In recent years, the fire accident caused by polymer has attracted great attention from all walks of life, and the research and development of flame retardant high clusters has become a hot spot. At present, the organic flame retardant used in the market has a large amount of smoke and toxic smoke, which has been limited by the laws of Europe, the United States, Japan, and my country. Therefore, inorganic flame retardants have received great attention. The inorganic flame retardant has received great attention.
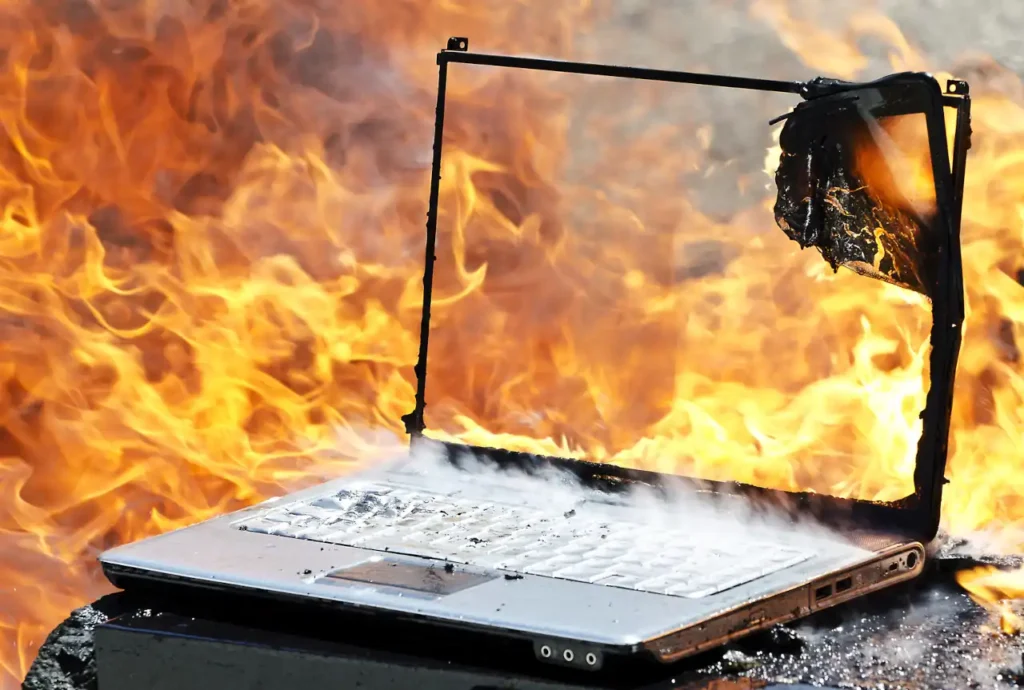
Magnesium hydroxide flame retardant decomposition temperature (340 ℃ ~ 450 ℃), thermal decomposition products are MgO and H2O, no toxic and harmful substances are released, and there is no harm to environmental and human health. Therefore, magnesium hydroxide flame retardant becomes becoming , Magnesium hydroxide flame retardant has become one of the most watched inorganic flame retardants at present, with broad application prospects. , With a broad application prospect.
The flame retardant of magnesium hydroxide oxide
Magnesium hydroxide has a special layered structure, making it present excellent tactile and low surface energy, and has good flame retardant and smoking effects on plastic. Magnesium hydroxide at 340 ° C began to be heated and decomposed into magnesium oxide and water. The temperature can be as high as 490 ° C when fully decomposed, and a large amount of thermal energy can be absorbed during decomposition. The specific flame retardant mechanism is:
(1) Magnesium hydroxide has a large heating capacity. When heating and decomposition, a large amount of heat is absorbed, and a large amount of water vapor is released at the same time, which not only reduces the temperature of the material surface, but also reduces the production of combustible small molecules.
(2) A large amount of water vapor can also cover the surface of the material to reduce the surface of the water, reducing the oxygen concentration in the burning surface air, thereby hindering the burning of the material.
(3) Magnesium oxide generated by magnesium hydroxide is a good refractory material. It can not only cover the surface of the material, but also promote the carbonization of polymer materials, form a carbonized layer to block the entry of heat and air, and effectively prevent burning.
(4) Magnesium hydroxide has the effect of oxidation and reduction reaction catalyst, which can promote the transformation of CO during the combustion process to CO2; the decomposition of magnesium oxide can neutralize the SO2, CO2 and NO2 generated during the combustion process, thereby reducing the release of toxic and harmful gases Essence
Preparation of magnesium hydroxide flame retardant
1. Physical crushing method
The physical crushing method is to use mechanical or ultrasonic methods to crush and crush natural minerals (mostly magnesium stones) to obtain magnesium hydroxide in the required particle size range. Although the magnesium hydroxide of the physical crushing method is simple and the cost is low, the prepared magnesium hydroxide purification is low and the particle size distribution is usually used. Generally, a special grinding method is required or the abrasives (or decentralized agent or decentralized agent are added during grinding. ) Obtain high -quality magnesium hydroxide. As a result, its industrial application and development have been greatly restricted.
