Recently, in Tangshan Harbor Economic Development Zone, held a “primary battery method of ultra-high purity magnesium oxide / power cogeneration project technology results conference”, the Beijing Institute of Technology (Tangshan) Transformation Research Center independent research and development of “primary battery method of ultra-high purity magnesium oxide” technology to achieve a breakthrough! breakthrough, solving the technical and industrialization problems that our country has been tackling since the 1970s, and received great attention from the industry!
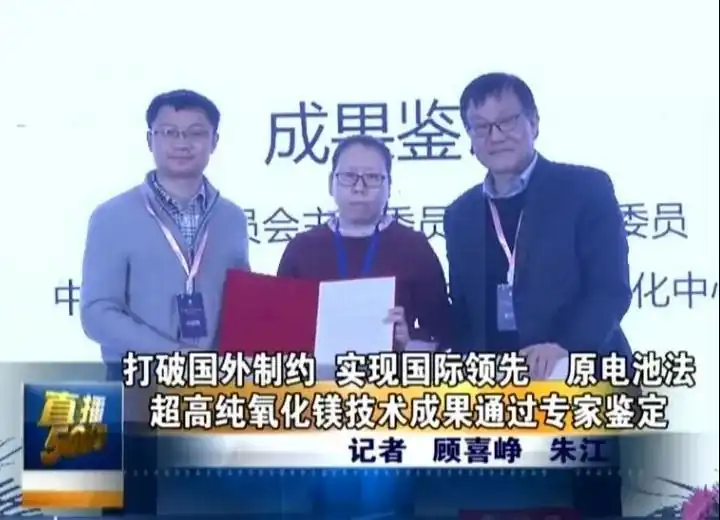
Why this high-purity magnesium oxide preparation technology breakthrough will be so important? This also has to start from the important application of high purity magnesium oxide and domestic development.
The important application of high purity magnesium oxide
High-purity magnesium oxide has excellent acid and alkali resistance and electrical insulation, good light transmission, high thermal conductivity, widely used as high-temperature heat-resistant materials.
With the development of industry, high purity magnesium oxide in the traditional field of application scale is expanding day by day, the new application areas are also constantly exploring and developing, the market capacity is expanding. From the development trend, the proportion of high-purity magnesium oxide consumption is increasing year by year.
