The application of magnesium oxide in aircraft runways is mainly reflected in its role as a vulcanization accelerator for fluororubber, which improves the runway’s resistance to high temperature, wear, oil and chemical media. Magnesium oxide mainly acts as a vulcanization accelerator in fluororubber, which can improve the product’s resistance to high temperature, wear, oil and corrosion by various chemicals.
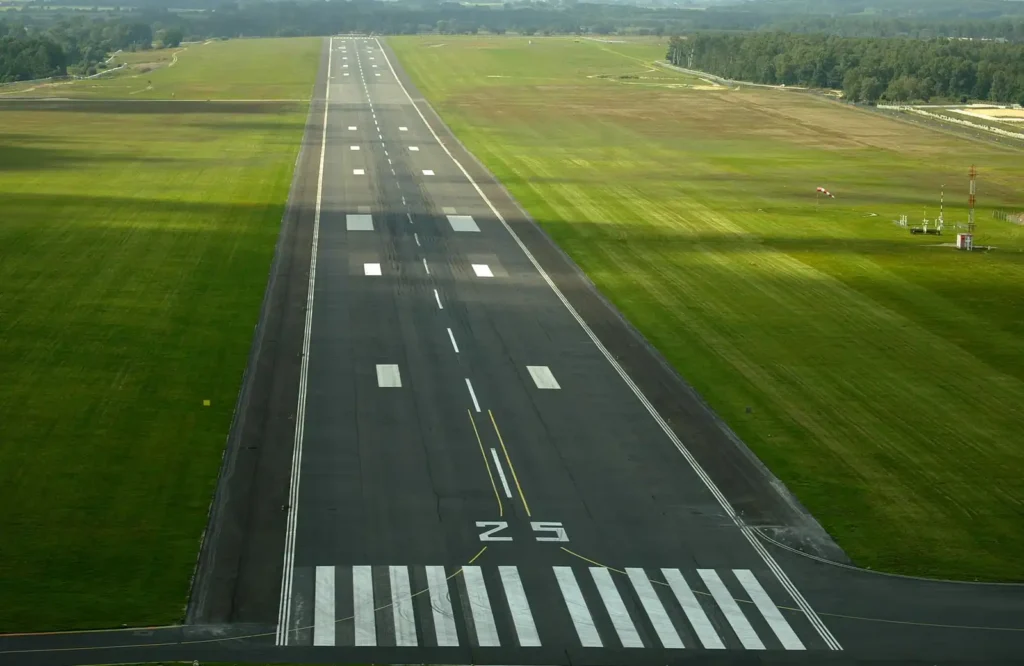
Specifically, there is a high-temperature and wear-resistant aircraft landing runway, which belongs to the application of fluororubber in the field of civil aviation. The main material is fluororubber, which is mixed with other raw materials through internal mixing and open mixing processes to prepare mixed rubber, and then vulcanized. The addition of magnesium oxide not only improves the mechanical properties of the runway, but also extends its service life. For example, the aircraft landing runway uses fluororubber with excellent mechanical properties, high temperature resistance and wear resistance as raw rubber, and adds highly wear-resistant graphene and nano zirconium dioxide. These materials, together with magnesium oxide, make the rubber have excellent high temperature resistance and wear resistance, thereby extending the service life of the runway.
In addition, magnesium oxide is also used in plastic runways. Although the question specifically refers to aircraft runways, the background information of plastic runways also helps to understand the wide application of magnesium oxide. Adding magnesium oxide to the silicon PU of plastic runways can play a role in anti-aging, absorbing carbon dioxide, preventing blistering, preventing precipitation and curing, extending the storage period, shortening the construction period and increasing the tensile strength. These characteristics make plastic runways more durable and safe, and also reflect the importance of magnesium oxide in similar applications.
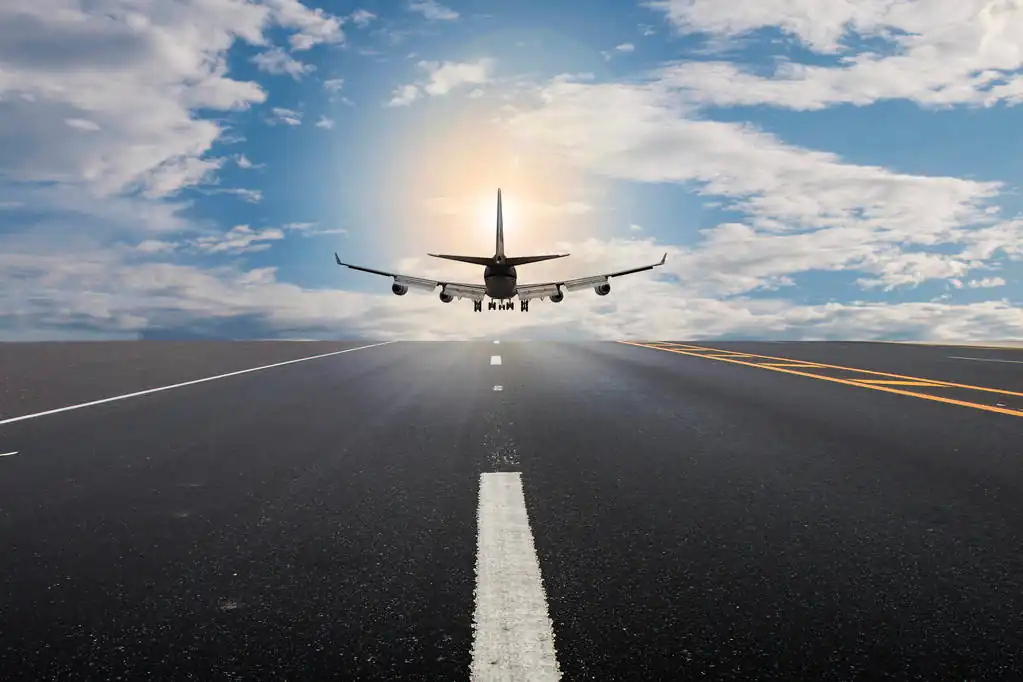