At present, graphite crucibles are commonly used for smelting rare metals. However, during the high-temperature smelting process, the inner wall of the crucible is easy to fall off and enter the rare metal, affecting the quality of the metal and making it difficult to meet the requirements of actual production. Magnesium oxide has a melting point of 2800℃, excellent mechanical properties, and stable chemical properties. Therefore, magnesium oxide ceramic crucibles have excellent chemical stability, oxidation resistance, and resistance to molten metal corrosion. In recent years, they have been valued in the smelting of rare metals.
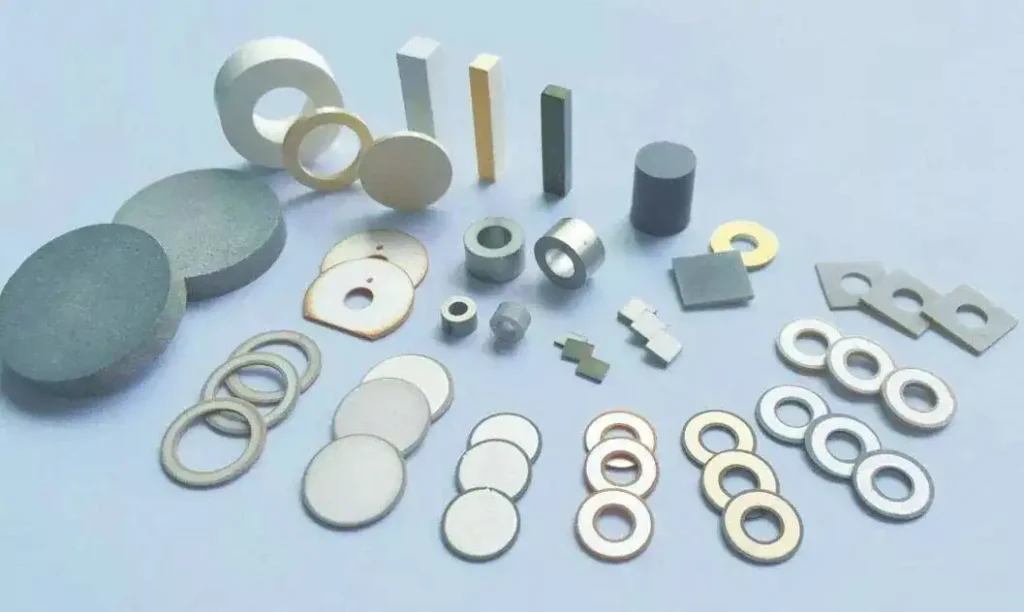
In addition, magnesium oxide ceramics are also transparent ceramic materials, foam ceramic filter materials, microwave dielectric ceramic materials, and ceramic core materials with excellent performance.
The only drawback is that the thermal expansion coefficient of magnesium oxide is large ((13~15)×10-6℃), resulting in poor thermal shock resistance.
Therefore, improving the high-temperature performance of magnesium oxide ceramics, especially thermal shock resistance, is a technical bottleneck that needs to be solved to further expand the application of magnesium oxide.
Rare earth oxides as additives
The most commonly used measure to improve the poor thermal shock resistance of magnesium oxide ceramics is to add additives.
As a common additive, rare earth oxides have the advantages of high stability, low volatility at high temperatures, high melting and boiling points, etc. They can greatly improve the strength and toughness of ceramic materials, and can reduce the sintering temperature and production costs, so they are widely used in the production of ceramic materials. In addition, rare earth oxides are mainly distributed at the grain boundaries of ceramics, thereby hindering grain growth and refining grains, which is conducive to the formation of dense structures.
