Abstract
The present invention discloses a method for preparing magnesium carbonate, wherein food-grade magnesium sulfate and food-grade sodium carbonate are reacted to obtain magnesium carbonate at room temperature, and the magnesium carbonate is separated, washed, dehydrated and dried to obtain pure food-grade magnesium carbonate. The present invention has a simple process, is easy to control the operation, requires less raw materials, can significantly reduce production costs, and the product is food-grade magnesium carbonate.
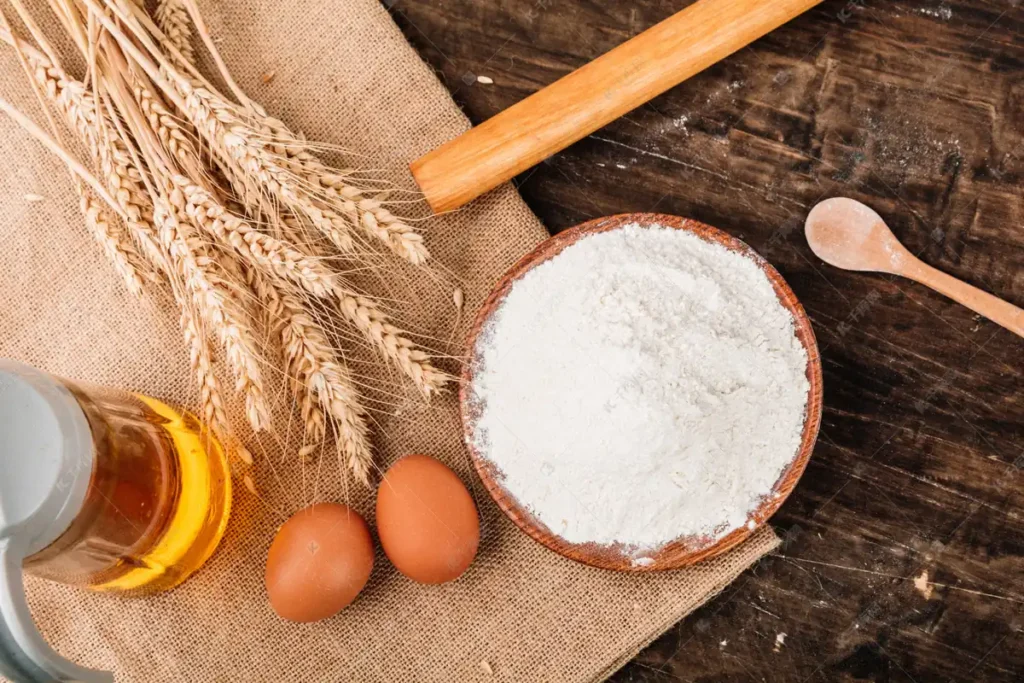
Background technology
In industrial production, due to different raw materials, there are usually four methods for producing light magnesium carbonate. One is the dolomite carbonization method, which is to calcine dolomite ore or magnesite with coal, and the clinker obtained after calcination is sent to a digester to be digested with waste magnesium water into an ash emulsion of a certain concentration. The ash emulsion is separated and deslagging and then sent to a carbonization tower to react with carbon dioxide in the kiln gas from the calcining kiln after washing and pressurization. The carbonized slurry after carbonization is qualified is separated and filtered to obtain filter residue and clear filtrate, i.e., magnesium water clear liquid. The heavy magnesium water clear liquid is pyrolyzed into a basic magnesium carbonate precipitate, which is separated and dehydrated, dried, and crushed to obtain a finished product. The second is the halogenation and carbonization method, that is, bittern is used as a raw material, and carbon dioxide, dolomite ash or lime produced after calcining dolomite or limestone is used as a raw material, and digestion, precipitation, carbonization, pyrolysis and other reactions are carried out to obtain light magnesium carbonate. The third is the brine soda method, that is, the bittern is diluted and then added to the soda ash solution, and the light magnesium carbonate product is obtained through filtering, washing, crushing, drying, crushing, air separation, packaging and other processes. The fourth is the brine-bicarbonate method, after the bittern is removed from the impurities, it is mixed with ammonium bicarbonate in an appropriate proportion, and a precipitation reaction is carried out, and then centrifugal dehydration, drying, and crushing are carried out to obtain light magnesium carbonate. At the same time, there is a small amount of sodium chloride and ammonium chloride in the mother liquor. Sodium chloride can be separated after filtration, and ammonium chloride can be recovered by crystallization after evaporation and cooling.
