Abstract
The present invention provides a method for preparing magnesium hydroxide flame retardant by one-step hydrothermal method, comprising mixing magnesium chloride, ethanol and water to obtain a mixed solution, adding dispersant polyethylene glycol to the mixed solution to obtain magnesium chloride mother solution; adding the magnesium chloride mother solution dropwise to an ammonia solution with a mass concentration of 2-36% in a closed hydrothermal reactor under constant temperature stirring at 40-200°C until the pH value of the reaction solution is 9-12, stopping the dropwise addition, stirring at constant temperature for 0.5-5 hours, and separating and purifying the reaction solution to obtain the magnesium hydroxide flame retardant. The beneficial effects of the method of the present invention are mainly reflected in: (1) magnesium hydroxide synthesis and hydrothermal modification are completed in one step, which reduces the process flow, improves production efficiency and reduces energy consumption; (2) the synthesized magnesium hydroxide has perfect crystallinity, small surface polarity, is not easy to agglomerate, and is fast to filter; (3) the production process is carried out in a closed hydrothermal reactor, ammonia water is fully utilized, and there is no ammonia gas leakage, which reduces costs and does not pollute the environment.
Description
Method for preparing highly dispersed magnesium hydroxide flame retardant by one-step hydrothermal method
(I) Technical field
The present invention relates to a method for preparing highly dispersed magnesium hydroxide flame retardant by one-step hydrothermal method.
(II) Background technology
As polymer materials such as plastics, rubbers, and synthetic fibers continue to enter people’s daily lives, people have higher and higher requirements for the flame retardant properties of these materials. In particular, when polymer materials are used in combination with electronic devices (such as wires and cables), they are prone to fire when working under long-term heating and power generation conditions. For this reason, it is necessary to study effective flame retardants to solve the problems of flammability and smoke generation of polymer materials. Compared with other flame retardants (such as halogen, phosphorus, aluminum hydroxide, and antimony trioxide), magnesium hydroxide has the characteristics of flame retardancy and smoke suppression, high thermal stability (decomposition temperature is 340-490°C), and non-toxicity. When used as a filler, it can make plastics withstand higher temperatures, which is conducive to accelerating the extrusion speed and shortening the molding time. It is especially suitable for use with heat-resistant polymers such as PP, PA, and POM.
Although magnesium hydroxide has many advantages, the synthesis of highly dispersed magnesium hydroxide flame retardants is a big problem. Magnesium hydroxide synthesized by conventional processes often has the following problems: (1) imperfect crystallization, strong surface polarity, easy gelation, very difficult to wash and filter, and easy to re-agglomerate during drying; (2) wide particle size distribution and poor dispersibility; (3) low purity. The above problems cause poor compatibility of magnesium hydroxide with polymer materials, and large addition amount reduces the mechanical properties and heat resistance of the material.
From a microscopic point of view, the formation of magnesium hydroxide grains includes two steps: crystal nucleation and growth. The ordinary synthesis process (precipitation method) generally has a faster crystal nucleation and growth rate, and the ion concentration distribution in the system is uneven, which easily causes imperfect magnesium hydroxide grains and uneven particles, making the magnesium hydroxide surface energy higher, easy to agglomerate and difficult to filter. The use of supergravity method (Song Yunhua, Chen Jiangming, Liu Lihua, etc. Application research on the preparation of nano magnesium hydroxide flame retardant by supergravity technology, Chemical Minerals and Processing, 2004 (5): 19-23) and microwave method (Fang Yuxun, He Renbin, Liu Yanhong. Preparation of magnesium hydroxide and magnesium oxide by microwave catalysis of brine-dolomite. Inorganic Salt Industry, 2005, 37 (2): 35-37) can improve the uniformity of ion concentration distribution in the system, thereby improving the distribution of magnesium hydroxide particle size. However, the method used is that the external mechanical energy acts on magnesium hydroxide, and the effect on the surface energy of the grains is limited, and subsequent surface modification is required.
