Silicon steel grade magnesium oxide is a white powder with small particle size, good water suspension, low hydration rate and a certain particle size distribution range. Silicon steel grade magnesium oxide is mainly used to produce oriented silicon steel sheets. Its main function is to react with magnesium oxide and silicon steel sheets under high temperature to form a thin film. This film is orderly arranged and can reduce the reactive power loss of silicon steel sheets during operation. Silicon steel magnesium oxide is a high-temperature annealing isolation agent in the production of oriented silicon steel sheets. Transformer materials made of oriented silicon steel sheets have the special function of high energy saving. High-tech industries such as aviation manufacturing aircraft turbines and chips in mobile phones are all made of oriented silicon steel sheets. There is a broad development prospect and space in these fields.
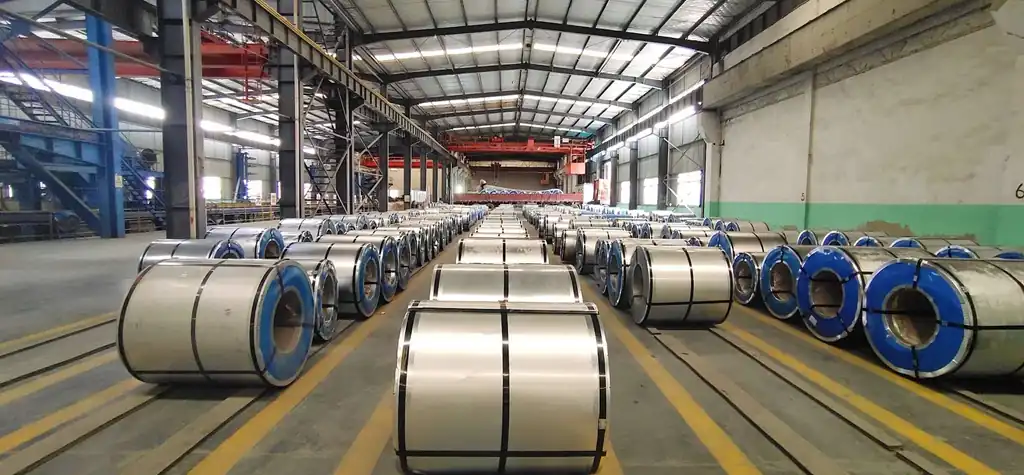
The silicon steel grade magnesium oxide produced by Messi Biology, a national high-tech enterprise, has obtained a national patent and can completely replace Japanese imported products, ranking among the top in the global industry. Messi Biology can improve the automation level of the production process by controlling the water used for hydration and improving the drying process. On the premise of ensuring that important indicators such as hydration rate do not change, the viscosity of silicon steel grade magnesium oxide is improved.
Messi Biology has optimized the analytical conditions of silicon steel grade magnesium oxide measured by laser particle size analyzer, such as dispersion medium, dispersion method, sample pretreatment, instrument dimness, etc., and explored a test method with good reproducibility in measuring the particle size range of silicon steel grade magnesium oxide, which meets the requirements of silicon steel production process control for magnesium oxide particle size.
Magnesium oxide coating for electrical steels and the method of coating.PDF
A preparation method of high viscosity silicon steel grade magnesium oxide, characterized by the following process steps:
(1) Add brine with a molar concentration of 1.5-2.5 molL (in terms of Mg2+) to the reactor, add ammonium bicarbonate under stirring at room temperature, the amount of ammonium bicarbonate added is 35 kg/m (in terms of brine), then add carbonated ammonia water (carbonization degree 40-60%) at a ratio of 1:6 to the volume of brine, continue to add ammonium bicarbonate 15 kg/m² (in terms of brine), stir continuously and raise the temperature to 40-50℃, make brine react with ammonium bicarbonate and carbonized ammonia water in a reactor for 1 to 1.5 hours; separate and dry to obtain magnesium compound;
(2) adopt dynamic calcination method to calcine the magnesium compound obtained in step (1), control the calcination temperature to 700 to 800℃, and the calcination time to 1 to 2.5 hours to obtain high-activity magnesium oxide powder;
(3) add the high-activity magnesium oxide obtained in step (2) into 80 to 90℃ pure water, hydrate for 1 to 2 hours, and then separate, wash and dry to obtain magnesium hydroxide.