Nd2O3
Di Yuli et al. prepared magnesium oxide ceramics using micron-level lightweight magnesium oxide powder as the main raw material, Nd2O3 as an additive, and polyvinyl alcohol as a binder. The results show that the optimal sintering conditions for magnesium oxide ceramics are a pressing pressure of 242MPa and a sintering temperature of 1580℃; when the addition of Nd2O3 is 8%, the sintering performance of magnesium oxide is the best, and when the addition is 4%, the number of thermal shock resistance of magnesium oxide ceramics is as high as 16 times.
Y2O3
Rare earth oxide Y2O3 has a high melting point, high electric charge, large radius, strong polarization ability, and active chemical properties. It is often used to improve the microstructure of materials and improve the high-temperature performance of materials.
Xue Zongwei et al. prepared magnesium oxide ceramic samples with high-purity nano-magnesium oxide as the main raw material and high-purity nano-Y2O3 powder as an additive, and studied the effects of yttrium oxide addition (external addition, mass fraction of 0, 1%, 2%, 3% and 4%) and calcination temperature (1350℃, 1450℃ and 1550℃) on the properties of magnesium oxide ceramics. The results show that: Y2O3 forms a limited substitutional solid solution with periclase, which improves the density of the sintered sample; Y2O3 inhibits the growth of periclase grains in the sintered sample; Y2O3 improves the thermal shock resistance of magnesium oxide ceramics through second phase toughening and microcrack toughening.
La2O3
La2O3, as a rare earth oxide, can form a solid solution with other ceramic raw materials, causing crystal defects inside, activating the lattice, and promoting the sintering of ceramic materials.
Yu Yin et al. prepared magnesium oxide ceramics using nano-magnesium oxide as the main raw material and La2O3 as an additive. The results show that after La2O3 is added, it can form a solid solution and some amorphous substances with magnesium oxide, which are evenly distributed at the grain boundaries, slowing down the tip stress of the crack during thermal shock, hindering the extension of the crack, and effectively improving the thermal shock stability of magnesium oxide ceramics.
CeO2
Zheng Bo et al. used lightweight magnesium oxide powder as raw material, rare earth CeO2 as additive, polyvinyl alcohol as binder, and prepared magnesium oxide ceramics by atmospheric pressure sintering. The changes in ceramic sintering properties and thermal shock resistance were studied. After determining the optimal sintering conditions for magnesium oxide ceramics, different contents of rare earth CeO2 were added to prepare magnesium oxide ceramics, and the thermal shock resistance of the ceramics was greatly improved.
ZrO2 as an additive
Since ZrO2 undergoes a martensitic phase transformation (t-ZrO2 to m-ZrO2) accompanied by changes in volume and shape, it can absorb energy, slow down the stress concentration at the crack tip, prevent crack expansion, and improve the toughness of ceramics. Many studies have shown that the addition of ZrO2 can improve the thermal shock resistance or sintering performance of magnesium materials.
Zhao Zhipeng et al. used high-purity magnesium oxide powder as the main raw material, added 14% (ω) of m-ZrO2 nanopowder, t-ZrO2 nanopowder, and c-ZrO2 nanopowder as additives, prepared magnesium oxide ceramic samples through batching, molding, and sintering at 1550℃ for 2h, and studied the effects of adding different crystal forms of ZrO2 nanopowder on the sintering and thermal shock resistance of magnesium oxide ceramics. The results show that the added ZrO2 is dispersed at the grain boundaries of periclase, which improves the density of the sample; in the sample with m-ZrO2, ZrO2 and MgO form a solid solution, activate the lattice of periclase crystals, greatly promote the sintering of the sample, and ZrO2 improves the thermal shock resistance by a composite toughening mechanism of phase transformation toughening and second phase toughening. In the samples with t-ZrO2 and c-ZrO2, ZrO2 improves the thermal shock resistance by a second phase toughening mechanism.
Al2O3 as an additive
According to the binary equilibrium phase diagram of Al2O3 and MgO, Al2O3 and MgO generate magnesium aluminum spinel (MgAl2O4) materials with high melting point, small thermal expansion, low thermal conductivity, good thermal shock stability and strong slag corrosion resistance at 1000℃, which has a positive effect on improving the strength and thermal shock resistance of ceramic materials.
