For asphalt flame retardants, it is recommended to choose hexagonal platelet-shaped magnesium hydroxide with purity ≥99%, particle size 1.5-2.0 μm, and modified with silane. For high performance, nano-magnesium hydroxide products can be chosen. For petroleum asphalt, it is suggested to compound it with zinc borate, while coal asphalt requires combination with layered silicates.
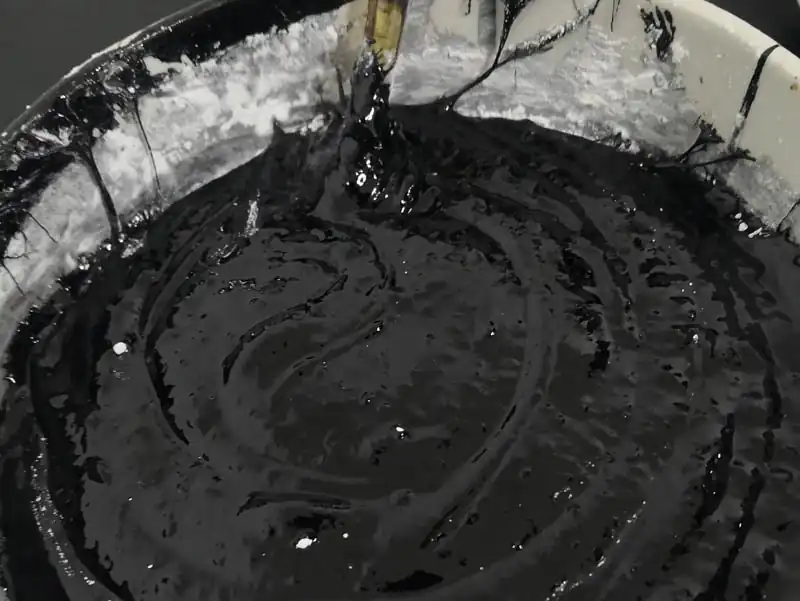
I. Technical Characteristics of Magnesium Hydroxide as an Asphalt Flame Retardant
Flame Retardant Mechanism
Magnesium hydroxide achieves flame retardant effect through a triple mechanism:
- Endothermic decomposition: Decomposes at 340-490℃, absorbing heat (44.8 kJ/mol), reducing the material surface temperature;
- Gas phase dilution: Releases water vapor to dilute oxygen concentration, inhibiting combustion chain reactions;
- Barrier protection: Forms a magnesium oxide (MgO) covering layer to isolate oxygen and promote carbonization of the asphalt surface.
Core Advantages
- Environmentally friendly and non-toxic, decomposition products are only water and magnesium oxide, complying with RoHS standards;
- Significant smoke suppression effect, can neutralize acidic gases such as SO₂ and CO₂ produced during combustion;
- High decomposition temperature, suitable for high-temperature processed asphalt materials (e.g., modified asphalt processing temperature reaches 180-200℃).
II. Key Performance Indicators and Specification Selection
Indicator | Recommended Parameters | Impact on Flame Retardant Effect |
Purity | ≥99.5% | Impurities (e.g., Fe, Ca) will reduce thermal stability. |
Particle Size | D50=1.5-2.0μm (Nano-grade is better) | The smaller the particle size, the better the dispersibility, and the flame retardancy improves by 30%. |
Morphology | Hexagonal platelet structure | Enhances interlayer stacking and improves the density of the char layer. |
Surface Modification | Surface coating treatment with silane coupling agent | Improves compatibility with asphalt and reduces aggregation. |
III. Adaptation Schemes for Different Types of Asphalt
Petroleum Asphalt
- Recommended compounding: Magnesium hydroxide + 5% zinc borate, which can increase the oxygen index to over 28%;
- Addition amount: 40-50%, needs to be combined with compatibility agents (e.g., SBS) to avoid a decrease in mechanical properties.
Coal Asphalt
- Requires higher purity (≥99.9%) to resist the acidic components of coal tar;
- Compounded with layered silicates (e.g., montmorillonite) to synergistically improve flame retardant and anti-aging properties.
IV. Mainstream Products and Engineering Cases
Recommended Products
- ①: Purity 99.5%, D50≤1.2 μm, specifically for cable and asphalt flame retardation;
- ②: Compound formula, containing magnesium hydroxide + APP, addition amount can be reduced to 35%.
Successful Applications
- Tunnel flame retardant asphalt: Uses bio-based modified magnesium hydroxide, oxygen index reaches 28%, smoke density reduced by 40%;
- High-speed rail track filling material: 45% nano-magnesium hydroxide + 3% red phosphorus, passes UL94 V-0 level test.
V. Usage Recommendations
Processing Technology
- Staged addition: First mix with 60% asphalt, then add the remaining components to avoid localized overheating and decomposition;
- Temperature control: Mixing temperature ≤180℃ to prevent premature deactivation of magnesium hydroxide.
Economic Optimization
- Although nano-magnesium hydroxide has a high unit price, the addition amount can be reduced by 20%, resulting in lower overall cost;
- Prioritize selecting pre-modified magnesium hydroxide to avoid performance fluctuations caused by self-modification.