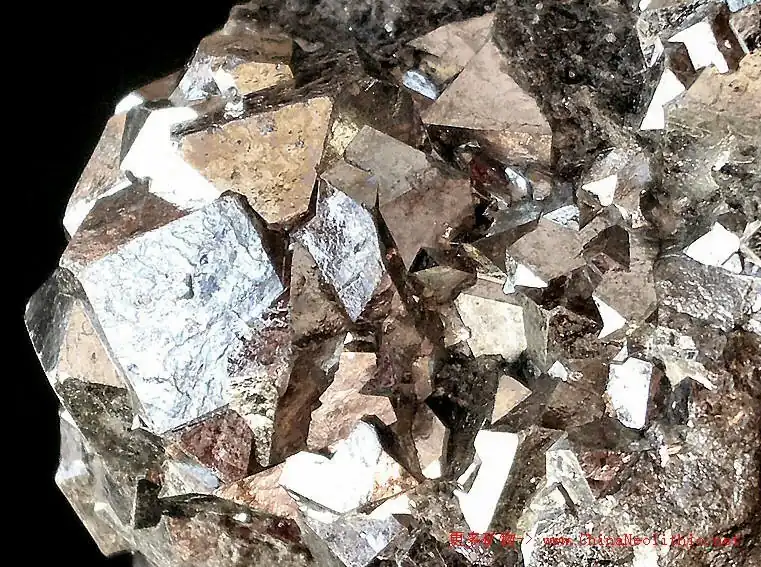
Unique Advantages of Reactive Magnesium Oxide in Hydrometallurgical Cobalt Extraction
- Efficient Dissolution Promotion and Selectivity:
Reactive magnesium oxide can act as an effective catalyst or auxiliary agent in hydrometallurgical cobalt extraction, promoting the dissolution of cobalt minerals in aqueous solutions. Its high reactivity facilitates the release of cobalt ions from ores or wastes into the liquid phase system. At the same time, reactive magnesium oxide can, to some extent, inhibit the dissolution of other impurity metals, improving the extraction selectivity of cobalt and laying the foundation for subsequent separation and purification steps.
- Improvement of Solution Environment:
In the hydrometallurgical process, factors such as pH, ionic strength, and redox potential of the solution significantly affect the dissolution and precipitation behavior of metals. The addition of reactive magnesium oxide can adjust the pH of the solution, keeping it within a range that favors the dissolution of cobalt ions while disfavoring the precipitation of impurity ions. In addition, reactive magnesium oxide can undergo complexation reactions with certain ions in the solution, altering the chemical properties of the solution and further optimizing the cobalt extraction conditions.
- Enhanced Precipitation and Separation:
In the subsequent steps of hydrometallurgical cobalt extraction, it is usually necessary to separate cobalt from the solution through methods such as precipitation, filtration, and solvent extraction. The presence of reactive magnesium oxide can influence the formation rate and morphology of precipitates, making the cobalt precipitation process more efficient and controllable. Furthermore, by adjusting the dosage of reactive magnesium oxide and reaction conditions, it is possible to control the particle size of the precipitates, optimize filtration and washing effects, and reduce cobalt loss.
Process Flow of Hydrometallurgical Cobalt Extraction Using Reactive Magnesium Oxide
Generally, the process flow of hydrometallurgical cobalt extraction using reactive magnesium oxide includes steps such as ore crushing, grinding, leaching, solid-liquid separation, solution purification, cobalt precipitation and separation, and subsequent drying and smelting. In the leaching stage, reactive magnesium oxide is mixed with ore or waste, and reacted under appropriate temperature and acidity conditions to allow cobalt ions to enter the solution. Insoluble matter is then removed through solid-liquid separation, and the solution is purified to remove impurity ions. Finally, cobalt precipitates are obtained through steps such as precipitation, filtration, washing, and drying, which are then processed into the final product through smelting.
Environmental Benefits of Hydrometallurgical Cobalt Extraction Using Reactive Magnesium Oxide
Compared with traditional pyrometallurgy and other hydrometallurgical techniques, hydrometallurgical cobalt extraction using reactive magnesium oxide has significant advantages in environmental protection. First, the process has lower energy consumption, reducing energy consumption and greenhouse gas emissions. Second, because impurity ions in the solution are effectively removed, the difficulty of wastewater treatment is reduced, which is conducive to realizing wastewater recycling and meeting discharge standards. In addition, reactive magnesium oxide, as a renewable resource, its recycling is also in line with the concept of green development.
Practical Application Cases and Effect Analysis
Taking a hydrometallurgical cobalt extraction project from a cobalt-containing waste residue as an example, the research team introduced reactive magnesium oxide as a regulator in the leaching stage. The experimental results showed that, compared with the control group that did not use reactive magnesium oxide, the leaching rate increased by approximately 15%, and the cobalt ion concentration in the leachate was more stable. In the subsequent precipitation process, reactive magnesium oxide was used as a co-precipitant, and the purity of the obtained cobalt product reached more than 99%, which is much higher than the industry average. In addition, the resource recovery rate of the project was also significantly improved, achieving a win-win situation for economic and environmental benefits.
In summary, reactive magnesium oxide plays a crucial role in hydrometallurgical cobalt extraction.