(4) adopt dynamic calcination method to calcine the magnesium hydroxide obtained in step (3), control the calcination temperature to 900 to 980℃, and the calcination time to 2 to 4 hours to obtain magnesium oxide particles, and obtain high-viscosity silicon steel magnesium oxide after crushing, grading and packaging.
The specific technical scheme and its optimization conditions of the present invention are as follows:
Add brine with a molar concentration of 1.5-2.5 mol/L (in terms of Mg2+), preferably 2.0-2.5 mol/L, to the reactor; add 35 kg/m² (in terms of brine) of ammonium bicarbonate under normal temperature stirring, and then add carbonized ammonia water with a carbonization degree of 40-60%, preferably 45-55%, according to a volume ratio of 1:4-6 with the brine; continue to add 15 kg/m of ammonium bicarbonate (in terms of brine); continue to stir and heat to 40-60°C, the reaction time is 1-3 hours, preferably 45-55°C for 1-1.5 hours; separate, wash and dry to obtain magnesium compound; calcine at a temperature of 700-800°C for 1-2.5 hours, preferably calcine at 700-800°C for 1-2 hours; crush and classify. After the above process operation, high-activity magnesium oxide particles are obtained. When the active magnesium oxide is controlled to be hydrated at 80-90℃, it is best to stir, and the hydration time is 1-1.5 hours. Then separate, wash and dry to obtain magnesium hydroxide. Magnesium hydroxide is calcined at 900-980℃ for 3-4 hours to obtain magnesium oxide particles, which are crushed, screened and graded to obtain high-viscosity silicon steel magnesium oxide.
After the raw materials (brine, etc.) that meet the concentration enter the reactor, at a certain temperature, the reaction time is short, which will make the crystal particles fine, otherwise the particles will be too large. In order to make the precipitate crystal form meet the requirements of high activity, a certain concentration and temperature are controlled for reaction. If the concentration is too high, the impurity content is too high and it is not easy to wash. If the concentration is too low or the time is too long, the utilization rate is low, the crystal form is too complete, and it does not have the lattice defects required for high viscosity.
In order to achieve the purpose of low cost and high utilization rate, the separated filtrate can be recycled as washing water. Since the mother liquor has a certain temperature, the washing effect can be enhanced. The use of carbonized ammonia water can increase the utilization rate of ammonium bicarbonate and accelerate the conversion of magnesium bicarbonate into magnesium carbonate.
In order to reduce the adhesion and unevenness between particles during the firing of magnesium compounds, dynamic calcination can be used.
When hydrating high-activity magnesium oxide, the temperature needs to be maintained above 80°C, and the time can be shortened to control the particle size of magnesium hydroxide and better control the crystal form of magnesium hydroxide. Controlling the firing temperature can reduce the adhesion between particles and ensure the crystal defects and reasonable particle size distribution required for its high viscosity.
The characteristics of this method that are superior to other preparation methods are: reasonable design, efficient use of simple raw materials such as brine to produce high-activity oxides, and controlling the hydration of oxides at a certain temperature to generate magnesium hydroxide with a certain particle size distribution and crystal form, improving the firing and crushing process, and breaking through the previous silicon steel magnesium oxide viscosity range while ensuring that important indicators such as hydration rate do not change.
According to the preparation method of the present invention, high-viscosity silicon steel grade magnesium oxide with performance that fully meets the application requirements can be prepared, and due to the continuous implementation of each process, the stability of product performance can be guaranteed. The high-viscosity silicon steel grade magnesium oxide produced by the present invention can react with the silicon dioxide on the surface of the oriented silicon steel sheet to form a dense forsterite-type insulating film.
The present invention can solve the problem that the viscosity of traditional silicon steel grade magnesium oxide is relatively low (20-50cp), and cannot meet the production requirements of some silicon steel sheet factories for magnesium oxide viscosity above 80cp. The product prepared by the preparation method maintains the MgO content of the product above 98%, and the hydration rate and coating properties can still meet the requirements of silicon steel sheet production.