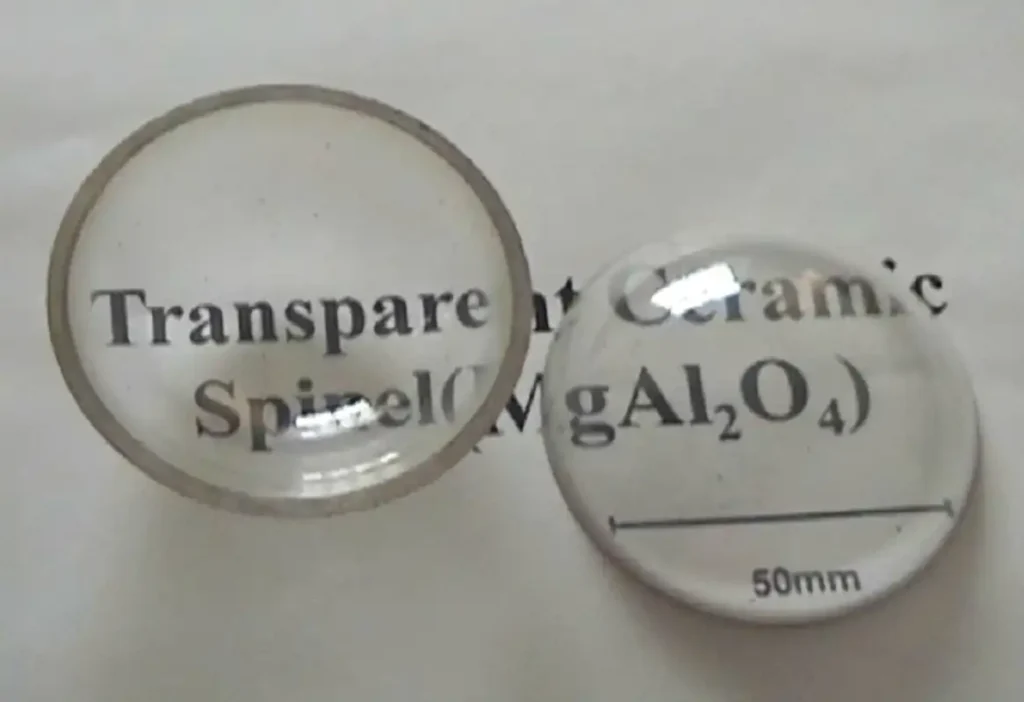
Wang Mengmeng et al. found through research that the addition of Al2O3 improves the sintering properties of MgO ceramics. Al2O3 reacts with MgO to generate MgAl2O4, which plays a bonding role and is distributed around the MgO ceramic grains, making the particles tightly bonded and filling the pores, thereby reducing the porosity and improving the density; the addition of Al2O3 improves the thermal shock resistance of MgO ceramics. When the addition amount of Al2O3 is 10%, the thermal shock resistance of MgO ceramics is the best.
TiO2-coated magnesium oxide powder
Yu Yin et al. used nano-magnesium oxide, titanium sulfate, and ammonia water as raw materials to prepare nano-magnesium oxide powder coated with TiO2 precursor on the surface, and used polyvinyl alcohol as a binder to press the sample into shape. The results show that the peak intensity of magnesium titanate phase in the XRD spectrum of the fired sample gradually increases, and the formation of magnesium titanate in the microstructure slows down the tip stress of the crack of the sample during thermal shock, hinders the extension of the crack, and effectively improves the thermal shock stability of magnesium oxide ceramics. The test results of the sample sintered at 1550℃ are better than those of the sample sintered at 1450℃, indicating that the sample is sintered more completely at a higher temperature, the magnesium titanate crystal grows better, and it is more conducive to improving the sintering and thermal shock resistance of magnesium oxide ceramics.