The production method of magnesium carbonate varies according to the different raw material routes. There are usually the following: dolomite carbonization method, brine carbonization method, brine soda ash method, brine carbon ammonium method (or brine baking soda method), magnesite carbonization method, magnesia double decomposition method, asbestos tailings carbonization method. The following is a brief introduction.
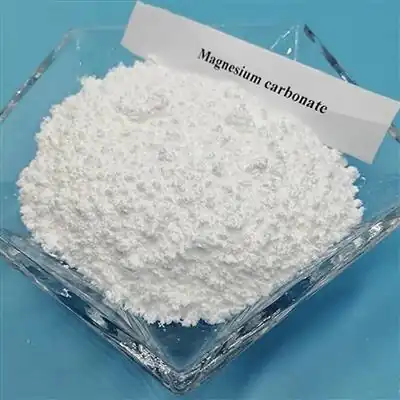
1. Brine carbonization method to produce magnesium carbonate
This production method uses brine, seawater and other magnesium chloride solutions and magnesium sulfate solutions as raw materials, and calcines with dolomite or limestone to produce CO2, and uses dolomite ash or lime as raw materials to produce light magnesium carbonate through digestion, deep precipitation, carbonization, pyrolysis and other reactions. Dolomite or limestone is calcined, digested and absorbed with water, and then reacts with brine. The production process is to precipitate magnesium hydroxide, and then carbonize, pyrolyze, wash, dehydrate, dry and crush to produce light magnesium carbonate products.
2. Magnesium carbonate production by ore carbonization method
Magnesite with a particle size of 100-300mm and white coal with a calorific value of 20000-25000kJ/kg are added into the kiln from the top of the vertical kiln in a ratio of (7-10):1. The temperature of the preheating section in the vertical kiln is controlled at 200-250℃, the temperature of the calcining section is controlled at 700-800℃, and the temperature of the cooling section is controlled at 100-150℃. The magnesite is calcined, and kiln gas with a CO2 concentration of more than 28% is drawn out from the kiln top; lightly burned magnesia with good activity is obtained from the bottom of the kiln. The magnesia is crushed and digested and absorbed with hot water to generate Mg(OH)2, which is then carbonated with CO2 in the purified kiln gas in the carbonization tower to generate magnesium bicarbonate. Light magnesium carbonate is obtained through sedimentation, separation, pyrolysis, filtration, and drying.
This method is the same as the dolomite carbonization method for producing magnesium compounds, but because the calcium content of magnesite is low, there is no need to set up a magnesium-containing calcium carbonate recovery system. At the same time, the calcium content in the product light magnesium carbonate is low, so the product quality of this method is better, the product cost is lower, the investment is low, and it is competitive. It is an emerging process that has attracted the attention of peers.
3. Asbestos tailings carbonization method for producing magnesium carbonate
The chemical composition of asbestos tailings is basically the same as that of dolomite. The difference is that the calcium-magnesium ratio is different due to different tailings. In some tailings, MgO≦20%, CaO≦29% and SiO2≧20%, and the ignition loss≦30%. Therefore, when using asbestos tailings as raw materials to produce light magnesium carbonate, the removal of hydrochloric acid solubles should be strengthened.
Applications of magnesium carbonate
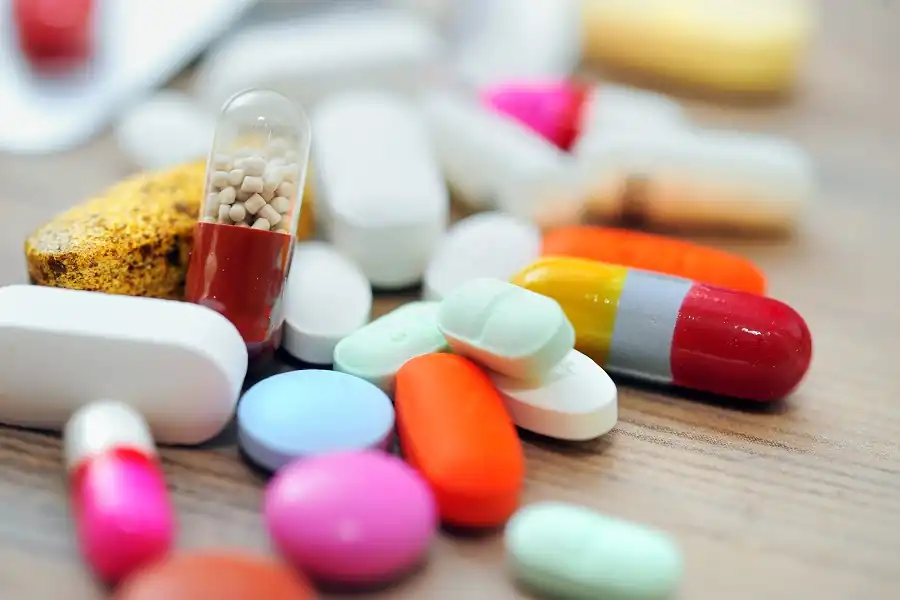
Application areas of magnesium carbonate: generally used as pharmaceutical intermediates, antacids, desiccants, color preservatives, carriers, anti-caking agents; used as additives and magnesium element compensators in food; used in the production of chemical reagents in fine chemicals; used as reinforcing agents and fillers in rubber; can be used as heat-insulating, high-temperature resistant fireproof and heat-insulating materials; important chemical raw materials in the manufacturing process of wires and cables. Manufacture of high-grade glass products; enamel ceramics for surface brightening; production of magnesium salts, pigments, paints, daily cosmetics, shipbuilding, boiler manufacturing.