High-purity magnesium oxide is a key functional material in the manufacturing of MLCCs (Multilayer Ceramic Capacitors). Its application value is reflected in enhancing heat resistance, mechanical strength, and dielectric properties, meeting the demands of high-end electronic devices. The industry has established clear purity standards (such as HG/T2573-2012) and optimized additive ratios (2-8%). With the growing demand for high-frequency and high-voltage MLCCs from 5G and new energy vehicles, the application of high-purity magnesium oxide will further expand.
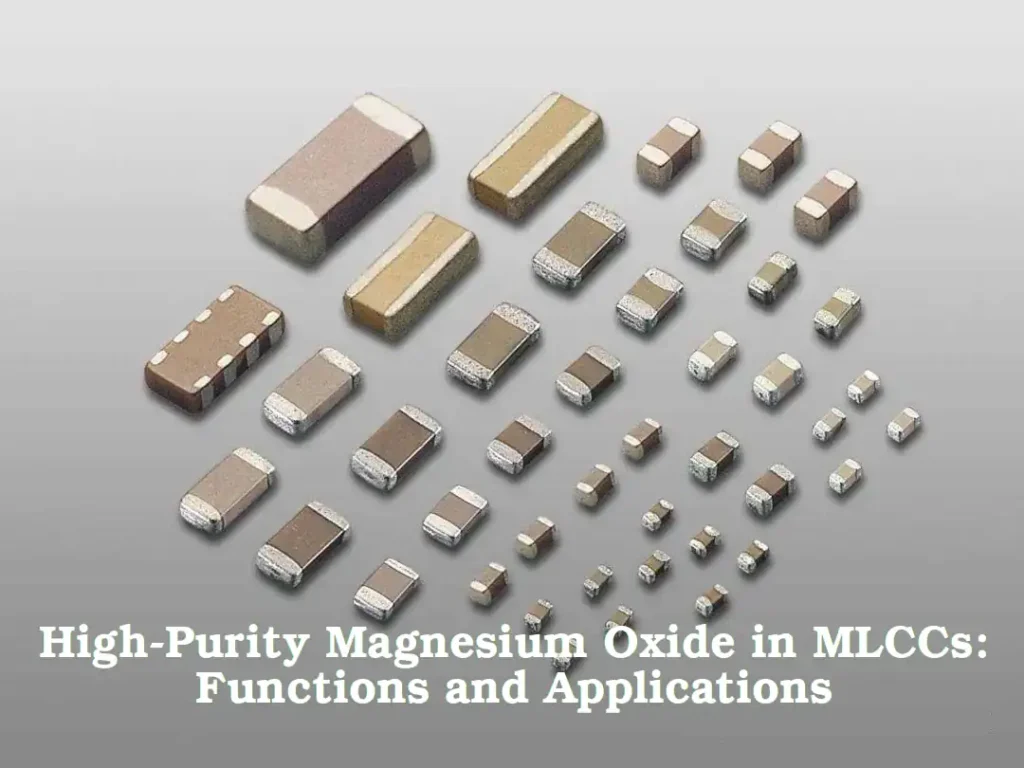
I. Basic Raw Material Composition of MLCCs
Ceramic Dielectric Components
The ceramic dielectric of MLCCs is primarily composed of barium titanate (BaTiO₃), supplemented by other oxides such as zirconium dioxide (ZrO₂), calcium oxide (CaO), etc. The dielectric composition varies depending on the MLCC type:
- C0G type: Primarily based on strontium zirconate (SrZrO₃) or barium strontium titanate (BaSrTiO₃), with stable dielectric constant and excellent temperature characteristics.
- X7R/X5R type: Based on barium titanate (BaTiO₃), with the addition of rare earth oxides (such as Y₂O₃) and transition metal oxides (such as MgO, MnO) to adjust dielectric properties.
Role of Additives
Magnesium oxide (MgO) is one of the auxiliary components, often added together with silicon dioxide (SiO₂), calcium oxide (CaO), etc., used to optimize sintering performance and dielectric characteristics.
II. Functions of High-Purity Magnesium Oxide in MLCCs
Performance Optimization
- High-temperature resistance: Magnesium oxide has a high melting point of up to 2852℃, which can improve the stability of MLCCs in high-temperature environments, allowing them to maintain electrical performance above 150℃.
- Mechanical strength: By filling microscopic ceramic defects, it enhances material densification and improves resistance to impact and wear.
- Electrical insulation: Reduces ceramic conductivity and improves insulation resistance, suitable for high-voltage and high-frequency circuits.
Process Improvement
- Sintering aid: Magnesium oxide can lower the sintering temperature (approximately 1320-1350℃), promote ceramic densification, and shorten the production cycle.
- Dielectric modulation: By adjusting the crystal structure, it optimizes the dielectric constant (ε=9.8-10.2) and dielectric loss, meeting the needs of different MLCC models.
III. Technical Standards and Addition Ratio
Purity Requirements
High-purity magnesium oxide needs to meet MgO content ≥ 98% (industrial grade) or ≥ 99.9% (electronic grade), with impurities such as calcium and iron controlled at the ppm level.
Typical Addition Amount
- General MLCCs: The addition ratio is typically 2-3 mol% (approximately 0.5-1.5 wt%). Excess may lead to a decrease in dielectric properties.
- High-frequency MLCCs: Nano magnesium oxide (particle size < 500nm) addition can be increased to 5-8% to improve high-frequency signal transmission loss.
IV. Application Cases and Industry Practice
Actual Applications
- High-voltage MLCCs: High-purity magnesium oxide from Hebei Meixi Bio Co., Ltd. serves as an insulating medium, controlling the dielectric constant fluctuation of the product within ±2% and improving consistency.
- 5G communication devices: Adding 3-8% magnesium oxide to silicon nitride ceramic substrates optimizes thermal conductivity and signal integrity.
Type Differences
- C0G type: Magnesium oxide is mainly used to adjust the Curie temperature (1 mol% MgO decreases the BaTiO₃ Tc by 3-5℃), meeting low-temperature stability requirements.
- X7R type: Acts as a grain boundary modifier, suppressing the drift of dielectric constant with temperature, ensuring ΔC/C ≤ ±15%.
Suggestions
For specific formulations or process parameters, refer to the technical manuals of electronic grade magnesium oxide suppliers (such as Messi Biology), or adjust the doping strategy based on the MLCC type (C0G/X7R).