Content of the invention
The purpose of the present invention is to overcome the above problems existing in the prior art and provide a method for preparing magnesium carbonate with low process cost and simple process.
In order to achieve the above technical objectives and the above technical effects, the present invention is implemented by the following technical scheme:
A method for preparing magnesium carbonate, comprising the following steps:
Step 1) adding magnesium sulfate particles to sodium carbonate solution;
Step 2) obtaining magnesium carbonate precipitate and sodium sulfate solution after a period of reaction;
Step 3) filtering and separating the magnesium carbonate precipitate from the solution;
Step 4) washing the magnesium carbonate with distilled water for 2-4 times, and then drying it with a dryer to obtain pure magnesium carbonate, the mass ratio of magnesium sulfate to sodium carbonate being 1:1.
Further, in the step 1), the magnesium sulfate is selected from food grade magnesium sulfate, and the sodium carbonate is selected from food grade sodium carbonate.
Further, the reaction temperature in the step 2) is room temperature, and the reaction time is 30-45min.
Further, the drying temperature in the step 4) is 95-100°C, and the drying time is 1-1.5h.
Further, the magnesium carbonate obtained in the step 4) is food grade magnesium carbonate.
The beneficial effects of the present invention are:
The process of the present invention is simple, easy to control the operation, and the input of raw materials is small, which can greatly reduce the production cost, and the generated product is food-grade magnesium carbonate.
Specific implementation method
The present invention will be described in detail in combination with the embodiments below.
A method for preparing magnesium carbonate comprises the following steps:
Step 1) adding magnesium sulfate particles to sodium carbonate solution;
Step 2) obtaining magnesium carbonate precipitate and sodium sulfate solution after a period of reaction;
Step 3) filtering and separating the magnesium carbonate precipitate from the solution;
Step 4) washing the magnesium carbonate with distilled water for 2-4 times, and then drying it with a dryer to obtain pure magnesium carbonate.
Furthermore, in the step 1), the magnesium sulfate is selected from food-grade magnesium sulfate, and the sodium carbonate is selected from food-grade sodium carbonate, and the mass ratio of magnesium sulfate to sodium carbonate is 1:1.
Furthermore, the reaction temperature of the step 2) is room temperature, and the reaction time is 30-45min.
Furthermore, the drying temperature of the step 4) is 95-100℃, and the drying time is 1-1.5h.
Further, the magnesium carbonate obtained in step 4) is food grade magnesium carbonate.
Example 1
Take 0.5 mol of food grade magnesium sulfate particles and add them to 0.5 mol/L food grade sodium carbonate solution. After reacting at room temperature for 5 hours, magnesium carbonate precipitate and sodium sulfate solution are obtained. The magnesium carbonate precipitate is filtered and separated from the solution. The magnesium carbonate is washed with distilled water twice and dried in a dryer at 50°C for 1 hour to obtain pure magnesium carbonate.
Example 2
Take 0.5 mol of food grade magnesium sulfate particles and add them to 0.5 mol/L food grade sodium carbonate solution. After reacting at room temperature for 7.5 hours, magnesium carbonate precipitate and sodium sulfate solution are obtained. The magnesium carbonate precipitate is filtered and separated from the solution. The magnesium carbonate is washed with distilled water 3 times and dried in a dryer at 55°C for 1.2 hours to obtain pure magnesium carbonate.
Example 3
Take 0.5 mol of food-grade magnesium sulfate particles and add them to 0.5 mol/L of food-grade sodium carbonate solution. After reacting at room temperature for 10 hours, magnesium carbonate precipitate and sodium sulfate solution are obtained. The magnesium carbonate precipitate is filtered and separated from the solution. The magnesium carbonate is washed with distilled water 4 times and dried in a dryer at 60°C for 1.5 hours to obtain pure magnesium carbonate.
The above is only a preferred embodiment of the present invention and is not intended to limit the present invention. For those skilled in the art, the present invention may have various changes and variations. Any modifications, equivalent substitutions, improvements, etc. made within the spirit and principles of the present invention should be included in the scope of protection of the present invention.