Magnesium hydroxide is the most popular inorganic flame retardant on the market now, but due to the surface of magnesium hydroxide has “hydrophilic and oleophobic” characteristics, there will be poor compatibility with the resin in the actual application of the situation, coupled with its own flame retardant efficiency is low, which directly hinders the further use of magnesium hydroxide in the actual production process. Magnesium hydroxide surface treatment can not only enhance the compatibility of magnesium hydroxide and resin, but also improve the flame retardant ability. Filling EVA with magnesium hydroxide (Mg(OH)2) can improve the thermal stability, tensile strength and processing fluidity of EVA.
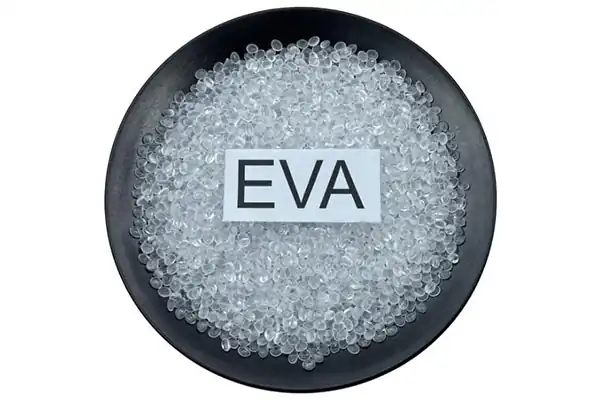
The mechanical properties of ordinary magnesium hydroxide, hexagonal flake magnesium hydroxide and stearic acid (SA)-modified magnesium hydroxide filled into ethylene vinyl acetate copolymer (EVA) were investigated. The structure and morphology of the three types of Mg hydroxide and EVA/Mg hydroxide composites were analyzed by infrared spectroscopy (FT-IR) and scanning electron microscopy (SEM).
The results showed that the hexagonal flake magnesium hydroxide and SA-modified magnesium hydroxide effectively reduced the surface polarity compared with the ordinary magnesium oxide, which greatly reduced the influence on the mechanical properties of the composites; the dispersion of 4% (mass fraction) SA-modified magnesium hydroxide in the EVA resin was uniform, and the interfacial adhesion between the surface of the filler and the surface of the resin was better; and the incorporation of the magnesium hydroxide (MH) powder increased the tensile strength of the EVA/ MH composites, which were characterized by the high tensile strength of the EVA/ MH composites. The addition of MH powder increased the tensile strength of EVA/MH composites, in which 4% (mass fraction) SA modified MH powder had the greatest effect on the tensile strength of the composites, and hexagonal flake MH had the least effect; when the filler amount of MH powder reached 60 mass fraction (60 mass fractions of MH was filled into 100 mass fractions of EVA), the elongation at break was reduced to less than 100%, and the mechanical properties of the composites were deteriorated drastically.