The dispersion mechanism of nano magnesium hydroxide in rubber mainly involves the viscosity and surface energy of the matrix, which are closely related to the dispersion state and network structure formation of nano magnesium hydroxide powder.
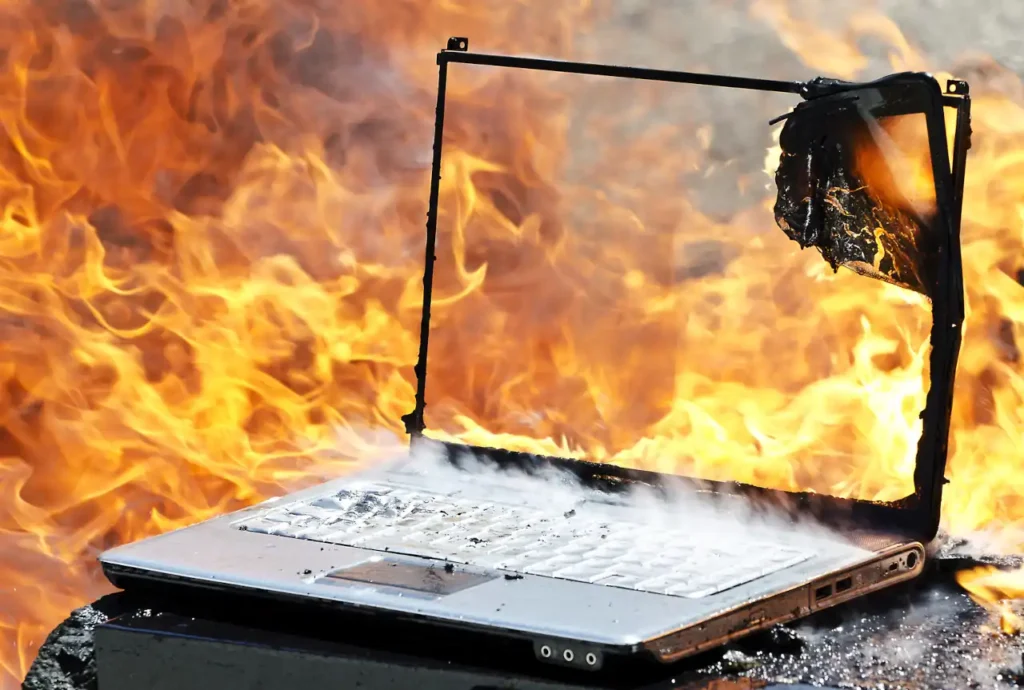
As a new type of flame retardant, nano magnesium hydroxide is widely used in rubber, and its dispersion characteristics and dispersion mechanism are crucial to improving the performance of rubber composites. Research shows that the viscosity and surface energy of the matrix have a decisive influence on the final dispersion state and network structure of nano magnesium hydroxide powder. Specifically, when the viscosity and surface energy of the matrix are high (such as nitrile rubber and EPDM rubber), nano magnesium hydroxide powder can be more finely dispersed and easily form a flexible network structure, and the polymer participation ratio is large. On the contrary, in a matrix with low viscosity and low surface energy (such as silicone rubber), nano magnesium hydroxide powder exists in the form of isolated large aggregates, and cannot form a network structure even at a low filling amount, but at a high filling amount, these large aggregates can be directly connected to form a network structure with higher rigidity, and the polymer participates less in the formation of the network structure.
In addition, the study also proposed a revised model, which introduced the influence of surface energy factors, in order to more comprehensively consider the influence of various main factors on the external forces exerted on powder aggregates. This revised model can better explain the experimental results, indicating that the dispersion mechanism of nano-magnesium hydroxide in rubber and its influence on the performance of composite materials is a complex process involving the interaction of multiple physical and chemical factors.
In summary, the dispersion mechanism of nano-magnesium hydroxide in rubber and its influence on the performance of composite materials is a multi-factor process, in which the viscosity and surface energy of the matrix are the key factors affecting the dispersion state and network structure formation. By in-depth study of these mechanisms, theoretical guidance can be provided for optimizing the application of nano-magnesium hydroxide in rubber, thereby improving the overall performance of composite materials.