High-purity magnesium oxide in the ceramic industry as ceramic crucible, substrate and other raw materials; in the electronics, electrical industry as magnetic device filler, insulating materials and a variety of carriers. 99% or more high-purity magnesium oxide is the world’s production of oriented silicon-steel sheet is the best chemical raw material. In addition, with high purity magnesium oxide as raw material, can also produce electrofusion magnesium oxide single crystal, high purity electrofusion magnesium oxide, nano magnesium oxide and other special special magnesium oxide series products, these products in the electronics, electrical appliances, optics, instrumentation, metallurgy, national defense and aerospace and other fields have a wide range of applications.
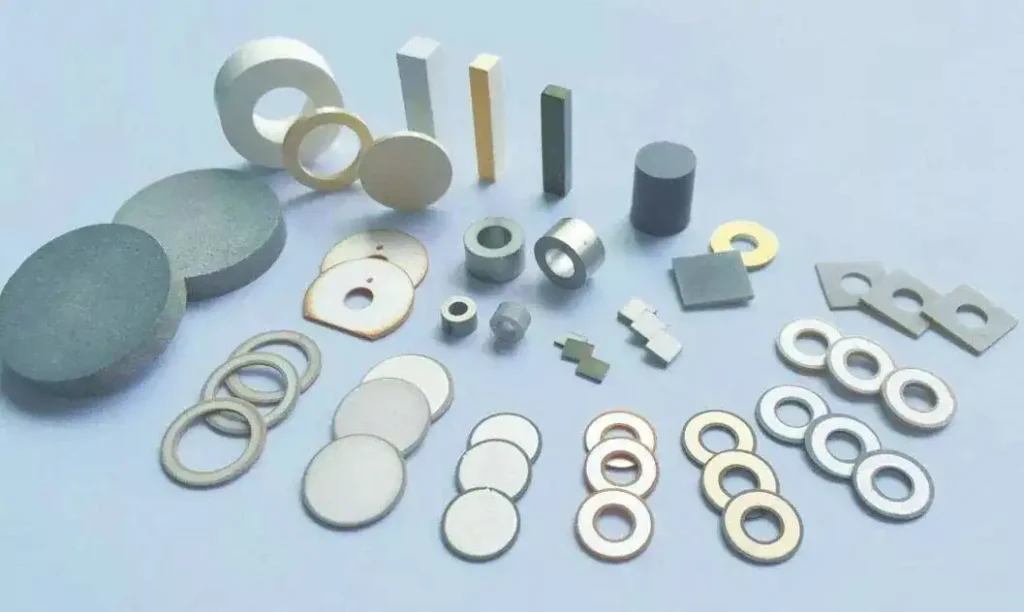
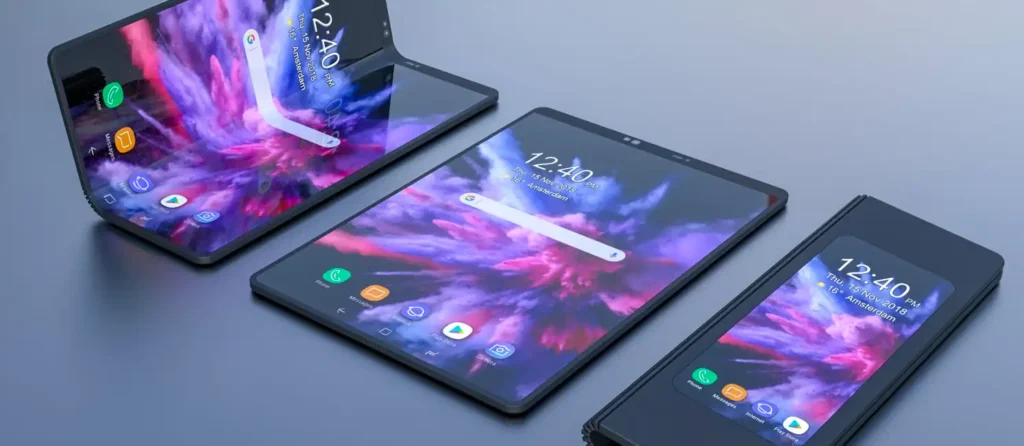
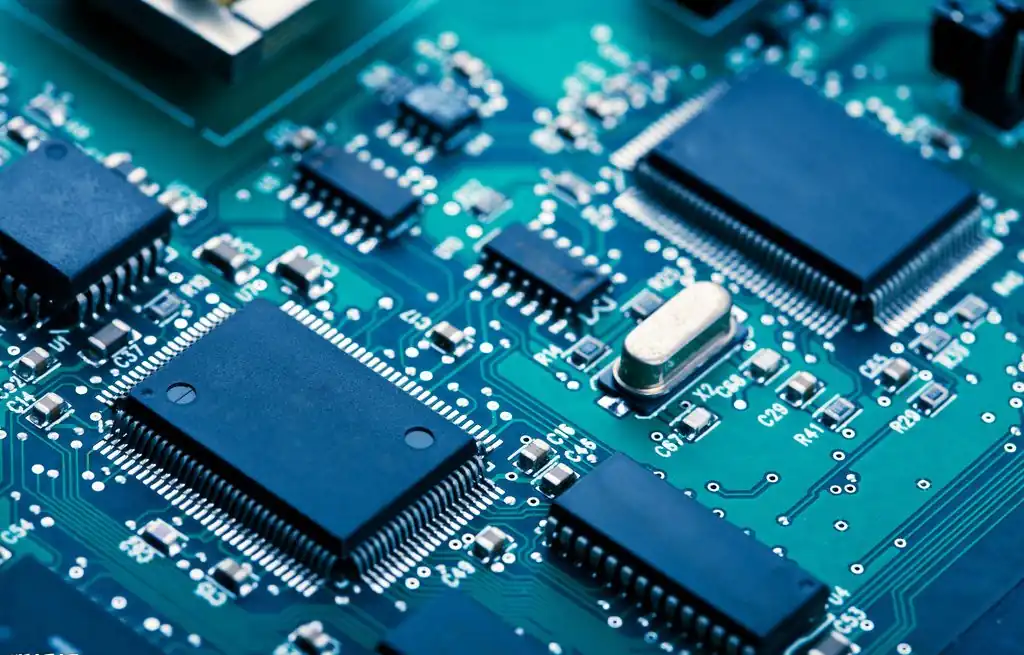
China has a difficult road to catch up in this field
China’s magnesium oxide production originated in the coastal areas of Dalian, Tianjin and other places to bitter brine as raw material, using soda ash method of magnesium oxide production. However, the method has high energy consumption and cost, and the development is slow. Later, the dolomite carbonization method (known as Patterson method abroad) was successfully developed, due to lower production costs, has been the rapid development of production capacity gradually shifted to Hebei, Shanxi, Hunan, Sichuan and other dolomite reserves in the region. However, due to the high calcium content in the magnesium oxide obtained by the dolomite carbonization method, the production of high-purity products is limited.
