Messi Biology stated that magnesium oxide (MgO) plays several key roles in the synthesis and application of lithium magnesium silicate (usually refers to artificially synthesized hectorite or similar layered silicate materials). Magnesium oxide is not only a source of ingredients in lithium magnesium silicate, but also one of the key “levers” to regulate its final structure and performance.
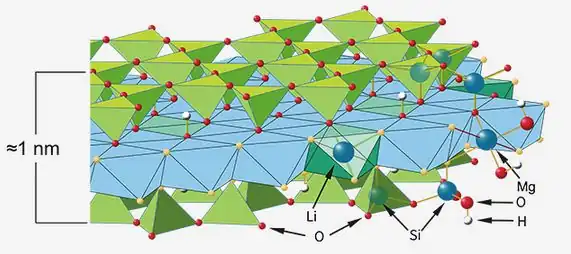
As a magnesium source
The basic chemical structural unit of lithium magnesium silicate requires magnesium ions (Mg²⁺). Magnesium oxide (MgO) is one of the main raw materials for providing magnesium in the synthesis process. In the synthesis reaction (usually high-temperature hydrothermal method), magnesium oxide dissolves or reacts to form magnesium ions, reacts with silicon sources (such as sodium silicate Na₂SiO₃), lithium sources (such as lithium carbonate Li₂CO₃ or lithium hydroxide LiOH) and possible other components (such as fluorine sources), and crystallizes to form layered lithium magnesium silicate crystals.
Adjusting the magnesium/silicon ratio
The Mg/Si ratio of lithium magnesium silicate is specific (for example, close to 5:8). Precise control of the amount of magnesium oxide in the reactants is essential to ensure that the final product has the correct stoichiometric ratio and crystal structure. The amount of magnesium oxide used directly affects the magnesium content in the synthetic product, which in turn affects its layer charge density, cation exchange capacity, swelling, rheology and other key properties.
Provide an alkaline environment
Magnesium oxide itself is alkaline, and reacts with water in the reaction system to form magnesium hydroxide (MgO+H₂O→Mg(OH)₂), which helps maintain the alkaline conditions required for the synthesis reaction. An alkaline environment is necessary for the dissolution and polymerization of silicate ions (SiO₄⁴⁻) and the ultimate combination with magnesium ions and lithium ions to form a stable layered silicate structure.
Impact on the performance of the final product
The amount and properties of magnesium oxide (such as purity, particle size, activity) will indirectly but significantly affect the performance of the synthesized lithium magnesium silicate product:
Layer charge density: Too little or too much magnesium oxide may lead to magnesium vacancies or insufficient magnesium substitution in the layer, changing the net negative charge density of the layer, directly affecting the cation exchange capacity and interaction with the polymer.
Crystal size and morphology: The reaction rate and solubility of magnesium oxide will affect the crystal nucleation and growth process, thereby affecting the size, shape and thickness of the final particles.
Purity: Impurities in magnesium oxide may be carried into the final product, affecting its color, transparency or specific application properties (such as biocompatibility, electrical properties).
Swelling and colloidal stability: The layer charge density is the core factor that determines the swelling ability of lithium magnesium silicate in water (forming a transparent “house of cards” gel) and colloidal stability. Improper magnesium oxide dosage will result in incomplete swelling or unstable gel.
Replacement of magnesium hydroxide
Sometimes magnesium hydroxide is directly used as a magnesium source. The advantages of magnesium oxide are:
No crystal water: MgO does not contain water, which is more direct in formula calculation.
Reactivity: The process of MgO reacting with water to generate Mg(OH)₂ is exothermic, which may help start the reaction or provide some energy. However, its reaction rate and solubility need to be controlled, and sometimes prehydration is required.
In the process of synthesizing lithium magnesium silicate, magnesium oxide (MgO) is an indispensable core raw material, and its main functions are: providing magnesium elements (Mg²⁺) necessary for forming the crystal skeleton. Accurately control the Mg/Si stoichiometric ratio in the product. Help maintain the alkaline environment required for the reaction. By accurately controlling the amount of MgO and selecting MgO of appropriate quality, the synthesis process can be optimized to produce lithium magnesium silicate products with key performance indicators such as specific layer charge density, crystal size, swelling, rheology and purity. These properties directly determine the application effect of lithium magnesium silicate in many fields (such as coatings, inks, cosmetics, drug carriers, drilling fluids, ceramics, polymer nanocomposites, etc.).