In the production process of magnesium oxide, the calcination method occupies an important position, which can be divided into magnesite calcination method and water magnesite calcination method, and at present our country mainly adopts magnesite calcination method. Magnesite, MgCO3 content is very high, up to more than 90%, while containing a small amount of CaCO3 and other trace impurities. When magnesite is calcined in a high temperature environment, MgCO3 and CaCO3 will decompose, generating MgO and CaO, and releasing CO2 gas, this process is a heat absorption reaction. Magnesite begins to decompose when heated to 500℃, and its thermal decomposition mainly occurs near the interface, which is an ion diffusion reaction process, following the interfacial contraction mechanism, i.e., the shrinking shell mechanism, the outer surface of the original ore grains is gradually decomposed and peeled off, in which the diffusion of CO32- is the key step.
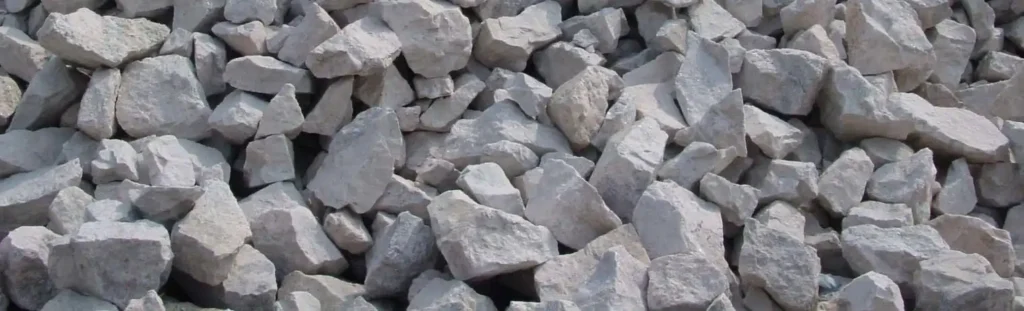
The method of smelting light magnesium oxide using magnesite mainly includes the following steps:
Calcination :
Magnesite is calcined into magnesium oxide at high temperature (usually around 950°C).
The calcination process can be carried out using a calciner, including mixed calcining vertical kiln, inter-wall calcining process, direct-fired calcining vertical kiln, rotary kiln and so on5.
Grinding fine :
The magnesium oxide obtained from calcination is finely ground with water for further processing.
Separation :
The sieved slurry is continuously stirred and a separator is added to separate the calcium and magnesium.
The slurry is pumped and filtered to obtain filtrate and precipitate, and the filtrate is heated and evaporated and then powdered to obtain calcium chloride.
Carbonization :
The precipitated magnesium oxide is slurried with water and then put into the carbonization tower.
The carbon dioxide gas from the kiln during calcination is fed into the carbonization tower through the air compressor and pipeline to carbonize the slurry and reduce it to magnesium carbonate.
Acid washing :
Put the magnesium carbonate into the acid solution after precipitation and filtration to remove the impurities such as iron hydroxide by filtration.
Add soluble magnesium hydroxide into the solution, and add ammonia brine at the same time, so that the magnesium hydroxide generated in the solution will precipitate down.
Press-filtering and drying :
After the precipitated magnesium hydroxide is pressed and filtered, it is lightly burned or dried to make light magnesium oxide.
Suggestion
Process optimization: In practice, the above steps can be optimized according to the specific conditions (such as the quality of raw materials, equipment performance, etc.) in order to improve production efficiency and product quality.
Environmental protection treatment: The waste gas and waste residue generated during the calcination and carbonization process should be properly treated to ensure compliance with environmental protection requirements.
Cost control: further reduce the production cost and improve the economic efficiency by choosing suitable raw material sources, optimizing the process flow and reducing energy consumption.
All the above methods can get high quality light magnesium oxide, and the process is relatively simple, suitable for large-scale production.