Since the quality of magnesium oxide will have a significant impact on the performance of rubber-type chlorinated polyethylene, not all magnesium oxides can be used in CPE. Magnesium oxide is generally divided into heavy magnesium oxide and light magnesium oxide according to bulk density; it can also be divided into high-activity magnesium oxide, medium-activity magnesium oxide, low-activity magnesium oxide and relatively inert magnesium oxide according to chemical activity.
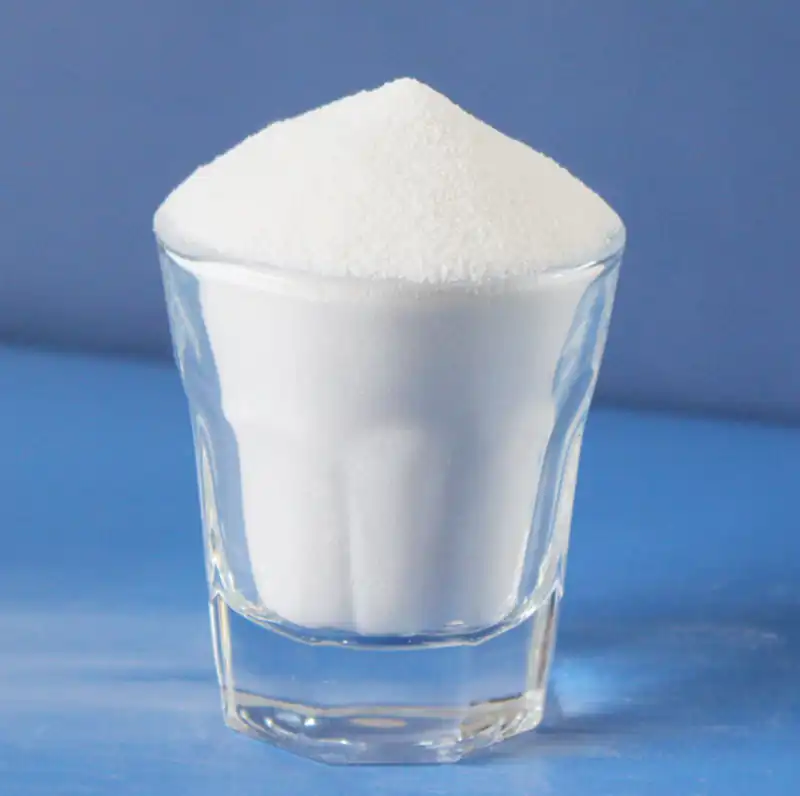
Generally speaking, only light-activity magnesium oxide can be used as a vulcanization aid for CPE. However, when selecting magnesium oxide, we should not only pay attention to the content of magnesium oxide, but also think that the higher the content, the better. First of all, the quality of magnesium oxide should be comprehensively considered from the aspects of content, activity (citric acid value or iodine absorption value), bulk density, particle size, surface modification, etc. Then, comparative screening is carried out through testing.
A large number of tests have proved that the quality of magnesium oxide has a significant relationship with the physical properties of CPE rubber, such as the degree of vulcanization, vulcanization speed, elongation at break, tensile strength, etc. Generally speaking, lightweight and low-activity magnesium oxide is adopted by most formulations.
At the same time, the particle size of magnesium oxide is also closely related to the acid absorption rate of CPE, and also affects the tensile strength, vulcanization speed and vulcanization degree. The finer the particle size of magnesium oxide, the better the acid absorption rate, which helps to improve the tensile strength and promote vulcanization.