Abstract
The present invention discloses a new process for producing high-purity magnesium oxide using salt lake brine, which belongs to the technical field of comprehensive utilization of brine. The purpose is to provide a process for producing high-purity magnesium oxide and co-producing sodium sulfate and sodium chloride using natural salt lake brine and sodium bicarbonate as raw materials. The ingredients are prepared according to the equivalent ratio of magnesium ions to bicarbonate ions of 1:2.02-1:2.05, and separated after reaction to obtain intermediate products such as basic magnesium carbonate and mother liquor I. The basic magnesium carbonate is washed with deionized water, and the washed basic magnesium carbonate is calcined to obtain high-purity magnesium oxide. After evaporation and concentration of mother liquor I, basic magnesium carbonate and mother liquor II are separated by centrifugation. After evaporation and concentration of mother liquor II, anhydrous sodium sulfate and mother liquor III are separated by centrifugation. Mother liquor III is cooled and crystallized to obtain sodium chloride and mother liquor IV. The process realizes comprehensive utilization of brine, the reaction process is simple to operate, easy to industrialize and mass produce, high magnesium conversion rate, good product quality, no “three wastes” are discharged during the reaction process, and has good environmental and social benefits.
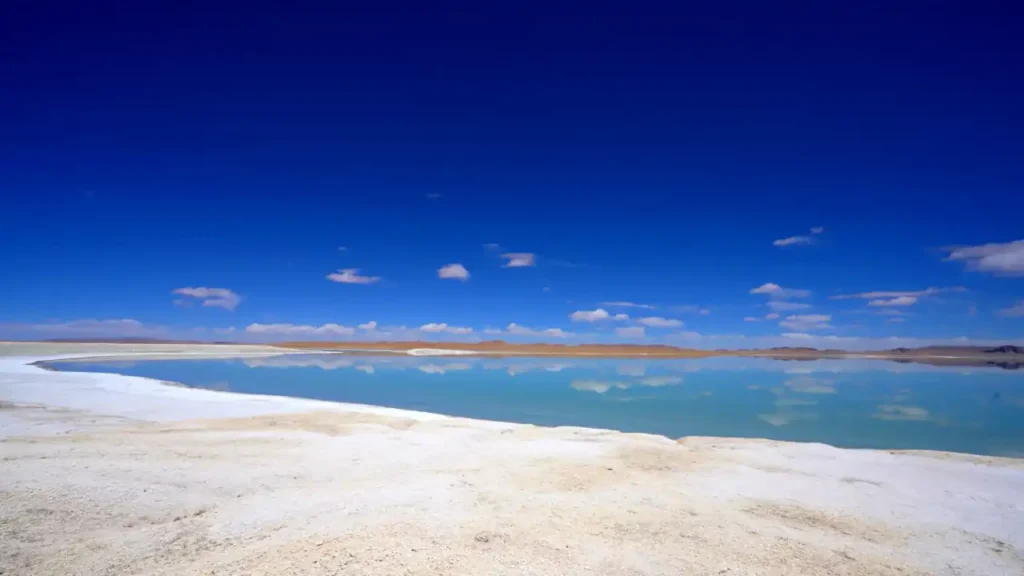
Description
A new process for producing high-purity magnesium oxide using salt lake brine
Technical field
The present invention belongs to the technical field of comprehensive utilization of salt lake brine, and specifically relates to a new process for producing high-purity magnesium oxide using salt lake brine.
Background technology
At present, there are several methods for producing magnesium oxide using brine (sea) water as raw material:
①, the slurry method, including the limestone slurry method and the dolomite slurry method, that is, the magnesium chloride in the sea (brine) water reacts with the lime slurry (made by adding water after calcining limestone or dolomite) to generate magnesium hydroxide, which is then calcined to generate magnesium oxide. This method has low raw material cost and is the most widely used method abroad. For example, Japan and the United Kingdom generally use this method to produce high-purity seawater magnesia. The main disadvantage is that the product contains high calcium and high boron.
②, the ammonia method, using ammonia or ammonia water to react with soluble magnesium salts to generate magnesium hydroxide solution, which is then calcined to obtain magnesium oxide. Its characteristics are that the generated magnesium hydroxide has high crystallinity, fast precipitation speed, and is easy to filter and wash; the technology and process are better than the slurry method. The disadvantage is that the raw material cost is higher than the slurry method, and the boron content in the product is high.
③. Carbonization method: carbon dioxide is introduced into high-concentration magnesium ion-containing brine to generate magnesium carbonate or basic magnesium carbonate under certain conditions, and high-purity magnesia is produced through purification, light burning, processing and heavy burning. A significant advantage of the carbonization method over the emulsion method is that the intermediate product is basic magnesium carbonate, which has better filtration performance than magnesium hydroxide. The disadvantages are: large equipment, large investment, unstable composition of basic magnesium carbonate, and high calcium content in the product (this problem exists when dolomite or magnesite is used as raw material).