Hydrothermal synthesis is a method of changing the internal energy field in the synthesis process of magnesium hydroxide. It can change the surface polarity of magnesium hydroxide and improve the crystal phase structure of magnesium hydroxide. The hydrothermal synthesis technology reported in the literature (Xiang Lan, Jin Yongcheng, Jin Yong. Study on the crystallization habit of magnesium hydroxide. Journal of Inorganic Chemistry, 2003, 19 (8): 837-842; Chinese patent CN1740269) is a two-step method, first synthesizing magnesium hydroxide crystals at room temperature, and then modifying the morphology and surface polarity of the magnesium hydroxide crystals by hydrothermal method. However, this method has the following defects: (1) high hydrothermal temperature, long process and high cost; (2) easy to cause environmental pollution of ammonia; (3) hydrothermal modifiers (such as ammonia water, sodium hydroxide, urea) are highly corrosive to equipment; (4) the hydrothermal modification effect is limited.
(III) Content of the invention
In order to overcome the above-mentioned shortcomings of the current hydrothermal modification technology of magnesium hydroxide, the present invention provides a new process for preparing magnesium hydroxide flame retardant by one-step hydrothermal method. This method is not only simple in process and low in cost, but also has high purity, good dispersion, regular morphology and adjustable magnesium hydroxide product.
The technical scheme adopted by the present invention is:
A method for preparing magnesium hydroxide flame retardant by a one-step hydrothermal method, the method comprising:
(1) mixing magnesium chloride, ethanol and water to obtain a mixed solution, adding a dispersant polyethylene glycol to the mixed solution to obtain a magnesium chloride mother liquor; the amount ratio of the magnesium chloride, ethanol, water and polyethylene glycol is: 10-50g: 20-60mL: 40-80mL: 0.05-1.0g;
(2) taking an ammonia solution with a mass concentration of 2-36% and placing it in a closed hydrothermal reactor, heating it to 40-200°C under stirring, keeping the reactor at a constant temperature, and then dripping the magnesium chloride mother liquor obtained in step (1) into the hydrothermal reactor through a high-pressure feed pump until the pH of the reaction liquid is 9-12, stopping the dripping, stirring at a constant temperature for 0.5-5 hours, and separating and purifying the reaction liquid to obtain the magnesium hydroxide flame retardant.
The present invention is preferably carried out under constant temperature and pressure conditions. Since the reactor is sealed, its internal pressure is basically constant under constant temperature conditions, so it is only necessary to control the temperature to be constant during operation.
The polyethylene glycol is usually selected from products with a molecular weight of 500 to 6000, and PEG6000 is preferred in the present invention.
Preferably, the temperature in the reactor in step (2) is controlled at 100 to 200°C.
The separation and purification can be carried out according to conventional methods. The separation and purification steps in the present invention can be: after the reaction is completed, the reaction solution is cooled, the filter residue is filtered and washed with distilled water, and dried to obtain the magnesium hydroxide flame retardant.
Preferably, the method is as follows:
(1) Mix magnesium chloride, ethanol and water to obtain a mixed solution, add dispersant PEG6000 to the mixed solution to obtain a magnesium chloride mother solution; the amount ratio of the magnesium chloride, ethanol, water and PEG6000 is: 15-30.5g: 20-50mL: 50-80mL: 0.1-0.2g;
(2) Prepare an ammonia solution with a mass concentration of 2-25%, place it in a closed hydrothermal reactor, and slowly drop the magnesium chloride mother solution obtained in step (1) into the reactor under constant temperature stirring at 100-200°C until the pH of the reaction solution is 9-12, stop dropping, stir at constant temperature for 2-5 hours, cool the reaction solution naturally, filter the residue, wash it with distilled water, and dry it at 110°C to obtain the magnesium hydroxide flame retardant.
According to the method of the present invention, highly dispersed magnesium hydroxide particles are prepared with a primary particle size of 0.1 to 2.0 μm, a specific surface area of 5 to 20 m2/g, a purity of more than 99%, and a hexagonal flake structure.
The beneficial effects of the method of the present invention are mainly reflected in: (1) the synthesis and hydrothermal modification of magnesium hydroxide are completed in one step, which reduces the process flow, improves production efficiency, and reduces energy consumption; (2) the synthesized magnesium hydroxide has perfect crystallinity, small surface polarity, is not easy to agglomerate, and is fast to filter; (3) the production process is carried out in a closed hydrothermal reactor, ammonia water is fully utilized, there is no ammonia leakage, which reduces costs and does not pollute the environment.
