Magnesium hydroxide serves as the primary magnesium source in the production of magnesium taurate, where it reacts with tauric acid (an organic sulfonic acid) via a neutralization reaction to form the final product. This process is widely favored in industrial production—especially for high-purity magnesium taurate—due to its mild reaction conditions, high conversion efficiency, and simple byproducts (just water!).
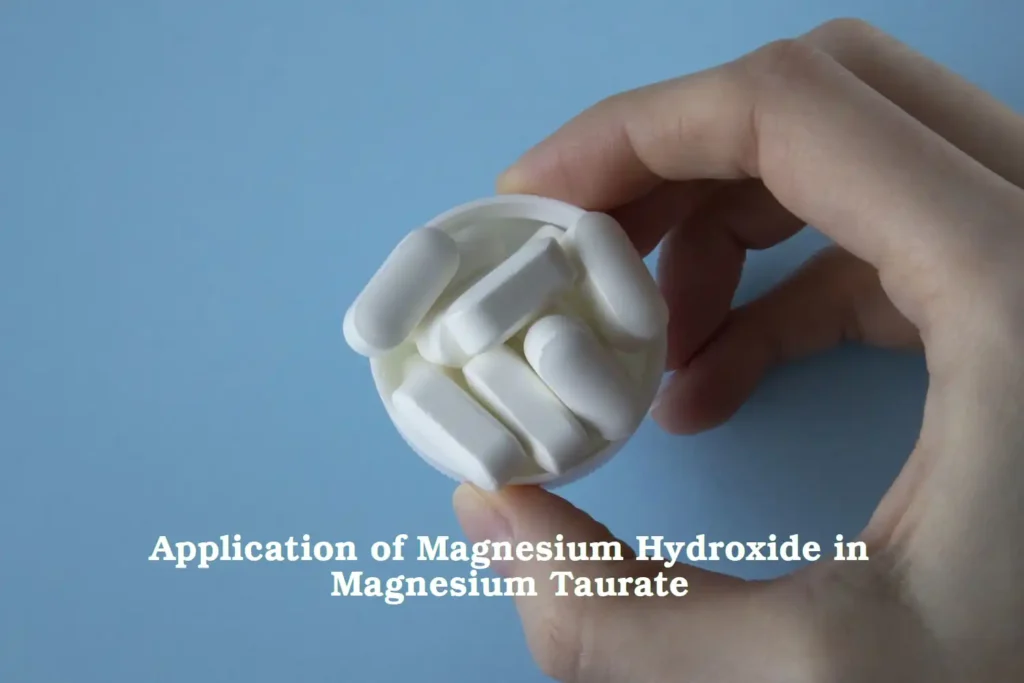
1. As a Reactant (Magnesium Source)
Magnesium taurate is a salt formed by the combination of tauric acid (with acidic properties) and magnesium ions. Its chemical formula is typically represented as:
Mg(C₂H₆NO₃S)₂** or **(HOOC-CH₂-CH₂-SO₃)₂Mg
Magnesium hydroxide, an inorganic base, has the chemical formula:
Mg(OH)₂
The core neutralization reaction is:
2HOOC-CH₂-CH₂-SO₃H + Mg(OH)₂ → (HOOC-CH₂-CH₂-SO₃)₂Mg + 2H₂O
Here, tauric acid provides the anionic component, while magnesium hydroxide supplies the magnesium cation, yielding magnesium taurate and water as the only byproduct.
2. Why Magnesium Hydroxide?
Several key advantages make magnesium hydroxide the preferred choice:
Mild Reaction: Compared to stronger bases like magnesium oxide (MgO), magnesium hydroxide reacts more gently, reducing risks of overheating or side reactions.
High Conversion Efficiency: Under optimized conditions (e.g., controlled temperature, stirring, and reaction time), it reacts fully with tauric acid.
High Purity: Food-grade or pharmaceutical-grade magnesium hydroxide has low impurity levels (e.g., heavy metals), crucial for high-end applications like health supplements or medicines.
Simple Byproducts: Only water is produced, simplifying post-processing (e.g., evaporation, crystallization, drying).
Wide Availability: It’s a common industrial raw material, easy to source.
Eco-Friendly: No harmful gases or hard-to-handle waste are generated.
3. Industrial Production Process
In practice, the production involves:
1. Mixing: Calculated molar ratios of tauric acid (usually in aqueous solution) and magnesium hydroxide (powder or suspension) are combined in a reactor.
2. Reaction Control: The mixture is gently heated (e.g., 60–80°C) with stirring to ensure thorough reaction. pH is monitored to confirm completion (theoretical endpoint: near-neutral or weakly alkaline, depending on tauric acid’s dissociation constant).
3. Post-Processing: The reaction solution is concentrated by evaporation, then cooled for crystallization (or spray-dried). Crystals are separated, washed to remove residual mother liquor, and dried to obtain the final product.