2. Chemical solid phase method
Magnesium hydroxide is magnesium hydroxide is a solid metal salt and metal hydroxide mixing according to a certain proportion. After grinding and burning, the solid reaction occurs to obtain the product of magnesium hydroxide products. This method has the characteristics of simple craftsmanship and low cost, but there are also defects such as low product purity, easy reunion, and poor decentralization performance. It has less applications in actual large -scale industrialized production.
3. Chemical qi phase method
Magnesium -hydroxide hydroxide is ammonia as a precipitation, and the ammonia gas is directly transmitted to the Mg2+solution to make magnesium hydroxide. The quality of magnesium hydroxide is affected by ammonia flow, stirring strength, and reaction temperature of ammonia, and its quality. Due to the stable ammonia concentration during the process of air -based legal hydrogen oxide flame retardant, the products made have the advantages of high purity, uniform particle size, and good decentralization performance. At the same time The concentration of magnesium oxidation is high, the area is small during the production process, and the unit has a high production rate. However, the requirements for equipment and technology are high, and it is also prone to the problem of ammonia gas diffusion pollution.
4. Chemical fluid phase method
Magnesium hydroxide is magnesium salt as the main raw material, which reacts with alkaline substances with hydroxide root ions (OH–), generates magnesium hydroxide precipitation, and then obtains products through washing and drying. The liquid phase method can be divided into direct precipitation method, solvent thermal and water heat method, precipitation-covalent distillation method, ultrasonic chemical method and microwave assistance method.
(1) Direct precipitation method
Direct precipitation method is also called alkaline method. It is a method for reacting magnesium solution directly with alkaline precipitant or precipitant front drive reaction to generate magnesium hydroxide. According to the different types of sediment, it can be divided into lime, ammonia, and sodium hydroxide. Method and calcium hydroxide method. The direct precipitation method is simple and easy to run, and the equipment and technical requirements are low and it is not easy to produce impurities, but its reaction conditions affect the performance of the final product. The concentration of raw materials, reaction time, temperature, stirring rate, etc. are all current research. The focus.
(2) Solvent heat and water heat method
Solvent thermal and hydrophilic method is a chemical synthesis method that is easy to control the size and decentralization of magnesium hydroxide. This method changed the properties of magnesium hydroxide under high temperature and high pressure. In the raw materials, magnesium salts and alkaline substances fully react and crystallize, forming magnesium hydroxide with more uniform granules and more decentralized. The current research on solvent heat and water heat method is mainly focused on improving the performance of magnesium hydroxide products, such as adding different types of organic solvents or additives, reasonable adjustment of chemical reaction time, and reaction temperature.
(3) Precipitation-Co-boiling distillation method
Settlement-covalent distillation method can improve the phenomenon of reunion in the process of conventional preparing magnesium oxide. The principle is that the general sediment particles are full of water molecules. Direct drying can easily cause the particles to produce hard reunion under the pressure of the capillary tube. The boiling distillation method forms a co -boiling object at a certain temperature by using organic matter and water such as alcohol, thereby using hydrogen to hydrogen hydrogen, so as The moisture in magnesium oxide gum is removed, which improves its decentralization and obtains the products with good decentralization performance.
(4) Ultrasonic chemistry method and microwave assistance method
Ultrasonic chemistry method and microwave assistance method belong to the new type of magnesium hydroxide flame retardant preparation process. The ultrasonic chemical method is a chemical reaction caused by ultrasonic chemistry. The activity site is generated to enhance the chemical response rate and ensure that the appearance of magnesium hydroxide particles is more uniform and uniform. The study of this method mainly focuses on the comprehensive advantages of ultrasonic chemicals, such as ultrasonic chemicals, and other aspects of ultrasonic power and product performance. Ultrasonic chemical method does not need to perform pressure control of the reaction process. The comprehensive response speed is faster, the reaction temperature is relatively low, and process control is more advantageous.
Microwave technology is used to prepare magnesium hydroxide, and the energy consumption is relatively small and will not cause serious pollution to the environment. At the same time, the microwave auxiliary method can effectively shorten the chemical reaction time of magnesium hydroxide, and make the sample solution in the interior of a more uniform high temperature state. The microwave auxiliary method can be combined with the water thermal method, etc., and further explores the new methods and deep application value prepared by magnesium hydroxide flame retardants.
