Messi Biology stated that magnesium oxide has certain application value in the polishing of special glasses, especially optical glasses. Its unique physicochemical properties make it improve efficiency and polishing quality during the polishing process of optical glass, and it has obvious advantages in some specific occasions. The following are the applications and functions of magnesium oxide in optical glass polishing:
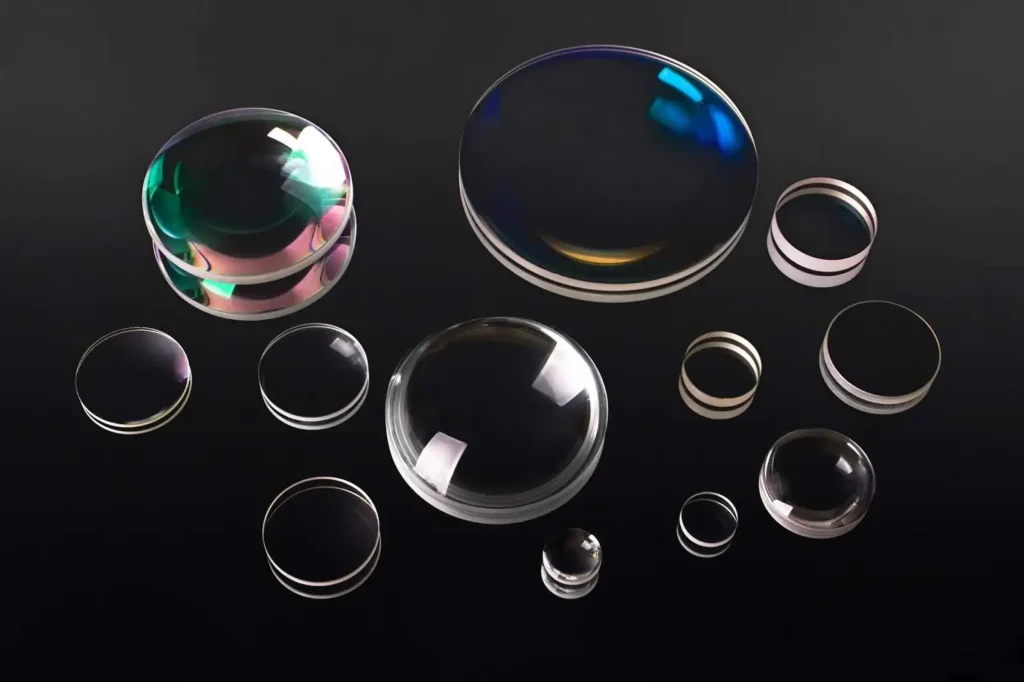
1. As a component of polishing powder
Magnesium oxide is often used as one of the components of optical glass polishing powder. During the optical glass polishing process, the polishing powder acts as an abrasive and is used to remove tiny irregularities and scratches on the glass surface. Magnesium oxide particles have appropriate hardness and chemical stability, which can effectively polish the glass surface and produce a smooth mirror effect.
Particle size control: The particle size of magnesium oxide powder can be adjusted to meet the polishing needs of different types of optical glass. Fineering magnesium oxide powders can produce high finishes, while coarse particles help remove larger defects.
Polishing rate control: The abrasive properties of magnesium oxide enable it to effectively remove substances on the glass surface under a certain pressure, which can not only control the polishing rate, but also avoid excessive damage to the glass surface.
2. Improve the smoothness of the glass surface
Another important role of magnesium oxide in optical glass polishing is to improve surface finish. In the optical industry, the surface finish of glass is crucial to imaging quality. Magnesium oxide can carefully polish the surface of optical glass, remove tiny scratches, particles and defects, and help the glass surface achieve a mirror effect.
Reduce scratches and tiny defects: Magnesium oxide, as a polishing medium, can reduce scratches and defects on the glass surface due to uneven abrasives or different hardness.
Improve finish: Magnesium oxide has high smoothness, which can produce very smooth surfaces, improving the light transmittance and imaging quality of the glass.
3. Combination of use with other abrasives
Magnesium oxide is sometimes used in combination with other abrasives (such as cerium oxide, alumina, etc.) to form a composite polishing material. The use of composite materials can optimize the polishing process, achieve higher polishing effects, and can meet the different needs of different types of optical glass.
Improve the polishing adaptability of various glasses: Different types of optical glass (such as lenses, optical fibers, flat glass, etc.) have different needs for polishing abrasives. By reasonably combining magnesium oxide and other abrasives, the polishing requirements of different optical glasses can be met. .
Enhanced abrasive effect: The combination of magnesium oxide and other abrasives can enhance the cutting ability of the polishing powder while maintaining a good surface finish and reducing thermal damage during the polishing process.
4. Provide thermal stability
Magnesium oxide has good thermal stability and can maintain its chemical stability and hardness at high temperatures, which makes it perform excellently in high-temperature polishing environments, especially during high-speed rotary polishing.
Adapt to high temperature environment: When working at high temperatures, optical glass polishing may cause some abrasive decomposition or performance degradation, while the thermal stability of magnesium oxide ensures its stability at high temperatures and ensures long-term efficient polishing effect.
5. Improve the chemical stability of glass
In the polishing process of certain optical glasses, the chemical inertia of magnesium oxide is also an important advantage. It can be polished efficiently without chemical reaction with the glass surface. The chemical stability of magnesium oxide can avoid unnecessary chemical damage to the glass surface during the polishing process, especially when fine polishing some special optical glasses, it can avoid surface corrosion or damage caused by chemical reactions.
6. Application in the formula of polishing liquid
Magnesium oxide can also be used in the formulation of optical glass polishing liquids as one of the auxiliary components. Magnesium oxide in the polishing liquid can help improve the lubricity of the polishing process, reduce the friction heat when the abrasive is in direct contact with the glass surface, and reduce the temperature rise caused by friction of the glass.
Enhanced lubricity: Magnesium oxide, as an additive in polishing liquid, can increase the viscosity of the liquid, provide better lubrication, and reduce thermal damage to the glass surface.
Reduce pollution: The use of magnesium oxide can help reduce the impact of possible contaminants on the glass surface during polishing and maintain the high purity of the glass.
7. Controllable surface microstructure
Polishing of optical glass is not only for the purpose of obtaining a smooth mirror, but also requires ensuring uniformity of the surface microstructure. Due to its good control performance, magnesium oxide can achieve a more uniform microstructure on the glass surface, thereby improving the imaging quality of the optical element.