(IV) Description of the drawings
Figure 1 is the morphology of magnesium hydroxide particles synthesized in Example 2 (80°C);
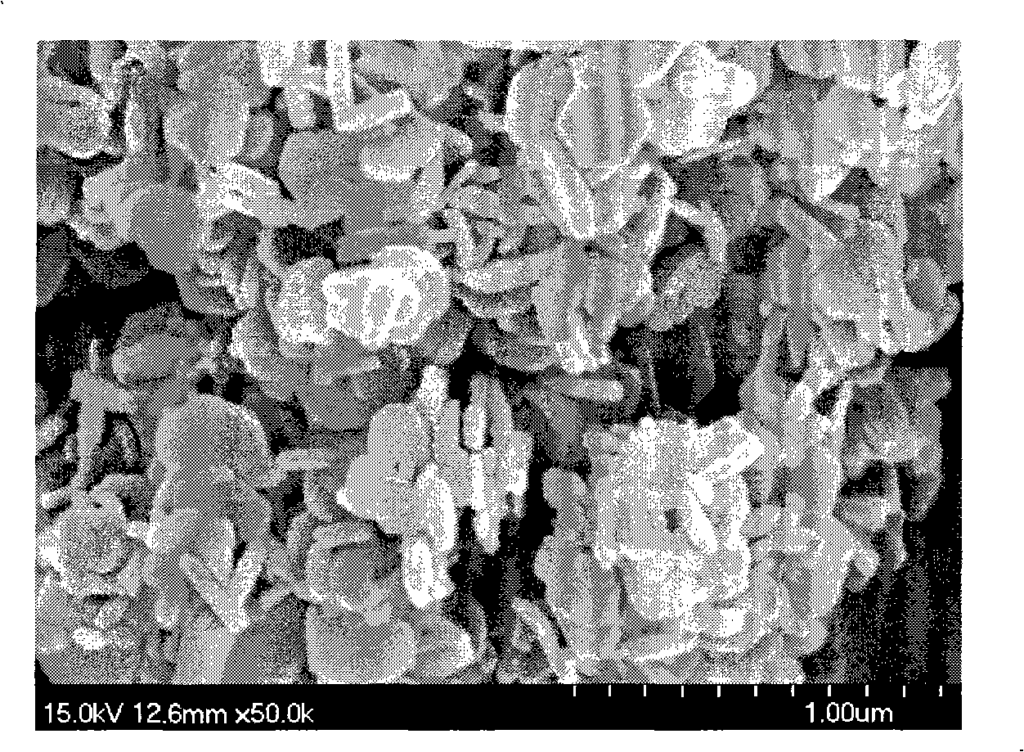
Figure 2 is the morphology of magnesium hydroxide particles synthesized in Example 3 (100°C);
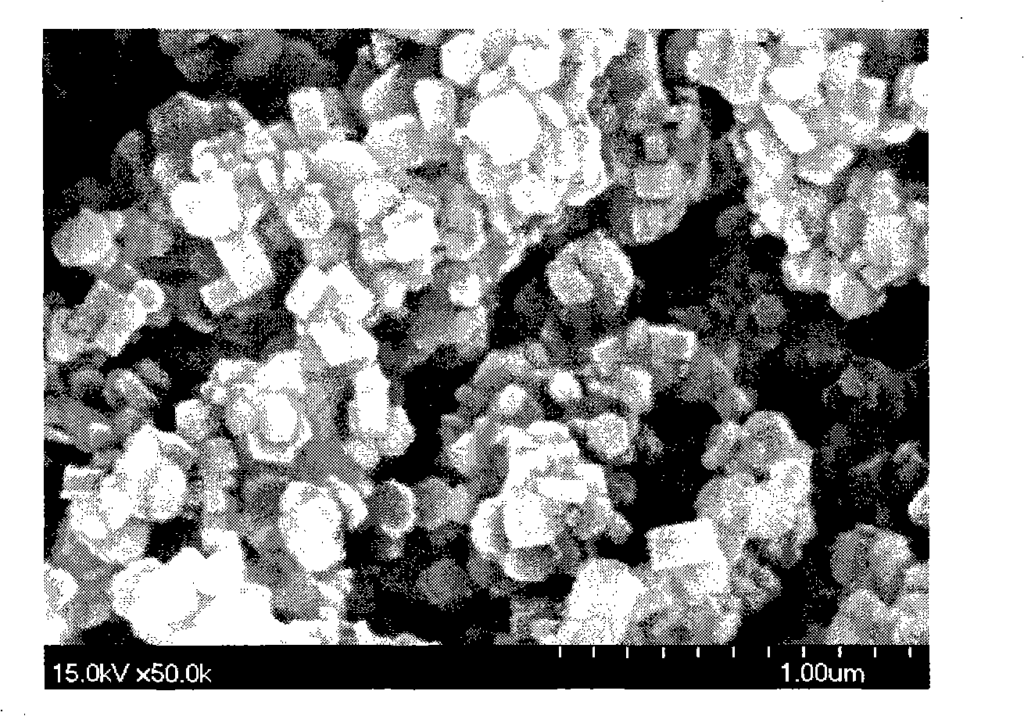
Figure 3 is the morphology of magnesium hydroxide particles synthesized in Example 4 (120°C);
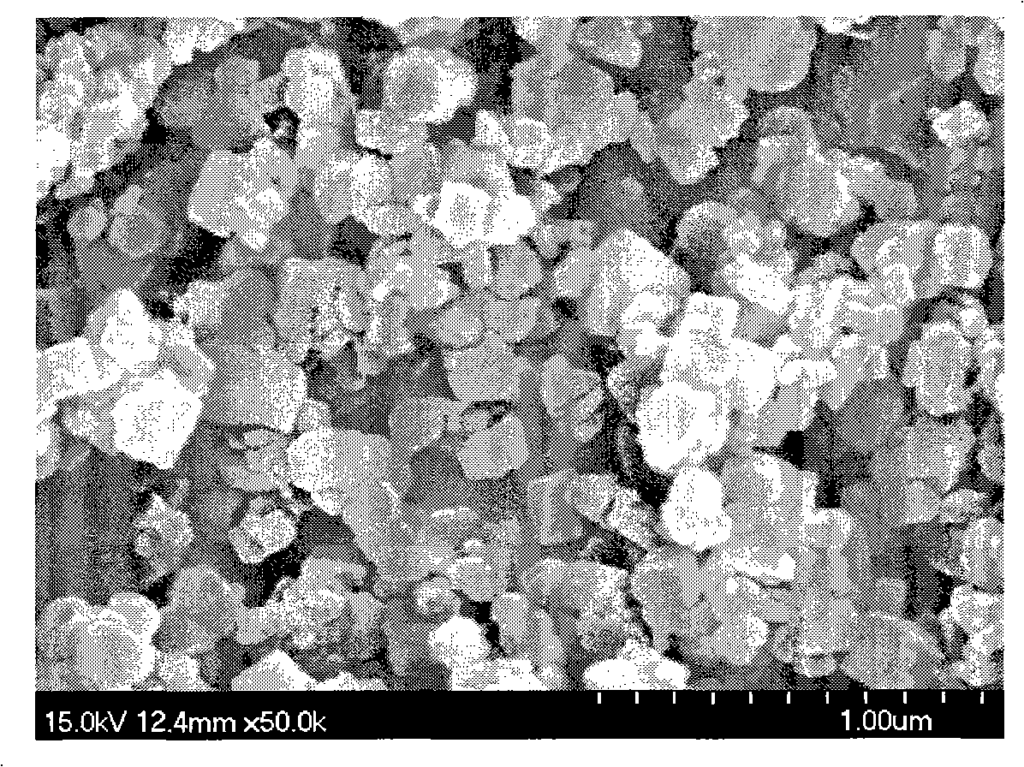
Figure 4 is the morphology of magnesium hydroxide particles synthesized in Example 6 (200°C);
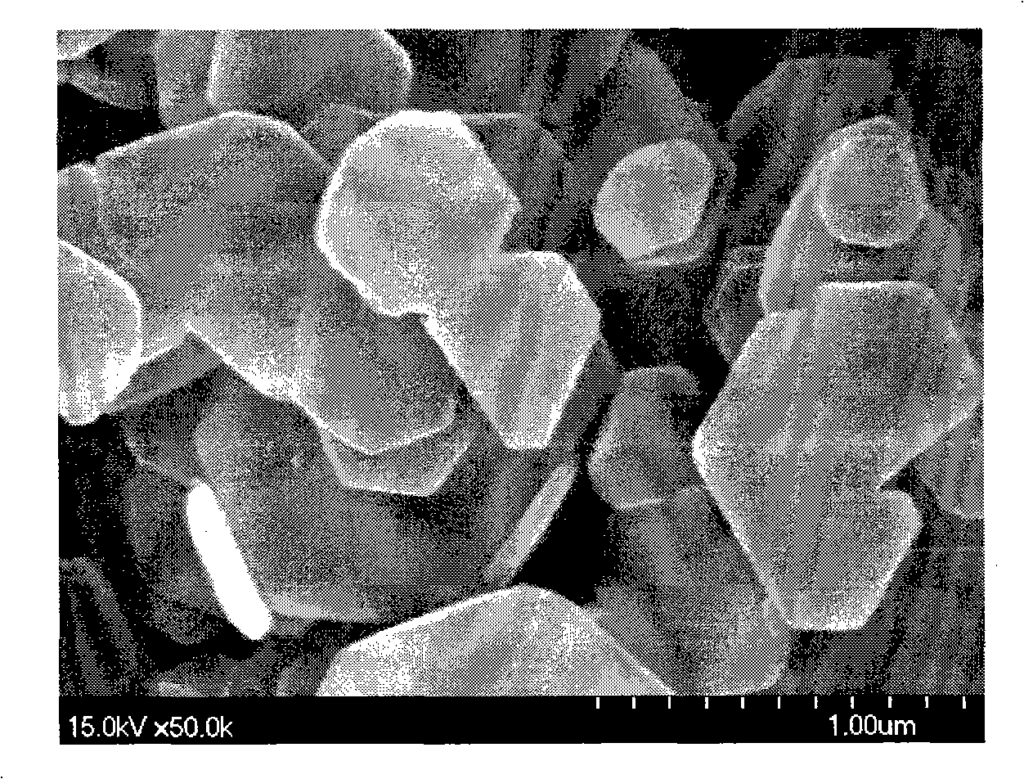
Figure 5 is the X-ray powder diffraction pattern of magnesium hydroxide particles synthesized in Example 6 (200°C);
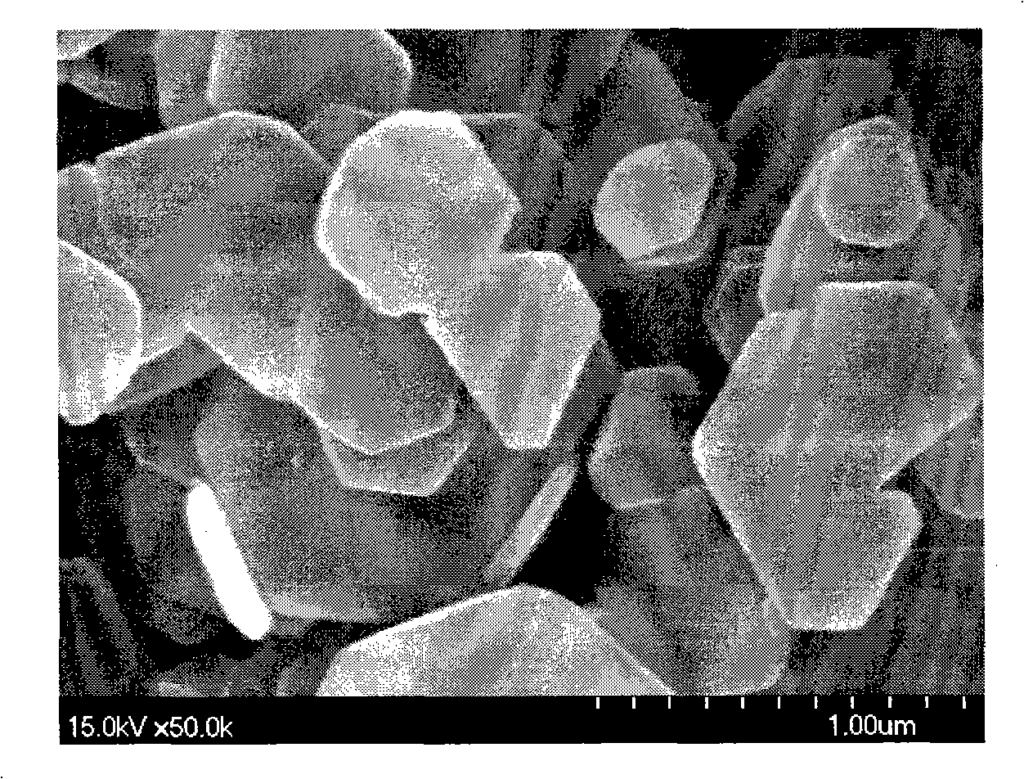
(V) Specific implementation methods
The present invention is further described below in conjunction with specific examples, but the scope of protection of the present invention is not limited thereto:
Example 1:
30.4845g of magnesium chloride and 0.2145g of PEG 6000 (Shanghai Zhuokang Biotechnology Co., Ltd.) were dissolved in 50ml of distilled water, and 50ml of ethanol was added to obtain magnesium chloride mother solution (1). Take a 6% ammonia solution and place it in a closed hydrothermal reactor. Heat it to 40°C while stirring, keep the reactor constant temperature, and then add the magnesium chloride mother solution (1) to the hydrothermal reactor through a high-pressure feed pump until the pH of the reaction solution is 9.5, stop adding, keep the reaction solution constant at 40°C for 1 hour, cool the reaction solution, filter, wash with distilled water, and dry the resulting product at 110°C to obtain a white powder. The particle size and morphology of the sample were observed using a transmission electron microscope (SEM). The powder was a nanoscale hexagonal plate-like crystal with high purity (99.5%), good dispersion, and regular morphology. The crystal particle size was mainly distributed in the range of 200-300nm, the crystal thickness was mainly distributed in the range of 20-50nm, the specific surface area was 4-20m2/g, the surface polarity was small, it was not easy to agglomerate, and the filtration was fast.
Example 2:
30.4845g magnesium chloride and 0.2145g PEG 6000 (Shanghai Zhuokang Biotechnology Co., Ltd.) were dissolved in 50ml distilled water, and 50ml ethanol was added to obtain magnesium chloride mother solution (1). A 6% ammonia solution was placed in a closed hydrothermal reactor, heated to 80°C under stirring, and the reactor was kept at a constant temperature. Then, the magnesium chloride mother solution (1) was added dropwise to the hydrothermal reactor through a high-pressure feed pump until the pH of the reaction solution reached 9.5, and then the addition was stopped. After stirring at a constant temperature of 80°C for 1 hour, the reaction solution was cooled, filtered, washed with distilled water, and the obtained product was dried at 110°C to obtain a white powder. The particle size and morphology of the sample were observed by transmission electron microscopy (SEM). FIG1 shows a 50,000-fold magnified photograph of the magnesium hydroxide prepared in this example. The powder is a nano-scale hexagonal plate-like crystal with high purity (99.5%), good dispersion, and regular morphology. The crystal particle size is mainly distributed in 150-200 nm, the crystal thickness is mainly distributed in 50-100 nm, the specific surface area is 4-20 m2/g, the surface polarity is small, it is not easy to agglomerate, and the filtration is fast.
