Abstract
Serpentine is a rich ore containing magnesium oxide, and its main component is Mg3Si2O5(OH)4, in which the theoretical content of magnesium oxide is 43.5%. Sichuan Province is a rich ore area of serpentine, and the content of magnesium oxide in serpentine is generally 36%. In some areas, the content of magnesium oxide in serpentine can be as high as 40% or more.
Serpentine is usually discarded as solid waste in the process of asbestos mining. The amount of asbestos mined in my country has reached 200,000 tons per year, and the asbestos content of ore in asbestos mines is about 8%, of which more than 90% – that is, millions of tons of serpentine are asbestos tailings, and the utilization rate of tailings accounts for only 2% of the emissions. Therefore, the emission of serpentine as waste is astonishingly large. This not only wastes natural resources, but also has a certain impact on the local environment. Although there are many methods for making light magnesium oxide using serpentine, the conditions for converting these methods into industrial production are harsh.
The present invention relates to a method for extracting magnesium oxide from serpentine. The method comprises the following steps: crushing serpentine into powder, leaching with sulfuric acid, filtering and drying to obtain sulfates of magnesium and other impurities, and then burning the above salts in air at 700-1100°C, then immersing the burned solid in water, filtering and drying to obtain magnesium salts, and finally burning the magnesium salts at above 1114°C to obtain magnesium oxide. The purity of the magnesium oxide obtained by the method can reach more than 99.94%, and the process is simple and the production cost is low, which opens up a new way for the utilization of serpentine and the extraction of high-purity magnesium oxide.
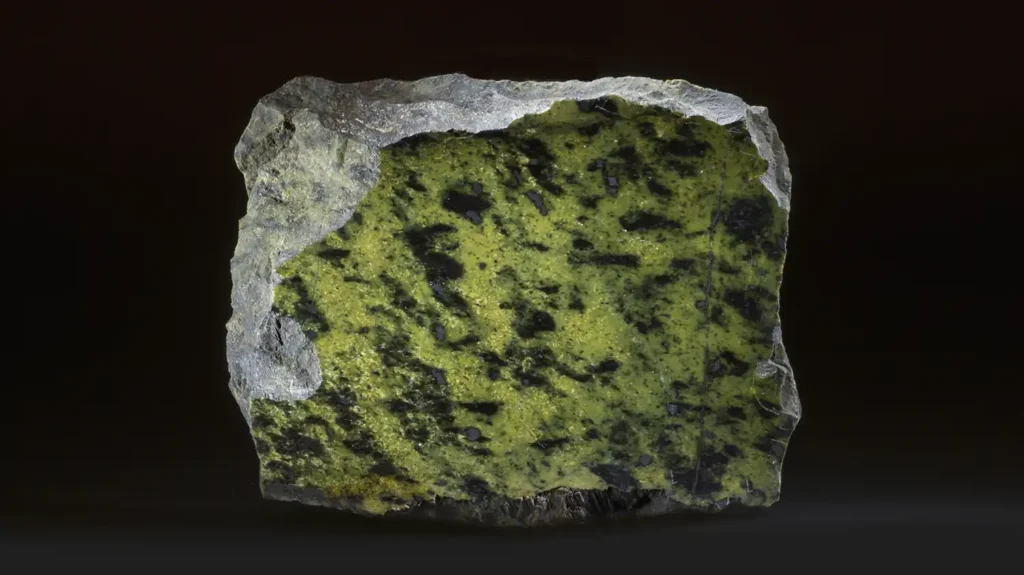
Description
The present invention belongs to a method for preparing magnesium oxide, specifically a method for extracting magnesium oxide from serpentine.
At present, magnesium oxide is mostly prepared by extracting magnesium oxide from seawater or magnesite as raw materials, but the preparation of high-purity magnesium oxide is mainly extracted from seawater. Extracting magnesium oxide from seawater requires a large amount of soda ash as a precipitant to remove impurities. The higher the purity of the extracted magnesium oxide, the higher the purity of the soda ash used, and the higher the cost.