Requirements for the application of magnesium hydroxide flame retardant materials
Magnesium hydroxide hydroxide as a flame retardant has the following requirements:
(1) It must have extremely high purity (Mg(OH)2> 93%). Magnesium hydroxide with high purity not only has high flame retardant performance, but also reduces its addition in the material.
(2) Small particle size, composite materials prepated with micr -nano -grade magnesium hydroxide in all aspects (including flame retardant effects, smoke elimination and mechanical properties, etc.) are far better than micron -level magnesium hydroxide.
(3) When the surface polarity is low, when the surface polarity of magnesium hydroxide is reduced, the degree of agglomeration will be reduced, and the dispersability and compatibility increase. Sexual impact on the mechanical performance of materials.
Reasons for modification of magnesium hydroxide flame retardant materials
At present, most of the flames of magnesium hydroxide hydroxide in the market are micron levels (D> 5 μm), and the particle size is widely distributed, and it is necessary to fill in large quantities in the application. In addition Molecular polymers are not compatible. In actual application, magnesium hydroxide has caused serious damage to the mechanical properties of polymer polymer materials, which greatly limits the application of magnesium hydroxide flame retardants.
Through a certain physical and chemical method, the surface polarity is low, the hydrophilicity, the small particle size and the narrow distribution, and the magnesium hydroxide flame retardant compatible with the polymer polymer has become a hot spot for the current research of science and technology workers. Essence
On the one hand, the use of organic officials can reduce the polarity of the surface of magnesium hydroxide on the surface of magnesium hydroxide, and improve the compatibility of its polymer polymer; The composite material performance is good.
On the other hand, the performance of magnesium hydroxide -hydroxide flame -retardant performance of micro -nano -grade is several times higher than that of micron -level magnesium hydroxide, and it has a lower impact on polymer polymer materials. Micro -nano -grade magnesium hydroxide with low polarity can be evenly scattered in the polymer polymer material, so that the flame retardant performance and mechanical performance of the entire material can be consistent. Therefore, the surface modification and superfractory of magnesium hydroxide flame retardants can solve the disadvantages of the application of magnesium hydroxide flame retardants.
Research on surface modification of magnesium hydroxide hydroxide
Magnesium hydroxide, as a flame retardant for polymer polymers, is the most important thing is to be well compatible with the polymer polymer, realize uniform dispersing, and finally achieve the purpose of flame retardant. The use of specific compounds on the surface modification of magnesium hydroxide can reduce the surface polarity of magnesium hydroxide, make the surface of its surface have hydrophobicity, and improve the compatibility of magnesium hydroxide and polymers.
Magic hydroxide surface chemical modification is to use chemical methods to selectively adsorb or specific adsorption or chemical reactions on the surface of magnesium hydroxide powder on the surface of magnesium hydroxide powder, so as to cover the surface of the particles and make the particles surface so that to make the surface of the particles and make the surface of the particles so that to make the particles surface make the particles surface, so that the surface of the particles is covered to make the particles surface, so that the surface of the particles is covered to make the particles surface, so that the surface of the particles is covered to make the particles surface, so as The surface of the particles is organic or changes to polarity, and the surface modification is finally achieved. Commonly used surface modifiers mainly include Silicane coupling agents and titanate, aluminate coupling agent and high -grade fatty acids and their derivatives.
The physical modification of magnesium hydroxide usually has surface high -energy modification and surface overwriting. The surface high -energy modification mainly modified Mg(OH)2 through radiation and other methods to change the surface activity of Mg(OH)2. The process of modification does not involve chemical reactions. The surface overwriting is mainly modified by the decentralized agent to Mg(OH)2.
Research on ultrafine magnesium hydroxide
Hyperfinesis is one of the ways to enhance magnesium hydroxide and polymer compatibility and reduce the effectiveness of filling. The preparation process has a decisive effect on the particle size, particle size distribution, and appearance of the final appearance of magnesium hydroxide hydroxide. It is the most effective method for obtaining super fine -grade magnesium hydroxide by changing the preparation process.
The solvent thermal and water thermal method, microwave auxiliary method and ultrasonic chemistry method have been verified in the preparation of microfanan -level materials, and some research reports have also been made in the preparation of super fine -grade magnesium hydroxide flame retardant materials.
summary
In the past two decades, research on magnesium hydroxide modification and super fine preparation has made great progress. The non -toxicity, extensive source, and low price of magnesium hydroxide are the biggest advantage of the material as a flame retardant. With the enhancement of environmental protection, the application of magnesium hydroxide in the material in flame retardant materials will continue to increase, realizing the surface modification and superfractory preparation of magnesium hydroxide flame retardant It is of great significance.