Description
Background technique
Magnesium oxide (chemical: MGO) It is the oxide of magnesium, an ionic compound. It is a white solid at room temperature. Magnesium oxide exists in the form of square magnesium stones in nature and is the raw material for magnesium smelting.
Magnesium oxide is commonly known as magnesia, also known as magnesium oxygen. Magnesium oxide is alkaline oxides. It has the generality of alkaline oxides and belongs to the gel material. White powder (light yellow is magnesium nitride), which is odorless, odorless, and non -toxic. It is a typical alkaline earth metal oxide and chemical MGO. White powder, the melting point is 2852 ° C, and the boiling point is 3600 ° C. Soluble in acid and ammonium salt solution, insoluble in alcohol.
It is exposed to the air, which is easy to absorb water and carbon dioxide and gradually becomes alkaline magnesium carbonate. Lightweight products are faster than heavy quality. They are combined with water under certain conditions to generate magnesium hydroxide, which shows a pH of a slightly alkaline response and saturated aqueous solution. For 10.3. It is soluble in water and ammonium salt in water, and its solution is alkaline. Insperfolid in ethanol. It is visible and near -ultraviolet light. Magnesium (MGCO3), Baiyun Stone (MGCO3 · CACO3) and seawater are the main raw materials for producing magnesium oxide. Thermal decomposition diamond magnesium or magnesium oxide. Use lime to remove magnesium hydroxide and precipitate, and burns magnesium hydroxide to obtain magnesium oxide. You can also use the magnesium hydrochloric block or bromamine as raw materials obtained in the use of seawater. The sodium hydroxide or sodium carbonate is generated to generate magnesium hydroxide or alkaline -type magnesium carbonate, and then burned magnesium oxide. China mainly uses Magnesium ore, white cloudstone, brine or halogen as the raw material.
Magnesium oxide has high refractory insulation performance. It can be transformed into crystals with high temperature burning above 1000 ° C, and rises to 1500–2000 ° C. It becomes dead magnesium oxide (that is, magnesium) or sintering magnesium oxide.
Ink is an important material for printing. It shows patterns and text on printed materials by printing or inkjet. The ink includes the main ingredients and auxiliary ingredients, which are uniformly mixed with repeated rolling and repeatedly rolled into a sticky glue fluid. It is composed of conjunction (resin), pigments, fillers, additives and solvents. It is used for various prints such as books, packaging and decoration, building decoration and electronic circuit boards. With the increase in social demand, ink varieties and yields have also expanded and increased accordingly.
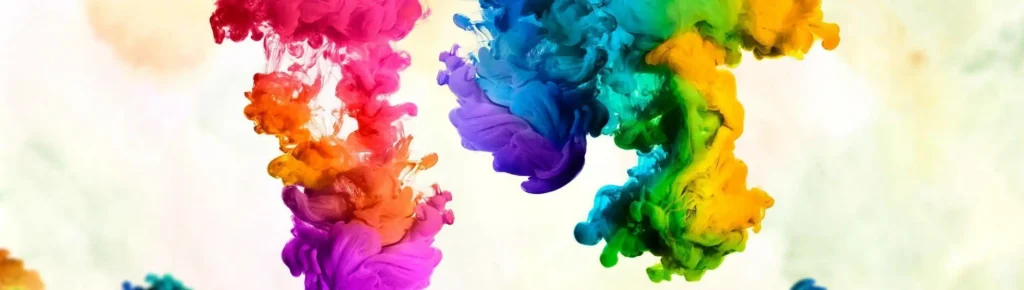
As the requirements for printing are getting higher and higher, the fineness and purity of the ink are getting more and more concerned. We know that the fineness of the ink is directly related to the nature of the pigment, the nature of the filling, and the size of the particles. In general, the ink made of inorganic pigments (excluding carbon black) is not good, and the particles are thicker, which has a lot to do with the rolling process of the ink. Ink is rolled. The more times the number of times during the process, the more uniform it will look, the greater the contact surface of the pigment particles and the linked material, and the finer the ink particles, the better and stable its printing performance. Obviously, the fineness of the ink is closely related to the quality of printing.
Invention content
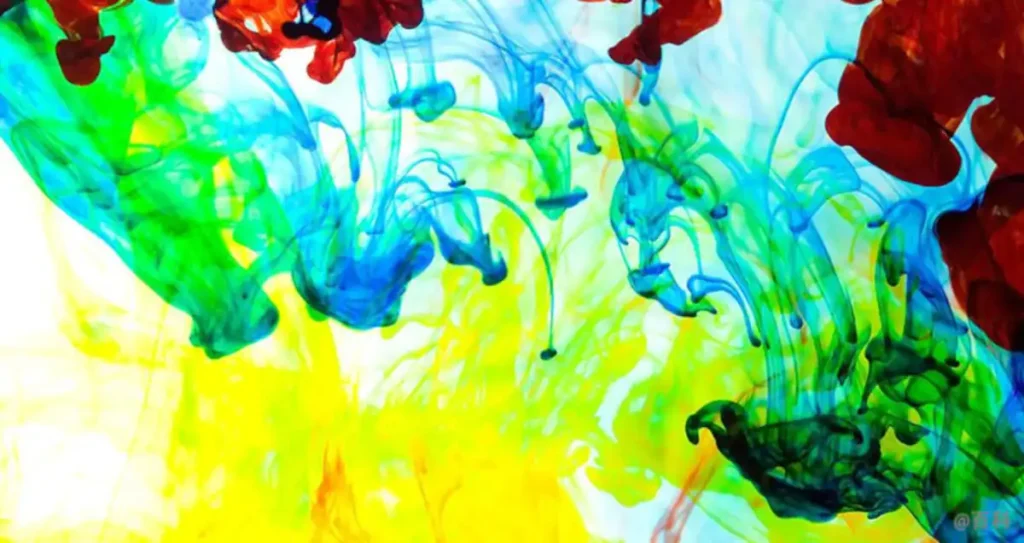
The purpose of the invention is to propose a method of preparation of magnesium oxide ink with strong stability and clear printing.
In order to achieve the above goals, the technical solution adopted by the present invention is:
A method of preparing a magnesium oxide ink, including the following steps:
a. Mix the alcoholic acid resin and polyamide resin, stir well, heat up to 60-80 ° C, add acetate ethyl, stir for 10-20 minutes;
b. Send the solution obtained from the step A and the water-soluble acrylic resin into the reaction kettle, stir up to 100-120 ° C, and stir for 50-60 minutes;
c. Add carbon powder to the reaction kettle and stir for 20-30 minutes;
d. Add magnesium oxide and cross-linked agents, continue to stir for 60-100 minutes, and grind to scatter 15-35um slurry, that is, obtain magnesium oxide ink.
The weight of the alcoholic acid resin described in step A is 15-25 copies, the weight of polyamide resin is 18-26, and the weight of ethyl acetate is 2-8 copies.
The weight of the water-soluble acrylic resin described in step B is 5-8 copies.
The weight of the carbon powder described in step C is 25-35 copies.
The weight of the magnesium oxide in the step D is 14-22 copies, and the weight of the cross-linked agent is 1-3.
Due to the above technical solution, the beneficial effect of the present invention is:
The ink of the present invention has good luster, bright colors, and strong solidity. It has good water resistance, melting, wear resistance, good stability, not easy to fall off, clear printing, and suitable for different paper.