With increasingly stringent environmental regulations and growing consumer awareness of environmental protection, PVC products are progressively moving towards “lead-free,” “low heavy metal,” and “low VOC (Volatile Organic Compounds)” formulations. The traditional heat stabilization system primarily based on lead salts is gradually being phased out, making the research and application of alternative materials a hotspot in the industry. In this context, magnesium carbonate, with its non-toxic, harmless, and good thermal stability properties, has become a key material in environmentally friendly PVC systems, garnering significant attention, especially in lead-free heat stabilization and low-smoke, flame-retardant applications.
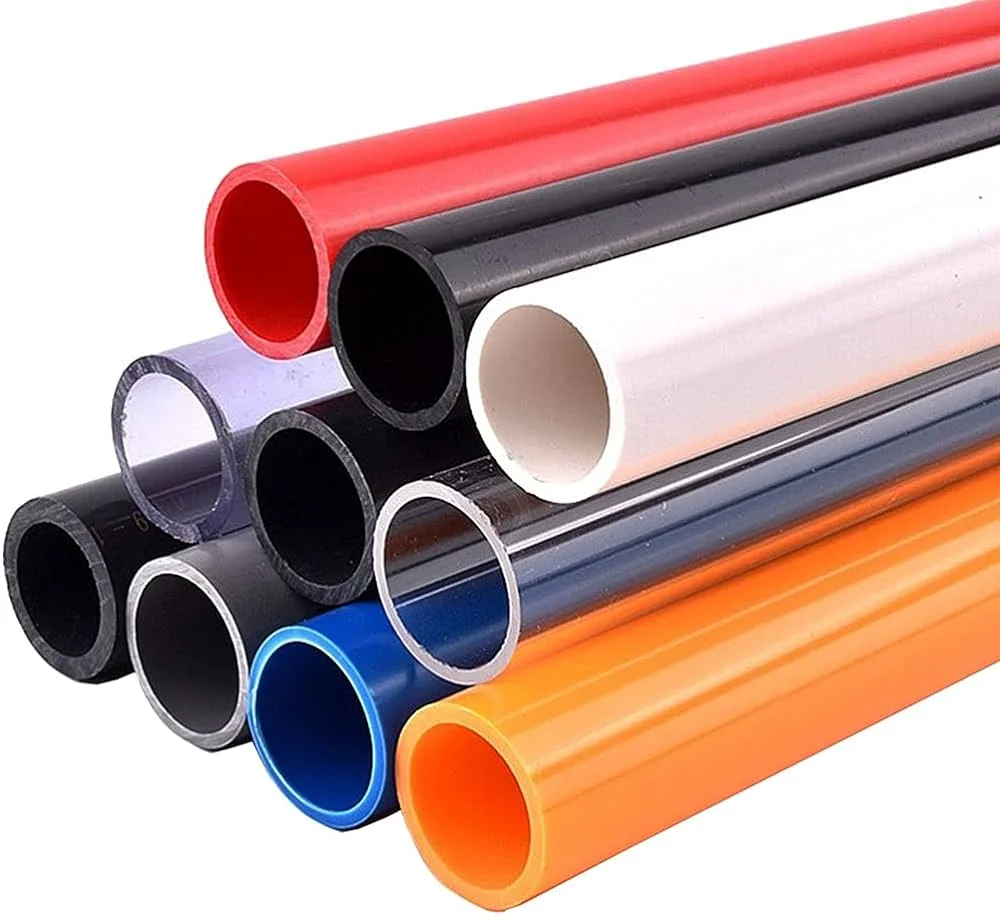
I. Main Functions of Magnesium Carbonate
- Auxiliary Heat Stabilizer: Magnesium carbonate is weakly alkaline and can absorb the hydrogen chloride (HCl) produced during PVC processing, slowing down the degradation reaction and thus enhancing thermal stability. This is particularly important for heat stability control in lead-free formulations.
- Acid Scavenger: When PVC undergoes thermal decomposition, the generated HCl accelerates degradation. Magnesium carbonate can absorb these acidic gases, maintaining a neutral environment within the system and reducing chain scission.
- Improved Processing Performance: Provided it is used in appropriate amounts, magnesium carbonate can reduce the adhesion of the PVC melt to processing equipment, improve extrusion and injection molding efficiency, and extend the service life of molds.
