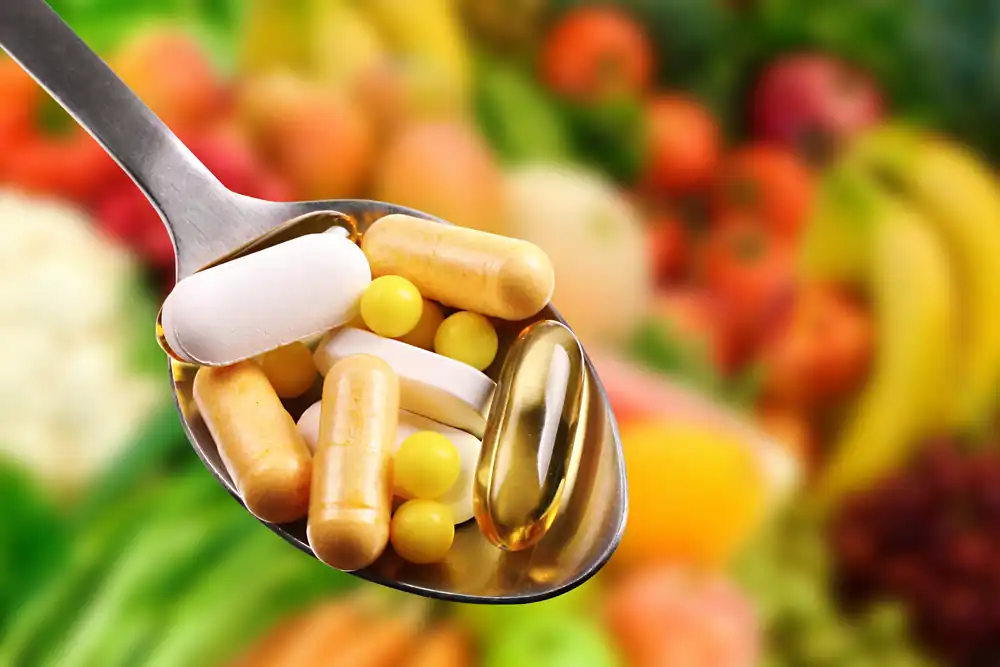
Existing microencapsulated products are mainly concentrated in flame retardant materials such as magnesium hydroxide. This is mainly because harmful substances to the human body are often used in the existing microencapsulation process. After microencapsulation, the product cannot be directly used as a raw material for the food industry. Microcapsule products used as raw materials for the food industry are mainly obtained by embedding unstable food active ingredients in the matrix of edible materials to obtain microcapsules to achieve the edibility of the material, while improving the stability of the material and having certain efficacy. However, this method is complicated.
A microencapsulated magnesium oxide and a preparation method thereof are provided for solving the above technical problems. The method comprises the following steps:
Mix the sodium starch octenyl succinate solution and magnesium oxide powder evenly under stirring to obtain a mixture, add liquid hydrogenated palm oil to the mixture, and perform emulsification and shearing treatment on an emulsifying shearing machine to obtain a shearing mixture;
Spray-dry the shearing mixture to obtain microencapsulated magnesium oxide;
Magnesium oxide: hydrogenated palm oil: sodium starch octenyl succinate are added in a mass ratio of 10-5:4-2:1;
The mass ratio of sodium starch octenyl succinate to water in the sodium starch octenyl succinate solution is 1:15-30.
Liquid hydrogenated palm oil is hydrogenated palm oil solid in a water bath at 80-90°C until it melts. Melting under this condition has a high melting efficiency and a good melting effect.
The emulsification and shearing treatment conditions are: treating at a speed of 2500-3000r/min for 15-30min. Shearing treatment under this condition can form an amphiphilic surface on the surface of magnesium oxide, thereby improving the solubility of magnesium oxide in water and reducing the sedimentation rate.
The temperature in the spray drying step is 190-200°C. Continuing spray drying under this condition can improve the solubility of the obtained particles in water, reduce the particle size, and form a porous structure on the outer wall of the particles, which is conducive to dissolution.
The method specifically includes the following steps:
1) 600g of hydrogenated palm oil is melted in a water bath at 85°C to obtain liquid hydrogenated palm oil;
2) 200g of sodium octenyl succinate starch is added to 4kg of purified water at 80°C to dissolve to obtain sodium octenyl succinate starch solution;
3) 1.2kg of magnesium oxide powder is added to the sodium octenyl succinate starch solution while stirring to obtain a mixture;
4) The emulsifying shearing machine is turned on, liquid hydrogenated palm oil is added to the mixture, the speed is set to 2900r/min, and the shearing time is 20min for emulsification and shearing treatment;
5) The emulsified emulsion is transferred to a material temporary storage tank, and spray-dried at 190-200°C to obtain microencapsulated magnesium oxide. At this time, the solubility, sedimentation velocity and repose angle of the obtained microencapsulated magnesium oxide are optimal.