Example 3:
30.4845 g of magnesium chloride and 0.2145 g of PEG 6000 (Shanghai Zhuokang Biotechnology Co., Ltd.) were dissolved in 50 ml of distilled water, and 50 ml of ethanol was added to obtain magnesium chloride mother solution (1). Take a 6% ammonia solution and place it in a closed hydrothermal reactor. Heat it to 100°C while stirring, keep the reactor constant temperature, then add the magnesium chloride mother solution (1) dropwise into the hydrothermal reactor through a high-pressure feed pump until the pH of the reaction solution is 10.0, stop dropping, keep stirring at 100°C for 1 hour, cool the reaction solution, filter, wash with distilled water, and dry the resulting product at 110°C to obtain a white powder. Use a transmission electron microscope (SEM) to observe the particle size and morphology of the sample. Figure 2 shows a 50,000-fold magnified photo of the magnesium hydroxide prepared in this example. The powder is a nano-scale hexagonal plate-like crystal with high purity (99.5%), good dispersion, and regular morphology. The crystal particle size is mainly distributed in the range of 200 to 300 nm, the crystal thickness is mainly distributed in the range of 100 to 150 nm, the specific surface area is 4 to 20 m2/g, the surface polarity is small, it is not easy to agglomerate, and the filtration is fast.
Example 4:
30.4845g magnesium chloride and 0.2145g PEG 6000 (Shanghai Zhuokang Biotechnology Co., Ltd.) were dissolved in 50ml distilled water, and 50ml ethanol was added to obtain magnesium chloride mother solution (1). A 6% ammonia solution was placed in a closed hydrothermal reactor, heated to 120°C under stirring, and the reactor was kept at a constant temperature. Then, the magnesium chloride mother solution (1) was added dropwise to the hydrothermal reactor through a high-pressure feed pump until the pH of the reaction solution reached 11.5, and then the addition was stopped. After stirring at a constant temperature of 120°C for 1 hour, the reaction solution was cooled, filtered, washed with distilled water, and the obtained product was dried at 110°C to obtain a white powder. The particle size and morphology of the sample were observed by transmission electron microscopy (SEM). FIG3 shows a 50,000-fold magnified photograph of the magnesium hydroxide prepared in this example. The powder is a nanoscale hexagonal plate-like crystal with high purity (99.5%), good dispersion, and regular morphology. The crystal particle size is mainly distributed in 100-150 nm, the crystal thickness is mainly distributed in 50-150 nm, the specific surface area is 4-20 m2/g, the surface polarity is small, it is not easy to agglomerate, and the filtration is fast.
Example 5:
30.4845 g of magnesium chloride and 0.2145 g of PEG 6000 (Shanghai Zhuokang Biotechnology Co., Ltd.) were dissolved in 50 ml of distilled water, and 50 ml of ethanol was added to obtain magnesium chloride mother solution (1). Take a 20% ammonia solution and place it in a closed hydrothermal reactor. Heat it to 140°C while stirring, keep the reactor constant temperature, and then add the magnesium chloride mother solution (1) to the hydrothermal reactor through a high-pressure feed pump until the pH of the reaction solution is 11.0, stop adding, keep the reaction solution constant at 140°C for 1 hour, cool the reaction solution, filter, wash with distilled water, and dry the resulting product at 110°C to obtain a white powder. The particle size and morphology of the sample were observed using a transmission electron microscope (SEM). The powder was a nanoscale hexagonal plate-like crystal with high purity (99.5%), good dispersion, and regular morphology. The crystal particle size was mainly distributed in the range of 200-300nm, the crystal thickness was mainly distributed in the range of 20-50nm, the specific surface area was 4-20m2/g, the surface polarity was small, it was not easy to agglomerate, and the filtration was fast.
Example 6:
30.4845g magnesium chloride and 0.2145g PEG 6000 (Shanghai Zhuokang Biotechnology Co., Ltd.) were dissolved in 50ml distilled water, and 50ml ethanol was added to obtain magnesium chloride mother solution (1). A 10% ammonia solution was placed in a closed hydrothermal reactor, heated to 200°C under stirring, and the reactor was kept at a constant temperature. Then, the magnesium chloride mother solution (1) was added dropwise to the hydrothermal reactor through a high-pressure feed pump until the pH of the reaction solution reached 9.0, and then the addition was stopped. After stirring at a constant temperature of 200°C for 1 hour, the reaction solution was cooled, filtered, washed with distilled water, and the obtained product was dried at 110°C to obtain a white powder. The particle size and morphology of the sample were observed by transmission electron microscopy (SEM). FIG. 4 is a 50,000-fold magnified photograph of the magnesium hydroxide prepared in this example. FIG. 5 is an X-ray powder diffraction pattern of the magnesium hydroxide prepared in this example. The powder is a nanometer-scale hexagonal flake crystal with high purity (99.5%), good dispersion, and regular morphology. The crystal particle size is mainly distributed in the range of 600 to 700 nm, the crystal thickness is mainly distributed in the range of 100 to 200 nm, the specific surface area is 4 to 20 m2/g, the surface polarity is small, it is not easy to agglomerate, and the filtration is fast.
