Magnesium hydroxide (Mg(OH)₂) serves not only as a basic flame retardant filler but also synergizes with various functional materials, expanding its applications in polyurea coatings for demanding scenarios. This is increasingly important in high-safety environments like rail transit, tunnels, ships, military applications, and power facilities.
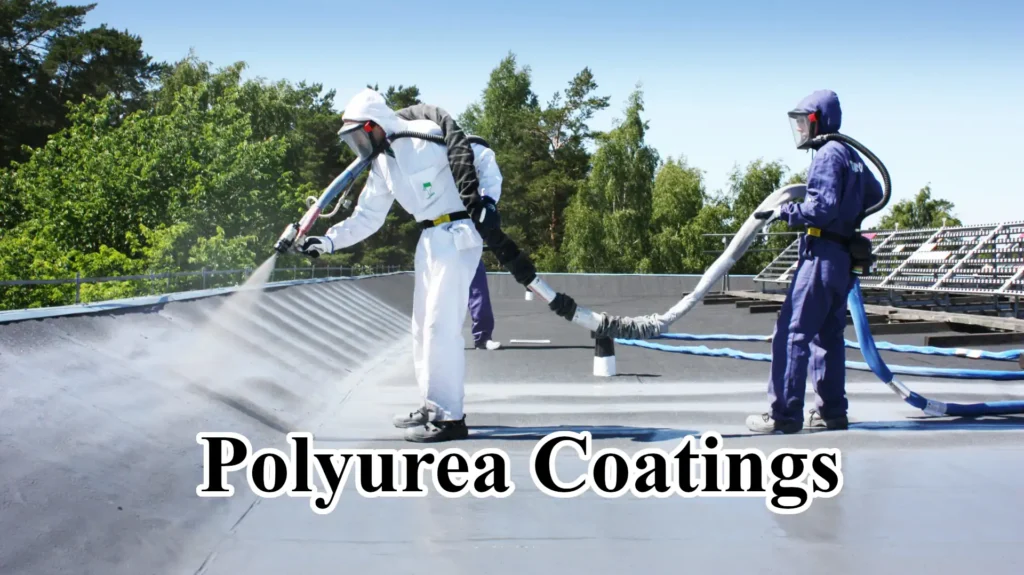
1. Fireproof Polyurea Coatings for Tunnels/Subways
Tunnels and subways face strict requirements for high-temperature and smoke toxicity control. Traditional polyurea is difficult to apply due to its flammability.
Polyurea systems incorporating magnesium hydroxide and phosphorus-based flame retardants can achieve flame retardant standards of B1 or higher, meeting tunnel fire protection specifications.
High-temperature resistant coating structural designs can also enhance the stability of steel in fire.
2. Explosion-Proof and Flame Retardant Polyurea for Military/Naval Vessels
Military coatings, in addition to corrosion protection, must possess explosion-proof, fireproof, and impact-resistant properties.
Synergistic use of magnesium hydroxide with nanoceramic powders (such as SiO₂, Al₂O₃) can enhance the rigidity and insulation of the flame retardant layer.
Widely applied in ship cabins, ammunition depots, and the outer walls of fuel pipelines.
3. Insulation + Flame Retardant Composite Coatings for Power Equipment
Polyurea used in cable trenches, cable trays, substations, and other areas must have good insulation and flame retardancy.
Magnesium hydroxide has excellent natural insulation properties and good thermal stability.
Functional polyurea with high-pressure resistance and low-smoke, halogen-free characteristics can be prepared by compounding magnesium hydroxide with aluminum hydroxide.
4. Polyurea Coatings for Interior/Seat Composites in Rail Transit
Materials for rail vehicles must meet the EN 45545-2 fire protection standard.
Polyurea prepared using modified magnesium hydroxide (e.g., surface silane treatment) can be sprayed on seats, wall panels, and inner door walls, improving flame retardancy while maintaining flexibility and adhesion.
5. Explosion-Proof and Anti-static Polyurea Systems
Polyurea used in coal mines, petrochemical industries, and other locations must possess both anti-static and flame retardant properties.
Anti-static coatings with a surface resistance of 10⁶~10⁸ Ω and flame retardancy reaching V-0 or B1 level can be prepared by synergistically incorporating conductive carbon black or graphene with magnesium hydroxide into the polyurea system.
6. Infrared Reflective/Thermal Protective Polyurea Materials
In specific applications (such as sun-exposed environments, tactical equipment), infrared reflection or thermal protection is required.
Introducing magnesium hydroxide and infrared reflective fillers (such as TiO₂, mica) into the polyurea system can achieve: reflection of infrared heat radiation, delaying material temperature rise, and improving thermal comfort and sun-resistant lifespan.
7. Wear-Resistant + Flame Retardant Composite Performance Coatings
Steel structures, storage tanks, and machinery housings often require both fire protection and wear resistance.
After adding magnesium hydroxide, it can synergize with high-hardness fillers (such as wollastonite, silicon carbide) to enhance the surface hardness and scratch resistance of polyurea.
8. Fireproof Coatings for Steel Structures in High-Rise Buildings
Steel structures rapidly lose strength when exposed to fire, requiring high-temperature resistant, intumescent flame retardant protection layers.
By adding magnesium hydroxide and intumescent flame retardants (IFR), polyurea systems can form a dense carbon char layer, effectively insulating heat.
Suitable for fire protection of large commercial and high-rise residential buildings.
9. Flame Retardant Coatings for Water Facilities and Ship Bulkheads
Ship cabins often encounter high humidity environments, requiring materials with multiple functions such as moisture resistance, flame retardancy, and corrosion resistance.
Magnesium hydroxide is not hygroscopic, corrosion-resistant, and produces extremely low smoke during combustion, making it suitable for: ship cabin walls, living area cabin doors, and the outer surfaces of cable channels.
10. The Role of Magnesium Hydroxide in Multifunctional Integrated Composite Systems
Magnesium hydroxide is no longer just a “filler” but an important component for functional integration.
It supports the integration of multiple functions: flame retardancy + corrosion protection + impact resistance + heat reflection + insulation.