On the other hand, a microencapsulated magnesium oxide is also provided, which is prepared according to the above method. The method changes the outer wall structure of the microencapsulated magnesium oxide to form a loose structure, and at the same time realizes the coating of the inner core of the magnesium oxide by the outer wall, so that the product has various excellent properties of high solubility, low sedimentation rate and small repose angle.
The repose angle of the microencapsulated magnesium oxide is <30°.
The beneficial effects that can be produced include:
1) The provided method for preparing microencapsulated magnesium oxide uses magnesium oxide fine powder as the core material, sodium octenyl succinate starch and hydrogenated palm oil as the composite wall material, and mixes them in this proportion, and then emulsifies, shears and sprays to prepare magnesium oxide microcapsules. The method is simple, the preparation process is fast and efficient, and there are no pollutants.
2) The provided method for preparing microencapsulated magnesium oxide uses heavy magnesium oxide as the core material, sodium octenyl succinate starch and hydrogenated vegetable oil as the wall material, and prepares magnesium oxide microcapsules through 60mpa high-pressure homogenization and spray drying. The method has a simple process, does not require the use of substances harmful to the human body, and can ensure the edible safety of the product. At the same time, the method uses hydrogenated palm oil and sodium octenyl succinate starch to form an amphiphilic emulsification effect on the outer wall of magnesium oxide, thereby reducing the sedimentation rate of magnesium oxide in the emulsion suspension and improving the processing performance of magnesium oxide in the food industry.
3) The provided microencapsulated magnesium oxide uses a spray drying method to prepare magnesium oxide microcapsules, and the resulting capsules can improve the problem of easy precipitation of magnesium oxide in instant products. Magnesium oxide microcapsules have excellent fluidity and a repose angle of <30°. After the product is applied to instant beverages, it can be evenly dispersed in the medium and has a slow sedimentation rate. Microencapsulated magnesium oxide particles reduce the sedimentation rate in instant products such as milk powder and protein powder, thereby improving suspension stability.
Specific implementation method
The following is a detailed description in conjunction with the examples, but is not limited to these examples.
The materials used in the following examples are all obtained through commercial channels unless otherwise specified.
Examples 1-5: Preparation of microencapsulated magnesium oxide samples 1-5
The preparation method includes the following steps:
1. Hydrogenate palm oil in a water bath at 80-90°C to obtain liquid hydrogenated palm oil;
2. Dissolve sodium octenyl succinate starch in purified water heated to 80°C to obtain a solution;
3. Add magnesium oxide powder to the sodium octenyl succinate starch solution while stirring;
4. Add liquid hydrogenated palm oil and turn on Emulsifying shearing machine, speed setting 2500~3000r/min, shearing time 15~30min;
5. The emulsified emulsion is transferred to the material temporary storage tank for spray drying; the air inlet temperature is 190℃, the air outlet temperature is 98℃, and the atomization frequency is 45hz;
Wherein, the mass ratio of magnesium oxide: hydrogenated palm oil: sodium octenyl succinate starch is 10~5:4~2:1; the mass ratio of sodium octenyl succinate starch to purified water is 1:15~30.
Example 6: Repose angle detection of samples 1~5
According to the existing repose angle determination method: take 50g samples 1~5 respectively, and test them on the standard funnel. The test results of samples 1~5 are the same. The repose angle of typical sample 1 is 26°, and the repose angle is <30°, indicating that the provided material can have good fluidity and is convenient for mixing and processing.
Example 7: Sedimentation velocity test of samples 1 to 5
Take 1g of magnesium oxide, dissolve it in 100g of purified water, stir and mix, and record the sedimentation time. The sedimentation time of ordinary magnesium oxide is 10min. Take 1g of microcapsule magnesium oxide in samples 1 to 5 and dissolve it in 100g of purified water. Stir and mix, and record the sedimentation time. The sedimentation time of samples 1 to 5 is similar, and the sedimentation time of typical sample 1 is greater than 2 hours.
It is explained that the microcapsule magnesium oxide prepared by the provided method can be well dispersed in the solution, avoid rapid sedimentation, and can achieve high stability in the solution.