- Enhanced Mechanical Properties: As an inorganic filler, magnesium carbonate can enhance the rigidity and dimensional stability of PVC, making it particularly suitable for eco-friendly building materials, profiles, and other products where strength is required.
II. Environmental Advantages
Magnesium carbonate is naturally non-toxic and free of heavy metals, posing no harm to human health or the environment. In terms of complying with environmental regulations, it performs better than traditional lead salts or organotin stabilizers. It not only meets environmental requirements such as RoHS and REACH but is also easier to recycle and reuse, which is of positive significance for building a sustainable material system.
III. Typical Application Areas
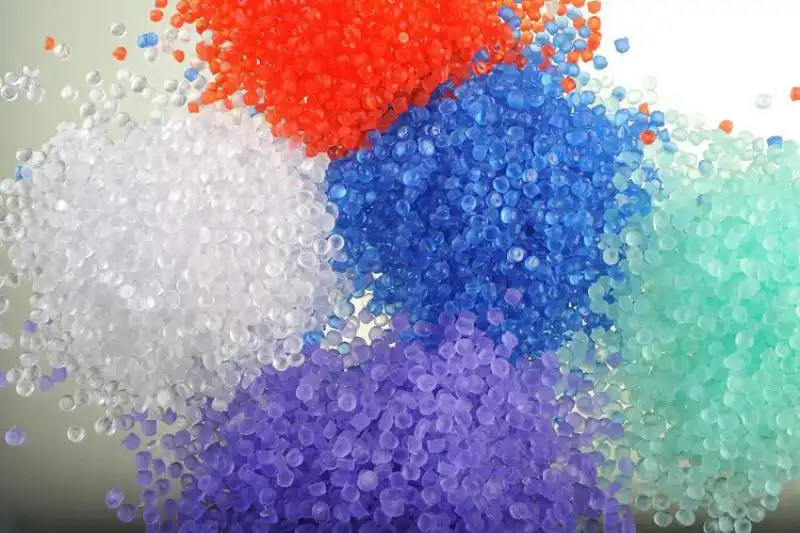
- Wire and Cable Sheathing Materials: In eco-friendly cable sheathing compounds, magnesium carbonate is often used in conjunction with calcium-zinc stabilizers to replace lead-containing formulations, meeting requirements for low smoke, low toxicity, and flame retardancy.
- Food-Grade and Medical PVC: In products with extremely high requirements for toxicity and migration, such as infusion tubes, transparent bottles, and food films, magnesium carbonate is an ideal stabilizing filler, ensuring product safety and freedom from contamination.
- Green Building Materials: In PVC building materials such as doors, windows, profiles, and pipes, magnesium carbonate helps to improve rigidity and weather resistance while supporting green building certifications and sustainable construction standards.
- Children’s Toys and Household Goods: These products need to be non-toxic and environmentally friendly. Magnesium carbonate, with its natural safety, has a clear advantage in replacing traditional additives.
IV. Challenges and Countermeasures
- Dispersibility Issues: Due to its small particle size and high surface polarity, magnesium carbonate tends to agglomerate in PVC, affecting processing and mechanical properties. Surface treatment (such as coating with fatty acids or silane coupling agents) can significantly improve its dispersibility and compatibility.
- Impact on Transparency: Ordinary magnesium carbonate may cause transparent PVC products to become whitish or hazy. Using high-purity, nano-sized ultrafine magnesium carbonate can greatly reduce the impact on transparency.
- Hygroscopicity Issues: Some types of magnesium carbonate easily absorb moisture in humid environments, which can lead to bubbles or delamination during PVC processing. This problem can be avoided by selecting lightweight, low-hygroscopic products and thoroughly drying them before use.
V. Future Trends
As environmental pressures continue to increase and consumer preferences for green materials rise, the use of magnesium carbonate in the PVC industry will further expand. Its role will become increasingly important, especially in lead-free, tin-free, and low-smoke, flame-retardant applications. Simultaneously, the research and development of modified magnesium carbonate will be a key direction for improving performance and expanding applications, such as developing surface-coated, nano-scale, and composite magnesium carbonate products.