Selective Catalytic Reduction (SCR) systems
For power plants and industrial companies using Selective Catalytic Reduction (SCR) systems to control backend boiler emissions. UtiliMag H, a high-purity magnesium hydroxide slurry and UtiliMag 40, a high-purity magnesium oxide (MgO) powder, can be used to significantly reduce sulfur trioxide (SO3) generated by the boiler, and SCR unit as well as opacity emissions and acid plumes related to SO3. UtiliMag H can be added from the superheater section to the SCR outlet for SO3 control or to reduce opacity.
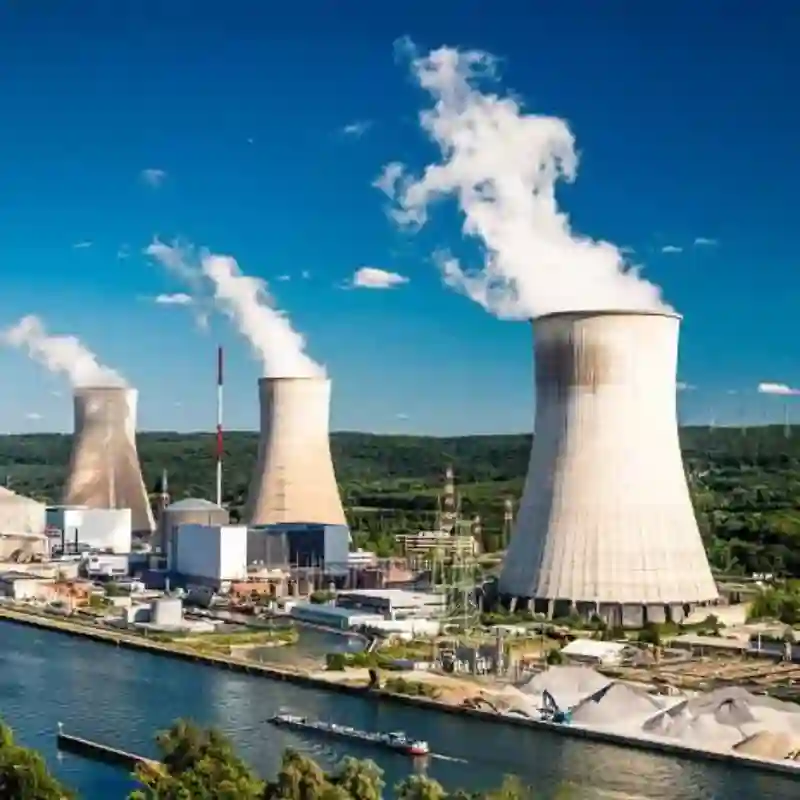
Magnesium Oxide for Power Plants
UtiliMag H is also effective in neutralizing acidic solutions generated from wet electrostatic precipitators (WESP) and SO2 from flue gas desulfurization (FGD) scrubbers. UtiliMag 40 can be injected downstream of the SCR to the air heater inlet for effective SO3 removal, corrosion control and opacity treatment. Backend treatment with UtiliMag 40 can also reduce the formation of ammonium bisulfate in the air heater, resulting in less frequent, easier cleanup and elimination of corrosion.
Boiler Additives | Power Plants
The use of boilers to generate utility hot water or steam for industrial processes is widespread. Typical examples are energy plants (i.e., power generation) which utilize boilers to generate steam. And the steam is used to drive steam turbines and produce electricity. However, the combustion of fuel oils and coal in such boilers is associated with corrosive combustion by-products creating the so-called hot and cold-end corrosion.
Cold and Hot Corrosion
Such fuels are rich in sulfur and combustion will generate SO3 that will convert to sulfuric acid (H2SO4) which damages metal surfaces. This type of corrosion is usually called cold or low-temperature or cold-end corrosion. Fuel oils also contain Vanadium (V) and sodium (Na). Upon combustion, these impurities react to form sodium vanadates (Na2O·xV2O5), a component of the fuel ash or soot.
These vanadates are low melting point phases and at high temperatures deposit and stick onto the equipment internal surfaces (slag formation). Being potent corrosives, they cause significant damage to the metal surfaces. This type of corrosion is usually called high-temperature or hot corrosion.
Fine and reactive magnesium oxide powders or special suspensions of said MgOs in organic mediums can be used under several circumstances as detergents or scavengers to mitigate corrosion problems:
For cold-end corrosion:
MgO based slurries or powders can be injected directly in the flue gas stream at a point between the economizer outlet and the combustion air preheater of the boiler. MgO will take part in the following acid neutralization reactions:
MgO + SO3 → MgSO4
MgO + H2SO4 → MgSO4 + H2O
For hot corrosion:
MgO based slurries or powders can be injected via existing soot blowers with some modifications. Powders can also be fed together with the coal in coal fired boilers. The basic scavenging reaction here is:
MgO + V2O5 → 3MgO·V2O5
The magnesium orthovanadate formed has a significantly higher melting point than sodium vanadate which means that it has a lower tendency to deposit, it is looser, powdery and easier to remove.
Our sales engineers and R&D teams can provide testing and develop straightforward solutions for your boiler corrosion challenges. Just get in touch with us!