④. Direct pyrolysis of magnesium salts: mainly, concentrated magnesium chloride solution is directly thermally decomposed in a high-temperature furnace to generate magnesium oxide and hydrogen chloride gas. The decomposition process is: magnesium chloride hexahydrate is heated to 117°C to start dehydration, and basic magnesium chloride is generated when the temperature is raised to 230°C. When the temperature is greater than 527°C, basic magnesium chloride is hydrolyzed to generate magnesium oxide and water-containing hydrogen chloride gas. The generated magnesium oxide is then washed and purified to obtain high-purity magnesium oxide. Since this method generates hydrogen chloride gas, the equipment is severely corroded at high temperatures, so the requirements for equipment materials are very high. At present, several domestic companies are ready to put into production.
⑤, Soda ash method, using sodium carbonate and soluble magnesium salt to generate basic magnesium carbonate, and then calcining to obtain magnesium oxide. This method is simple and mature, but due to the high cost of raw materials and the low market competitiveness of products, this method is rarely used. All of the above methods have defects in product purity, mother liquor treatment, conversion rate, process equipment, raw material cost, etc. to varying degrees.
Sulfate-type salt lake brine is a four-element interactive system of Na+, Mg2+//SO4 2-, Cl–H2O. Taking the Yuncheng Salt Lake in Shanxi as an example, for many years, it has been following the process of raising brine in summer and precipitating salt in winter, and using decahydrated saltpeter as raw material to produce glauber’s salt. Due to the single extraction of sodium sulfate, magnesium salt is enriched, which not only affects the product quality of glauber’s salt, but also causes a waste of magnesium resources. In order to make full use of salt lake resources and produce high value-added products, using Mg2+ in brine to produce high-purity magnesium oxide and comprehensively utilize the mother liquor is of great practical significance for changing the long-term resource exploitation mode of salt lakes.
Content of the invention
The purpose of the present invention is to provide a process for producing high-purity magnesium oxide and co-producing sodium sulfate and sodium chloride using natural salt lake brine and sodium bicarbonate as raw materials.
The present invention is achieved through the following technical scheme:
A new process for producing high-purity magnesium oxide using salt lake brine, comprising the following steps:
(1) Brine purification: heating the brine to 60-80°C, filtering with diatomaceous earth, and filtering out impurities to obtain refined brine;
(2) slowly adding the refined brine to the sodium bicarbonate solution at an equivalent ratio of magnesium ions to bicarbonate ions of 1:2.02-1:2.05 for reaction, stirring at a speed of 30 rpm, controlling the reaction pyrolysis temperature at 50-80°C, adding time for 1 hour, and reaction time for 2 hours.
(3) The basic magnesium carbonate is washed with deionized water 20-50 times the mass of magnesium oxide at room temperature, and the washing water is recycled. The washed basic magnesium carbonate is calcined at 800-900℃ for 2-4 hours to obtain high-purity magnesium oxide. The purity of magnesium oxide can reach more than 99%;
(4) The mother liquor I is directly evaporated and concentrated, and then centrifuged to obtain basic magnesium carbonate and mother liquor II. The conversion rate of magnesium reaches 98%;
(5) According to the Na+//SO4 2-, Cl-— H2O ternary phase diagram, the mother liquor II is evaporated and concentrated, and then centrifuged to obtain anhydrous sodium sulfate and mother liquor III;
(6) The mother liquor III is cooled and crystallized to obtain sodium chloride and mother liquor IV, and the mother liquor IV is returned to the mother liquor II for recycling. Compared with the prior art, the present invention has the following advantages:
(1) The reaction process is easy to operate and has no special requirements for equipment;
(2) High-purity magnesium oxide is produced using brine and sodium bicarbonate as raw materials, and the reaction and pyrolysis method is adopted. The obtained product has high quality and is stable, and it is easy to achieve large-scale production;
(3) The conversion rate of magnesium can reach 98%;
(4) This process finds an economically beneficial way for the comprehensive utilization of brine;
(5) This process produces sodium sulfate and sodium chloride, and the mother liquor is recycled without any pollution to the environment.
Specific implementation method
Example 1
After filtering the brine with diatomaceous earth, react with sodium bicarbonate, the equivalent ratio of magnesium ion to bicarbonate ion is 1:2.02 (or 1:2.03, or 1:2.04, or 1:2.05), slowly add the brine to a saturated sodium bicarbonate solution at 80°C under stirring, react at this temperature for 2 hours, and keep warm for 2 hours. After filtration, the intermediate product basic magnesium carbonate and mother liquor I are obtained, and the precipitate is washed with deionized water 50 times (or 20 times, or 30 times, or 40 times) the mass of magnesium oxide, and calcined at 900°C (or 850°C, or 800°C) for 4 hours (or 2 hours, or 3 hours) to obtain a high-purity magnesium oxide product.