From 1966 to 1971, Liao magnesium company of metallurgy ministry, Anshan coking refractory design and research institute, Luoyang refractory material research institute cooperation, using the water chloride magnesium stone of Qinghai salt lake as raw material, using spray method and pyrolysis method to carry on the development of high-quality magnesium oxide research, and has achieved certain results.
In 1985, Professor Sun Guoqing of East China Normal University improved the seawater lime method, and researched the 99.5% purity of high-purity low-boron magnesium oxide, which ended the history of our country not being able to independently develop and produce high-purity (more than 99%) magnesium oxide. However, due to engineering technology and other problems, it failed to realize industrial production.
In June 2000, by Li Tong, Chen Caichang research serpentine chemical wet production of high-purity magnesium oxide one-time trial production success, in 2001 began formal production. The success of this project put into production ended the history of Chinese people who could not mass produce more than 99% high purity magnesium oxide, and has been highly valued by domestic and foreign experts.
At present, the domestic preparation of magnesium oxide production process is mainly for ore calcination method and seawater / brine purification method, ore calcination method of magnesium oxide purity up to only 98.5%, has been unable to fully meet the needs of China’s metallurgy and other high-end manufacturing industry. At the same time, some countries have a long-term monopoly on seawater synthesis method technology, resulting in China had to import a large number of high cost.
Currently the main preparation method
The production of high-purity magnesium oxide is generally used in the preparation of ordinary magnesium oxide, and through a special de-emulsification process to achieve. There are mainly:
(1) gas phase method – the high purity of magnesium metal and oxygen reaction to generate nuclei, and then make the particles continue to grow, the production of high purity micronized magnesium oxide.
(2)Inorganic acid dissolution method-Dissolve the crude raw material of magnesium oxide with inorganic acid such as sulfuric acid, hydrochloric acid, nitric acid, etc. to make the magnesium salt of inorganic acid, and then get the high purity magnesium oxide through precipitation, separation, washing and calcination.
(3)Calcination method of magnesium hydroxide.
(4) Magnesium chloride direct pyrolysis method.
At present, the third method is mainly used domestically, i.e., using liquid or solid ore as raw materials, firstly preparing magnesium hydroxide with relatively high purity, then calcining magnesium hydroxide at a certain temperature to get high purity magnesium oxide.
Advancement of the new technology
According to the staff of the Transformation Research Center of Beijing Institute of Technology (Tangshan), “In the production process of magnesium selected for fuel cells using the primary cell method, it was found that ultra-high purity magnesium oxide could be generated”.
The primary cell method selects magnesium as the anode metal material for fuel cells, which increases the safety of each link in the fuel cell production, transportation, storage and refueling link, and converts magnesium into magnesium oxide in a short time, adding nearly 50% value, while no industrial three-waste emission can be realized in the process of obtaining ultra-high purity magnesium oxide.
In addition, the primary cell method breaks through the use of carbon-based non-precious metal catalysts, which reduces the cost of fuel cell manufacturing and improves the cost-effectiveness compared with traditional precious metal catalysts.
Compared with the magnesite calcination method and seawater/brine synthesis method commonly used to obtain magnesium oxide before, the use of the primary cell method can obtain ultra-high purity magnesium oxide, the purity of which is up to 99.95%, and the cost is lower, the process route is shorter, the product yield is higher, and the production process is accompanied by the generation of a large number of high-quality direct current electricity.
This technology in the material research and development, preparation and industrialization of the international advanced and world-leading technological breakthroughs, to help solve the high-strength stainless steel, aerospace steel, high-end bearing steel is not the core of the short board problem, breaking the field has been foreign technology “neck” of the status quo.