Example 7:
30.4845g magnesium chloride and 0.2145g PEG 600 (Shanghai Kaibite Chemical Co., Ltd.) were dissolved in 80ml distilled water, and 20ml ethanol was added to obtain magnesium chloride mother solution (1). A 25% ammonia solution was placed in a closed hydrothermal reactor, heated to 100°C under stirring, and the reactor was kept at a constant temperature. Then, the magnesium chloride mother solution (1) was added dropwise to the hydrothermal reactor through a high-pressure feed pump until the pH of the reaction solution reached 9.5, and then the addition was stopped. After stirring at a constant temperature of 100°C for 1 hour, the reaction solution was cooled, filtered, washed with distilled water, and the obtained product was dried at 110°C to obtain a white powder. The particle size and morphology of the sample were observed by transmission electron microscopy (SEM). The powder was nanoscale hexagonal plate-like crystals with high purity (99.5%), good dispersion and regular morphology. The crystal particle size was mainly distributed in 150-200nm, the crystal thickness was mainly distributed in 50-100nm, the specific surface area was 4-20m2/g, the surface polarity was small, it was not easy to agglomerate, and the filtration was fast.
Example 8:
15.2425g magnesium chloride and 0.1072g PEG 2000 (Shanghai Kaibite Chemical Co., Ltd.) were dissolved in 50ml distilled water, and 50ml ethanol was added to obtain magnesium chloride mother liquor (1). Take a 3% ammonia solution and place it in a closed hydrothermal reactor. Heat it to 100°C while stirring, keep the reactor constant temperature, then add magnesium chloride mother solution (1) dropwise into the hydrothermal reactor through a high-pressure feed pump until the pH of the reaction solution is 9.5, stop dropping, keep stirring at 100°C for 1 hour, cool the reaction solution, filter, wash with distilled water, and dry the resulting product at 110°C to obtain a white powder. The particle size and morphology of the sample were observed by transmission electron microscopy (SEM). The powder was nanoscale hexagonal flake crystals with high purity (99.5%), good dispersion, and regular morphology. The crystal particle size was mainly distributed in the range of 150 to 200nm, the crystal thickness was mainly distributed in the range of 20 to 50nm, the specific surface area was 4 to 20m2/g, the surface polarity was small, it was not easy to agglomerate, and the filtration was fast.
Example 9:
30.4845g magnesium chloride and 0.2145g PEG 1000 (Shanghai Yangjie Trading Co., Ltd.) were dissolved in 50ml distilled water, and 50ml ethanol was added to obtain magnesium chloride mother solution (1). A 12% ammonia solution was placed in a closed hydrothermal reactor, heated to 100°C under stirring, and the reactor was kept at a constant temperature. Then, the magnesium chloride mother solution (1) was added dropwise to the hydrothermal reactor through a high-pressure feed pump until the pH of the reaction solution reached 9.5, and then the addition was stopped. After stirring at a constant temperature of 100°C for 1 hour, the reaction solution was cooled, filtered, washed with distilled water, and the obtained product was dried at 110°C to obtain a white powder. The particle size and morphology of the sample were observed using a transmission electron microscope (SEM). The powder was nanoscale hexagonal flake crystals with high purity (99.5%), good dispersion, and regular morphology. The crystal particle size was mainly distributed in the range of 100 to 200 nm, the crystal thickness was mainly distributed in the range of 100 to 200 nm, the specific surface area was 4 to 20 m2/g, the surface polarity was small, it was not easy to agglomerate, and it was filtered quickly.