After the mother liquor I is directly evaporated and concentrated, it is centrifuged to obtain basic magnesium carbonate and mother liquor II. After the above two-step reaction, the conversion rate of magnesium can reach 98%. According to the Na+//SO4 2-, Cl– H2O ternary phase diagram, the mother liquor II was evaporated and concentrated, and then centrifuged to obtain anhydrous sodium sulfate and mother liquor III. Mother liquor III was cooled and crystallized to obtain sodium chloride and mother liquor IV, and mother liquor IV was returned to mother liquor II for recycling.
Example 2
Take 1L of brine with a Mg2+ content of 40g/L and react with a saturated solution containing 228g NaHCO3. Under the condition of insulation at 65℃, the brine was slowly added to the saturated sodium bicarbonate solution. Under stirring at a speed of 30 rpm, the reaction was carried out for 2 hours. After insulation and aging for 2 hours, solid-liquid separation was carried out to obtain 500g of intermediate product basic magnesium carbonate and mother liquor I. After washing the basic magnesium carbonate with 3.5L deionized water, the filter cake was calcined at 900℃ for 4 hours to obtain 57.7g of magnesium oxide with a mass of 99.13%.
After 1.65L of mother liquor I was directly evaporated and concentrated, 70g of basic magnesium carbonate and 0.67L of mother liquor II were obtained by centrifugation. After washing the basic magnesium carbonate, it was calcined at 900℃ for 4 hours to obtain 7.8g of magnesium oxide. According to the Na+//SO4 2-, Cl-— H2O ternary phase diagram, mother liquor II was evaporated and concentrated, and 121.6g of anhydrous sodium sulfate and 0.24L of mother liquor III were obtained by centrifugation. Mother liquor III was cooled and crystallized to obtain 32.5g of sodium chloride and 0.21L of mother liquor IV. Mother liquor IV was returned to mother liquor II for recycling.
Example 3
Take 1L of brine with a Mg2+ content of 38g/L and react with a saturated solution containing 210g of NaHCO3. At a temperature of 70℃, slowly add the brine to a saturated sodium bicarbonate solution. Under stirring at a speed of 35 rpm, react for 2.5 hours. After aging for 2 hours, perform solid-liquid separation to obtain 480g of intermediate product basic magnesium carbonate and mother liquor I. After washing the basic magnesium carbonate with 3.0L of deionized water, the filter cake was calcined at 850℃ for 3 hours to obtain 55.7g of magnesium oxide with a mass of 99.05%.
After directly evaporating and concentrating 1.55L of mother liquor I, centrifugal separation was performed to obtain 68g of basic magnesium carbonate and 0.62L of mother liquor II. After washing, the basic magnesium carbonate was calcined at 900°C for 4 hours to obtain 7.2g of magnesium oxide. After evaporating and concentrating the mother liquor II according to the Na+//SO4 2-, Cl-— H2O ternary phase diagram, 120.8g of anhydrous sodium sulfate and 0.23L of mother liquor III were obtained by centrifugation. The mother liquor III was cooled and crystallized to obtain 30.5g of sodium chloride and 0.20L of mother liquor IV, and the mother liquor IV was returned to the mother liquor II for recycling.
Example 4
Take 1L of brine with a Mg2+ content of 42g/L and react with a saturated solution containing 240g of NaHCO3. Under the condition of heat preservation at 60°C, the brine was slowly added to the saturated sodium bicarbonate solution. Under stirring at a speed of 25 rpm, the reaction was carried out for 2.5 hours. After heat preservation and aging for 3 hours, solid-liquid separation was carried out to obtain 530g of intermediate basic magnesium carbonate and mother liquor I. After washing the basic magnesium carbonate with 4.5L deionized water, the filter cake was calcined at 850℃ for 3.5 hours to obtain 60.5g of magnesium oxide with a mass of 99.25%.
After directly evaporating and concentrating 1.72L of mother liquor I, 78g of basic magnesium carbonate and 0.68L of mother liquor II were obtained by centrifugation. After washing the basic magnesium carbonate, it was calcined at 900℃ for 4 hours to obtain 8.1g of magnesium oxide. According to the Na+//SO4 2-, Cl-— H2O ternary phase diagram, the mother liquor II was evaporated and concentrated, and then centrifuged to obtain 122.8g of anhydrous sodium sulfate and 0.26L of mother liquor III. Mother liquor III was cooled and crystallized to obtain 32.5g of sodium chloride and 0.23L of mother liquor IV, and mother liquor IV was returned to mother liquor II for recycling.