Messi Biology states that soft capsules, widely used as a dosage form in nutritional supplements and pharmaceuticals, offer advantages like good taste, rapid absorption, and ease of swallowing. However, during production, packaging, and storage, soft capsules are prone to sticking together, which affects their appearance and user experience, and can even lead to product spoilage. To solve this problem, magnesium carbonate (MgCO3) is widely used for anti-sticking treatment of soft capsules, playing a crucial role in processing and stability.
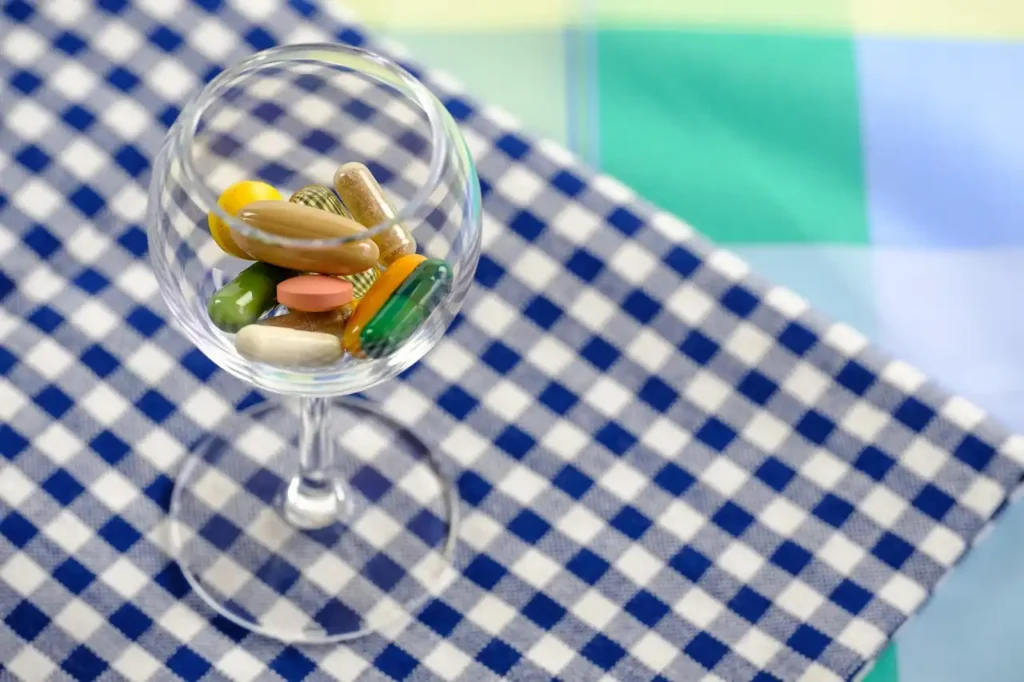
1. Physical Characteristics and Anti-Sticking Principle of Magnesium Carbonate
Magnesium carbonate’s effectiveness as an anti-sticking agent is rooted in its physical properties:
- Strong Hydrophobicity: Magnesium carbonate possesses a degree of hydrophobicity, enabling it to form a dry, particulate film on the capsule surface, thereby reducing moisture-induced adhesion.
- Moderate Hygroscopicity: It can absorb some surface moisture, lowering the humidity on the capsule surface and inhibiting the formation of condensation.
- Suitable Particle Size: Micronized magnesium carbonate offers excellent coverage, distributing evenly across the capsule surface without affecting the capsule’s sheen or feel.
2. Application Methods
Magnesium carbonate is applied in several ways to prevent sticking:
- External Dry Powder Treatment: After soft capsules are formed, magnesium carbonate powder is lightly dusted onto them using tumbling or sieving equipment.
- Combined Use with Talc and Silica: In some processes, it’s compounded with other inert powders to enhance the overall anti-sticking effect.
- Suitable for High-Humidity, High-Temperature Packaging Environments: It’s particularly effective in hot and humid climates, such as those in Asia, significantly extending product shelf life.
3. Advantages for Finished Product Quality
The use of magnesium carbonate offers several benefits for the quality of the final product:
- Prevents capsules from sticking together, improving the efficiency of automated packaging.
- Does not react with the capsule’s contents, ensuring chemical stability and safety.
- Light magnesium carbonate that complies with food or pharmacopoeia standards can be selected, meeting various regulatory requirements.
4. Precautions
To ensure optimal results and product quality when using magnesium carbonate:
- The particle size of magnesium carbonate should be appropriate; overly coarse particles can affect the capsule’s feel, while overly fine ones are prone to creating dust.
- Dosage must be controlled within a reasonable range to prevent excessive powder residue from affecting the consumer experience.
- It’s recommended to use it in conjunction with dedicated powder removal devices and airflow cleaning equipment to ensure the finished product is clean.