The content of magnesium oxide in serpentine ore is generally above 36%. my country has abundant serpentine resources and a wide distribution range, but it has not been properly utilized. How to extract magnesium oxide from serpentine has attracted people’s attention. Serpentine is mainly composed of SiO2 (about 40%), MgO (about 38%), and Fe2O3 (about 8%), and also contains a small amount of Al, Cr, Ca, Mn, etc. oxides. “Non-metallic Minerals” No. 3, 1991, 32-39 pages disclose the article “Comprehensive Utilization of Chrysotile Tailings – Extracting Magnesium Oxide from Serpentine”. The magnesium oxide extraction process recorded in the article is: serpentine ore is crushed into powder, and 30% sulfuric acid is added to dissolve the ore for leaching to generate soluble magnesium salts and other soluble salts of impurities, and then impurities are removed by precipitation, and basic magnesium carbonate is recrystallized after filtering, and magnesium oxide is calcined. The key to extracting magnesium oxide from serpentine is the impurity removal process, which is related to the problems such as the extraction purity, production cost and feasibility of industrialized production of magnesium oxide. The impurity removal of the above-mentioned prior art is to adjust the pH value with an alkaline solution to carry out precipitation impurity removal. This impurity removal method consumes a large amount of alkali, so the cost is relatively high. If the purity of the extracted magnesium oxide is required to be higher, the purity of the alkali is also higher, and the production cost is also higher. The second problem of the precipitation impurity removal method is that it is impossible to completely separate ferrous ions from high-content magnesium salts. To solve this problem, the above-mentioned prior art uses Naclo oxidant to convert ferrous ions into trivalent ferrous ions and then remove them, but Naclo is very expensive and it is difficult to filter during separation. The third problem of the precipitation impurity removal method is that it is also difficult to separate a small amount of calcium components from high-content magnesium salts. In addition, in the precipitation impurity removal, the precipitation of ferric hydroxide colloid not only brings difficulties to filtration, but also causes a large loss of extracts. Therefore, this method is not only costly, but also unsuitable for industrial production.
The purpose of the present invention is to provide a new method for extracting magnesium oxide from serpentine in view of the problems existing in the above-mentioned prior art. The method is easy to industrialize, has low cost, and the extracted magnesium oxide has high purity.
The solution to achieve the purpose of the present invention is as follows:
(1) crush the serpentine ore sample into powder,
(2) heat the above ore powder in sulfuric acid with a concentration of 10-40% to fully dissolve it, and filter to obtain a sulfate solution,
(3) evaporate the above filtrate to dryness to obtain solid sulfate,
(4) burn the solid sulfate at 700-1100°C in air,
(5) soak the burned solid in water, and then filter to remove the residue to obtain a magnesium salt solution,
(6) burn the solid magnesium salt in air at 1114-1350°C to obtain magnesium oxide,
The above whole process is carried out under normal pressure.
In the burning process of (4) above, except for magnesium salt and calcium salt, other metal salts are decomposed into water-insoluble oxides. Calcium salt is insoluble in water, and only magnesium salt is soluble in water. Therefore, the burned solid is soaked in water and filtered to remove the residue, and the impurities are removed to obtain a magnesium salt aqueous solution. In this process, as long as the burning is sufficient, the impurity removal is relatively complete. The high impurity removal burning temperature is conducive to the decomposition of impurities, but in actual production, considering the productivity requirements and equipment conditions, the impurity removal burning temperature is usually in the range of 900-1000℃.
The solid silica filtered out during the above acid-soluble ore leaching can be used as a filter aid material; and sulfuric acid can be recovered during both burning processes.
Example: The ore sample is Shaanxi Lantian serpentine, and its component content (%) is:
Sio2 (40.28), Fe2O3 (7.9), Al2O3 (0.33), Cr2O3 (0.76), NiO (0.98), CaO (0.55), MnO (0.25), MgO (38.40).
Crush the serpentine sample and pass it through a 200-mesh sieve; take 50 grams of serpentine powder, add 100 milliliters of 25% sulfuric acid, heat to 110°C in a reflux device and extract for 1 hour; filter the discarded slag (silica); evaporate the filtrate to dryness, and burn it in a muffle furnace at 1100°C for several minutes; then filter it with water, evaporate the filtrate to dryness, and burn it at 1300°C to obtain 12 grams of chemically pure magnesium oxide. The purity of the magnesium oxide is above 99.94%, and the impurity content (%) obtained by spectral analysis is: Cu 0.0002, Ni 0.0005, Mn 0.002, Ca 0.01, Si 0.01, Al<0.01, Fe<0.01. The content in this example is weight percentage.
The advantages of the present invention are: 1. The process is simple, the cost is low, and it is suitable for industrial production, which opens up a new way for the utilization of serpentine; 2. High-purity magnesium oxide can be extracted using only industrial-grade sulfuric acid, the purity can reach reagent grade, and the loss of the purified product is extremely small. In addition, the burning and impurity removal method of the present invention solves the difficulties in removing ferrous ions and a small amount of calcium components from high-content magnesium salts in chemical purification in the past.
Studies have shown that as long as the calcination conditions are selected well, the recovery rate of the expanded test can be close to or even reach the recovery rate of the laboratory test. In the industrial test, no impurities such as Cl- and SO2-4 are introduced during the preparation process. The calcium oxide content can be controlled by ore dressing and removed by using its solubility in water during digestion and washing. At the same time, the pH during the carbonization process is >7, and salts such as iron and manganese are precipitated in the waste residue in the form of hydroxides. Therefore, this method can be used to obtain high-quality light magnesium carbonate and light magnesium oxide.
In addition, the research shows that the process flow during carbonization and after carbonization is the same as the existing process flow for producing light magnesium carbonate and light magnesium oxide by dolomite carbonization, so it is easy to achieve industrial production.